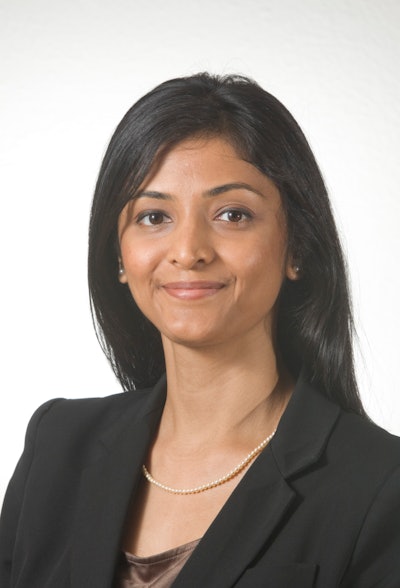
Supply chain failures and disruptions have become more commonplace. It’s no surprise given the complexity of global supply chain today and the increasing number of risks facing companies.
What’s more unsettling, however, is the cost related to disruptions.
The Business Continuity Institute reported in its Supply Chain Resilience 2013 study that 75 percent of the 519 survey respondents experienced at least one incident that caused a disruption in a 12-month period of time.[1] Additionally, 15 percent of respondents suffered supply chain disruptions that cost more than €1 million (approximately $1.35 million U.S.), and 9 percent experienced a single-event disruption that cost in excess of €1 million, according BCI. It snowballs from there—after a disruption, 24 percent said their brands and reputations were damaged; 26 percent saw increased stakeholder concern, and 3 percent witnessed a drop in their share price. If that wasn’t enough of an eye-opener, despite the cost and branding implications, 75 percent of respondents said they did not have full visibility of their supply chain disruption levels.
Concerned about these issues, leading companies are taking another look at their risk mitigation and business continuity planning strategies. They are also carefully considering the revenue impact when critical parts become unavailable and searching for innovative ways to deliver greater return on investment via supply chain resiliency.
Link Between Supply Chain Resiliency and Savings
Companies are doing this for a good reason. Resiliency-building initiatives can save a company a bundle of money and produce recurring annual savings.
Specifically, we see three main areas where resiliency could yield financial savings benefits in the near term: Improved manpower efficiency and productivity, optimized supply chain visibility and better insurance terms.
Efficient use of manpower. Improved productivity, though often seen as a soft cost, could produce tremendous supply chain value when applied alongside risk management.
Under many existing company models, purchasers and commodity managers often spend much of their time doing low-value work. Because of their deep supply chain understanding, these professionals are a frequently tapped knowledge base and are often asked to answer many information requests from colleagues. Additionally, the supply chain group, limited by time and resources, typically manages only about 20 percent of suppliers; those representing about 80 percent of a company’s spend. This opens the company to greater risk since only a small percentage of suppliers are regularly monitored, and usually relegates valuable staff brainpower to tracking quarter-over-quarterly part pricing savings rather than broadly watching for potential supply chain trouble spots.
Savvy companies, however, have begun to see their commodity managers as risk managers, a philosophy shift that has savings implications. One of Resilinc’s customers, for instance, used our supply chain resiliency solution to create a centralized, easily-accessible repository of multi-tier supplier intelligence and made that database available to most of its supply chain practitioner’s companywide. As a result, the number of information requests to commodity managers was cut in half. The decrease in information requests allowed commodity managers to focus on maintaining and building relationships with suppliers. In this case, the commodity managers more than doubled the number of critical suppliers they talked to on an ongoing basis. Additionally, along with the automated visibility into the supplier base, the extra time helped the commodity and supply chain managers identify possible disruptions and act faster when an incident occurred.
By focusing on this human aspect of resiliency, the company saved nearly $5 million, exceeding their cost savings target for the year. It also saw other financial benefits linked to increased productivity on higher-value work, improved supplier interactions and better-coordinated risk management practices across the entire company.
Optimized visibility. An advanced sourcing strategy, driven with a risk management plan in mind, brings with it optimized supply chain visibility along with reduced risks and new savings-generating opportunities.
Though advanced sourcing has been around conceptually for a while, it has been adapted at a slower rate, ironically, because of the risk involved in changing the status quo. Advanced sourcing represents a departure from common supply chain practices where supply chain teams negotiate cost savings with only a few tier-one suppliers; traditionally those suppliers then manage relationships the next tier down.
In an advanced sourcing model where suppliers and their sites are thoroughly mapped and monitored, companies expand their resiliency and establish some level of direct relationships with multiple tiers of suppliers supplying critical parts that, if were not available, would severely damage revenue prospects.
One of our life science customers went this route and uncovered significant savings. It evaluated its supply chain and discovered that a sub-tier provider of an expensive, must-have specialty chemical was used by nine of its tier-one suppliers. This mapped connection sparked a conversation about establishing a closer collaboration with the specialty chemical supplier. Five of the top-tier suppliers agreed to work on this initiative, which resulted in more direct contact with the sub-tier supplier and greater insight into what was happening on that level of the supply chain. In return the chemical supplier got early visibility into end-customer demand fluctuations, and by combining volumes across the five tier-one suppliers, the company was able to get preferential pricing for this critical raw material.
By investing in supply chain mapping as a core resiliency practice, the company saw $3 million in savings, which was shared with its five tier-one suppliers. For our customer, the $800,000 in savings paid for the cost of the mapping effort for four years.
Improved insurance terms. One opportunity that’s often overlooked when considering supply chain resiliency but could represent a notable gain falls under the category of better insurance terms, namely for contingent business interruption (CBI) insurance.
Many companies spend millions of dollars in CBI insurance annually to cover owned and sub-contracted manufacturing sites critical to the company’s production needs; there are different types of CBI coverage depending on how much a company knows about these sites and how well the company can demonstrate these sites’ supply chain and operational importance.
Often companies may know anecdotally which sites are vital, at least internally and within their core suppliers. But they likely won’t know which sites are equally valuable at the component supplier or sub-tier level. From an ROI perspective, this means companies are essentially leaving a big portion of their supply chain uncovered or getting only very limited coverage on unnamed sites.
Typically, the average company pays 10 cents to 12 cents per $100 for CBI insurance. For a $1 billion manufacturer needing $100 million in CBI insurance, that amounts to about $100,000 a year, according to “The ROI of Supply Chain Resiliency: It's More Than You Think” report by Sourcing Innovation and sponsored by Resilinc. [2] However, a company with good supply chain visibility and the ability to effectively map and monitor suppliers and sites across multiple tiers may see their CBI insurance rates reduced to 4 cents to 6 cents per $100, a 50 percent savings that recurs year after year. By showing it’s a lower-risk company, the average $1 billion manufacturer could cash in on about $50,000 in recurring insurance savings, according to Sourcing Innovation’s findings.
Financial Savings Bottom Line
So what’s the big game for resiliency’s potential return? Generally speaking, our work with clients, combined with market research and internally-developed savings calculations, shows that for an average manufacturer with $1 billion in annual sales, resiliency-related investments could potentially save $1 million; on the upside, in certain cases, ROI could range from $2 million to $10 million when factoring in total savings for manpower effectiveness, visibility gains and renegotiated insurance terms, along with other cost avoidance measures.
The cost avoidance issue, in itself, represents one of resiliency’s most appealing recurring rewards.
When a disruption occurs, companies kick into reactive mode, scrambling to assess the immediate damage and then, in the aftermath, to source parts from other suppliers, get factories back up and quickly get products out the door. All of this comes at a hefty price tag.
Comparatively, when companies proactively engage in risk management and resiliency-building practices, those costs are significantly reduced during and after a supply chain failure, as illustrated below. Consistently, over the long term, these costs are avoided and the business keeps moving–both boons for the company’s bottom line and ROI expectations.
Right now it may look like a supply chain play, but ultimately supply chain resiliency and the financial savings it generates will have a far-reaching impact across all aspects of business. How are you going to cash in?
[1] “5th Annual Survey Supply Chain Resilience 2013,” Business Continuity Institute, November 2013.
[2] “The ROI of Supply Chain Resiliency: It's More Than You Think,” Sourcing Innovation, November 2013.