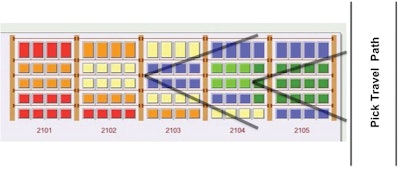
When slotting a warehouse, slow movers are not to be overlooked, as they typically constitute 70-80 percent of total items.
A slow moving item is often characterized as one with few hits, or visits to the pick location. In instances where slow moving items take up the majority of space in a warehouse, it is critical that the items be slotted in a manner that facilitates intelligent slow-mover picking. There are a number of techniques that can be employed to reduce selector travel and to increase pick density including layout configurations, selection strategies, and golden zoning considerations. Through an evaluation of slow mover activity, one can determine the best size for a slow moving area and the picking techniques best suited for that area.
Unit Movement vs Hits: A Common Mistake
We will use the term unit movement to refer to the number of picking units that are picked during the time period under consideration. Hits will refer to the trips to the picking locations. Why is this important? Consider an item with a unit movement of 1,000 and two hits; this means 500 items are picked on each visit to the pick location. Now consider an item with unit movement 100 and 100 hits; this means only one item is picked per visit to the pick location. Although the first item has 10 times the unit movement, it constitutes only two trips to the pick location. Meanwhile the second item has one-tenth the unit movement but 50 times the trips to the pick slot. So it would make sense to put the first item in a slow moving area and the second in a fast moving area closer to the shipping dock since selectors will visit the pick location many more times than the first item.
Pick Path Reduction and Slow Moving Area Picking Techniques
Slow moving areas are often defined by cross aisles in the pick path that allow selectors to avoid travelling the entire length of the pick path, and avoiding the slow moving area all together. For serpentine pick environments, it is common to see cross aisles, usually about two-thirds of the way down each aisle (away from the shipping dock). In this environment it would make sense to slot faster movers before the cross aisle and slower movers after the cross aisle. Additionally, in the one-way, serpentine environment, if a selector uses the cross aisle, he is skipping not only the back portion of the aisle that he is coming from but also the back portion of the aisle he is entering via the cross aisle.
Because of this, the layout of product in the pick line should clearly delineate faster movers in front and slower movers in the back as to increase the likelihood that the cross aisles can be used, reducing travel distance. In addition, as pictured in Figure 1, behind the cross aisle, items should be slotted in a velocity sequence along the serpentine pick path so as to maximize the likelihood of walking only one or two aisles behind the cross aisle. Slotting the fastest 30 percent as well as some “B” movers before the cross aisle typically increases the opportunity to utilize the cross aisle.
A clever approach in a traditional serpentine environment separates the selection operation before the cross aisle from the selection operation behind it. In the front section, orders may be picked by order, perhaps within a wave. This operation handles the fastest movers. Behind the cross aisle, orders are batch picked, gaining significant pick density, and then married to their specific orders on the shipping dock. The trade-off, of course, is the saving of selection travel against the double handling of outbound items. Figure 2 illustrates this approach.
The Clever Solution
Consider a hybrid rack layout where on one side of the pick path are flow rack and on the other side are static shelving in aisles perpendicular to the pick path (see Figure 3). Clearly the fastest movers (and larger items) would be slotted in the flow rack immediately adjacent to the pick path. The fastest, smaller items (requiring less space to keep the targeted days of product in the pick slot) would go into the perpendicular aisles closest to the pick path.
The idea that one level is better than another to pick from can be enhanced by applying golden zone rules to the items and slots at the same time (in a multi-level pick environment). Golden zone rules typically have the fastest of the fast items slotted at a height between the shoulders and the waist. The challenge in the described environment is determining the trade-off between ‘bend and reach’ ergonomics and productivity versus the opportunity to reduce horizontal travel down an aisle. The clever solution involves something called a ‘productivity wedge’, which is pictured in Figure 4.
The advantage of this hybrid approach is that the fastest movers (and larger items) would need fewer facings and/or stackings to maintain the targeted days in the pick slot; hence, the pick path has an opportunity to be shortened.
It makes great sense to focus on the fastest moving items in the pick line when maintaining a slotting layout. This article considers the potential for increasing selector productivity by also evaluating the slower moving items in the pick line. Fixing slower moving items not only frees up valuable space for faster moving items but can also increase the odds that portions of the pick path will not need to be travelled at all.
Dan Basmajian is President of Optricity, based in Research Triangle Park, N.C. For more information, visit www.optricity.com.