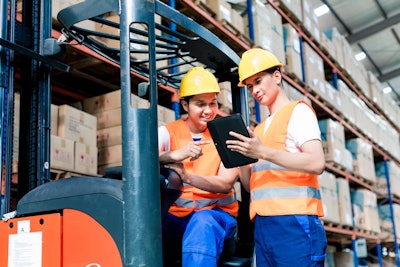
These days, product auto recalls are occurring on a weekly basis. Ford and General Motors (GM) are just a few of the major automotive brands that announced faulty products in recent weeks. While it’s usually these companies—the big brand manufacturers—that take the fall for recalls when they happen, issues can ensue anywhere along the automotive supply chain.
One big challenge contributing to these recalls at original equipment manufacturers (OEMs) is the sometimes hidden complexity of their supply chains. From raw materials to the pieces they turn into, tracking where auto parts are sourced can be exceptionally difficult. In the case at Ford, where a failed fuel pump was identified as the issue, the root cause could have been anything from the fuel pump design to a material failure in one of the components. Tracking down not only what happened, but also where the issue occurred—whether on the engineering table, the manufacturing floor or within the supply chain—is where Ford must look for answers. In that investigation is where its enterprise data management systems come into play.
Systems, such as quality management systems (QMSs) and vendor management systems, are all designed to make it easier to track, capture and record the processes surrounding an organization’s manufacturing. When effectively implemented, that information provides manufacturers a breadcrumb trail to track down what happened (and where), understand the larger problem and, ultimately, make sure it doesn’t happen again.
You’re Only as Good as Those Supporting You
When it comes to enterprise software and its impact on business operations, there’s one thing experience taught me—software systems are only as good as the business processes they support, which in turn, are only as good as the people behind them. Ultimately, those people are only as effective as they are informed (through data) of what’s going on. It’s a symbiotic relationship, so anytime there’s a weakness in the chain, business suffers. For manufacturers, these weaknesses can manifest as low production volumes, delayed shipments or worse—product recalls.
System Communication—Easy as One, Two, Three
- To address these gaps in system communications, manufacturers must ensure that all the underlying technology is sharing the same source information appropriately. When possible, consolidating disparate solutions into a centralized management platform can help with this.
- Take supplier and quality process data as they relate to ISO 9001 and other standards—many of these disparate processes are bound by the same standards and expectations, so it makes sense to merge these systems if there is an opportunity to do so. Though merging multiple platforms seems like a drawn-out process, siloed systems are only as effective as one dataset and make for more work in the long term.
- In cases when this isn’t feasible, ensuring that data is being shared through industry-standard protocols is another way to help ensure all your processes are playing from the same playbook. Data standards, such as OData, can streamline the exchange of information between systems to help ensure a smooth flow of information across systems that support different business units and processes.
Manufacturers were traditionally ahead of the curve when it came to data and processes. As the complexity of the automotive supply chain increases, from a supplier and product perspective, it’s important to regularly assess environments for any potential risk.
It’s time now for automotive manufacturers to apply the same innovative mindsets they do to creating consumer-facing technology and safety features to back-office systems, such as supplier management technology. In doing so, they can effectively reduce the likelihood of risk and issues in the supply chain.