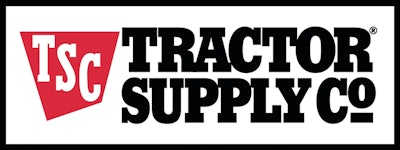
When Tractor Supply Co. (TSC)—the largest retail farm and ranch store chain in the U.S.—sought to expand its supply chain, the company turned to its trusted partner Columbus, Ohio-based Hy-Tek Material Handling Inc., the premier single-source provider of material handling solutions. TSC tasked Hy-Tek to assist in the design and installation of a new $55 million, 830,000-square-foot distribution center (DC) in Franklin, Ky. In turn, the DC would efficiently and effectively store, select and ship merchandise to existing and new retail stores in a multi-state region.
Working shoulder-to-shoulder with TSC’s logistics department, real estate department and general contractor, Hy-Tek served as systems integrator for the Franklin Distribution Center to provide custom design; procurement; installation; and implementation services for all of TSC’s material handling requirements.
“Hy-Tek provides distribution and manufacturing facilities with integrated systems that deliver both efficiency and profitability,” said Donnie Johnson, Vice President of Sales, Integrated Systems Division, Hy-Tek. “No matter what degree of automation you need, we employ the optimum balance of processes, equipment, people and technology to produce the best solution for your business.”
To that end, Hy-Tek sourced and managed proven-reliable suppliers to ensure that conveyors, rack and other material handling equipment fit the building structure, as well as TSC’s needs and goals. In addition to locating and purchasing the right equipment at the most desirable prices, Hy-Tek also assumed responsibility for delivering, installing and testing all material handling equipment.
TSC brings e-commerce fulfillment in-house
Committed to meeting growing consumer demand, TSC undertook the Franklin Distribution Center project with an important goal in mind—to house the company’s e-commerce fulfillment capabilities. Currently handled by an outside vendor, e-commerce is expected to be in-house and operational by early 2013, enabling TSC to handle direct shipments to individual consumers nationwide—controlling service quality and costs in the process.
Mindful of TSC’s e-commerce strategy and the need to individually box and ship consumers’ online orders, Hy-Tek selected and installed pick and pack equipment to help get the job done. It also worked with TSC to ensure that the retailer’s newest and largest DC came equipped with modern conveyor and sorter technology; dense storage systems; and processes adapted to TSC’s challenging product mix.
Added material handling features include voice technology to allow for hands-free picking and labeling— a fast, safe, and accurate approach to order fulfillment. Thanks to a particularly quiet conveyor system, (sourced, selected and installed by Hy-Tek), sorter noise is greatly reduced. Team members can actually converse while standing under the sorter—impossible at older distribution centers.
As a result, the Franklin DC is set up to service its stores quickly and effectively.
The end result
TSC’s Franklin Distribution Center—just one of several projects that TSC entrusted to Hy-Tek since 2008—now provides warehouse space and distribution capacity for up to 300 stores; helps balance the workload among TSC distribution centers in six other states; and supports the company’s steady growth. With nearly 1,200 stores now open, TSC projects a total of 2,100 stores will be operational within the next 10 years.
The retail chain attributes the success of its partnership with Hy-Tek to mutual trust and respect, shared responsibility for results and a commitment to excellence in design and execution.
“Trust is the primary reason we selected Hy-Tek,” said Tom Guschke, Director, Logistics Engineering, Tractor Supply Co. “In a project of this magnitude, trust is all-important. Hy-Tek always delivers as promised. Hy-Tek has the breadth, depth and support capabilities that TSC needs. Hy-Tek does it all, eliminating the need for supplemental vendors. Hy-Tek is a full-service, experienced, one-stop shop.”
With more than 1,000 vendors represented and up to 12,000 items in stock, the Franklin Distribution Center acts as a supply point for TSC stores within a 300-to-400-mile radius, similar to its other cross-country DC’s. Adding approximately 90 to 100 new stores per year, TSC is focused on efficiently expanding its supply chain capacity to support retail store growth; maintain appropriate stock levels; control costs; and safeguard customers’ loyalty and business.
Formula for success
The partnership between TSC and Hy-Tek is a win-win, thanks to Hy-Tek’s proven record of successful integration and implementation.
“There are a lot of integration companies in the U.S.,” said Guschke. “In Tractor Supply Company’s experience however, the success of a project like our Franklin DC depends heavily on implementation. It is critical to use an integrator with the experience, skills and capabilities necessary to deliver on-time and on-budget. That’s what makes Hy-Tek such a valued partner to Tractor Supply.”
On deck for TSC & Hy-Tek is a new distribution center in Macon, Georgia. Additionally, Hy-Tek will begin installing and implementing a material handling system similar to the Franklin DC In January 2013. Slated to be operational by summer 2013, the Macon DC will further enhance Tractor Supply’s ability to deliver quality merchandise, unsurpassed service and fair pricing to its customers—in retail stores and online.