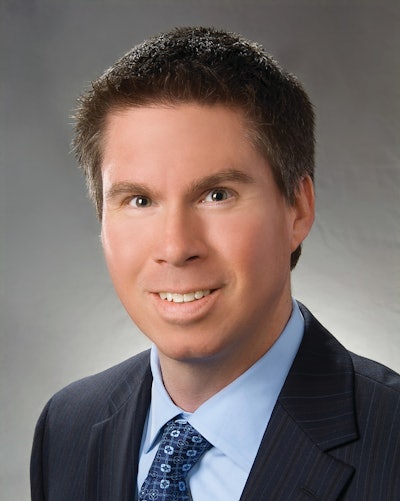
Consider your car for a moment. Do you need your car to run reliably and efficiently to get you from point A to point B? Of course. So, you take care of its basic needs by keeping the gas tank filled and taking it to the mechanic for regular checkups. You may even invest in a new hybrid for greater efficiency. But there is a big difference between your car running efficiently and running responsively. You want to know that when you push the pedal down to the floor, your car is going to respond quickly, and that when you shift into fourth gear, your car reacts. Without your car’s efficiency, you would not make it to point B. However, responsiveness is also a key component in the car’s overall functionality.
Like today’s cars, many companies have perfected how to make their global supply chains run efficiently. But the true test in running a global operation isn’t just efficiency—it’s responsiveness. Unexpected events, such as changes in consumer demand or natural disasters, threaten to undermine even the most efficient global supply chain operations. Operational responsiveness provides companies with the flexibility to quickly react to these types of events and remain a strong player in the supply chain game.
While every industry can benefit from operational responsiveness, one of the most critical is the mobile device industry. Lightning-fast demand shifts and technology upgrades threaten to make a model obsolete in a matter of weeks, and the globally complex supply chain is vulnerable to a number of unique variables. For example, the 2011 floods in Thailand rendered thousands of factories inoperable and many high-tech companies couldn’t access necessary parts since their supply source was hit by the disaster. These companies desperately needed the ability to quickly and purposefully respond.
The difference between an efficient supply chain and a responsive one comes down to the ability to meet uncertain demand. An efficient supply chain can corral its suppliers, manufacturers and retailers to manage orders and processing, and meet a stable, predictable demand at a lower cost. This is done independently and without the ability to address shifts in demand with agility. Conversely, a responsive supply chain works collaboratively among stakeholders to exchange information in a feedback loop in order to produce enough of a product to satisfy uncertain demand.
Here are a few points to consider when re-tooling supply chain operations to better respond to change.
Visibility Means Greater Control
Having real-time visibility empowers a company to manage in real time, which means greater control. Greater operational control allows for the quicker detection of exceptions and disaster, tracking of constraints and commitments, and responsiveness. When business variables are not constant (and they often are not), lead time is everything. A company that has the ability to see inside its supply chain, including work-in-process inventories, can increase its lead time to respond to unexpected shifts and see success.
This can mean that a company is able to quickly pull extra stock from its distribution center and supply store shelves when there is surplus demand. Or, it can mean the company has the foresight to ramp down production to avoid the cost of excess goods sitting on shelves. Imagine the cost of a warehouse full of tablets or smartphones that were suddenly rendered obsolete by a competitive product. This is also referred to as situational awareness—when a company has access to accurate data, both current (point of sale) and historical, to better assess and react to a given situation.
Orchestrating a Holistic Approach Enhances Responsiveness
Adopting a holistic approach to process management is critical to running a more responsive supply chain. Rather than keeping partners, suppliers and functions in separate silos, orchestrate them to be interconnected and in harmony. Creating a networked supply chain community that collaborates can eliminate process latency and more easily allow for greater process integration with information technology (IT) systems, for example. Relying on tools to manage and facilitate supplier collaboration is also beneficial.
These tools can provide a digital platform to:
- Easily share plans, schedules and product information.
- Track supplier commitments and product manufacturing status.
- Monitor real-time product flow through each step of the supply chain.
- Identify and act on exceptions.
Additionally, it’s important to remember to have well-defined organizational roles and responsibilities, and an agreed upon set of performance measurements for communicating across the network. From experience, having the right people can make all the difference. Having the professional skill set, as well as the ability to quickly assess a situation, develop a plan of action, and then communicate and execute that plan across the supply chain, is critical to meeting ever-changing market demands, and therefore, achieving overall customer satisfaction.
Efficiency and Responsiveness Are a Balancing Act
Trade-offs must sometimes be made between efficiency and responsiveness, but that does not necessarily mean efficiency must be sacrificed to responsiveness or vice versa. It’s really about a company finding the right, unique balance. This balance can be determined by factors like what markets the company is looking to source from and ship to, what industry it is in, whether the product is nascent or mature, and whether the product is functional and/or innovative. Take purely functional goods vs. purely innovative goods for an example. Product lifecycles and demand cycles are drastically different for functional and innovative products. Functional products, such as an outdoor grill, often withstand a longer lifecycle and have a predictable demand cycle, so greater efficiency is required.
Innovative products, like a new tablet or smartphone, tend to have very short lifecycles due to the speed of innovation and uncertain demand; therefore, greater responsiveness is needed. However, this situation becomes more complicated when dealing with a functional product, such as milk, that has a short shelf life and needs to be delivered to consumers quickly. Therefore, using market knowledge to forecast demand to the best of a company’s ability and designing a supply chain to be a flexible one-to-one model is crucial to this balancing act.
While overhauling a supply chain model to be more adept at responding to change may seem daunting, the benefits of doing so are impactful—both in the short and long term. Lowering operational costs, reducing risk, scaling for growth to pursue new business opportunities and achieving higher rates of customer satisfaction can all be achieved through a more responsive supply chain. And, much like responsive car care, you’re ensuring the smoothest ride possible.