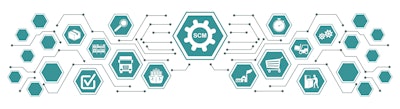
Today’s supply chains face many challenges. They must contend with weather-related disruptions, material and labor shortages, infrastructure problems (e.g., port congestion, channel and bridge closures), increasing freight rates compounded by economic volatility, difficult demand forecasting, changing customer expectations and lack of internal expertise. Where manual processes may have worked years ago, they no longer do. Not only are manual processes prone to human error and inaccuracies, but they also offer no supply chain visibility, transparency or insights into supply chain conditions and shipment movements. They do not allow for the productive, timely exchange of information between manufacturers and suppliers, freight forwarders and logistics service providers, nor do they support positive customer relationships and incur in increased costs.
These shortcomings have 93% of manufacturers planning to increase their resilience across the supply chain and 90% planning to increase supply chain talent in-house (McKinsey). In addition, both manufacturers and suppliers are focused on streamlining their sourcing, quoting and procurement, but recognize that a lack of visibility and disconnected systems are impeding the speed and accuracy of their procurement and supply chain operations. To address current market challenges, as well as the deficiencies of manual processes, organizations are turning to an integrated supply chain approach that leverages technology, including Artificial Intelligence (AI), global networks and customized services.
Current Market Conditions
What manufacturers face in today’s market are increasing challenges and expectations. Global supply changes are evolving, becoming more complex and interdependent, requiring companies to synchronize their operations with multiple partners in disparate locations around the world. Consumers, increasingly shopping online, have expectations of quick deliveries owing largely to the Amazon effect. While sourcing and procurement workflows have accelerated due to the broader application of digital technologies, they still cannot keep pace with current demands. This places additional pressure on manufacturers to meet shipping and delivery deadlines. There are also new pressures on businesses to be more sustainable in their operations and lower their carbon footprints.
According to IndustryWeek’s “The Need for Speed: The State of Manufacturing Procurement,” only 4% of manufacturers indicate it takes up to one week for the average sourcing and procurement process (i.e., from specifications delivery to quote acceptance).
What is at Stake?
There are risks for manufacturers who are slow to change their supply chain models to a more holistic, digitalized approach. It is essential that manufacturers consider the long-term risks involved. Currently, supply chain disruptions and cyber threats are major risks to a company’s operations, even more so than increasing labor costs, employee attraction and retention, and high interest rates. Yet, according to the PwC 2024 “Digital Trends in Operations Survey,” these high-risk areas are a focus of just 52% of manufacturers, while others are more focused on quality (47%), infrastructure and construction (43%), labor practices (41%), traceability (39%), trade (32%), and climate and environment (29%).
There are also increasing supply chain regulations to comply with including Environmental, Social and Governance (ESG) standards, as well as Data Privacy and Security, International Trade, Product Safety and Quality, and Anti-Corruption and Bribery regulations. To mitigate risks and avoid incurring hefty fines, achieve resiliency and remain competitive, manufacturers need to think more strategically and adopt a more integrated supply chain approach which supports all of these areas (i.e., labor practices and workforce productivity, quality, trade, climate/environment).
The Integrated Approach
Developing an integrated supply chain approach streamlines the complete product life cycle,
from the sourcing of raw materials and components to product, distribution, and delivery. It supports collaboration between manufacturers, suppliers, freight forwarders and logistics service providers, while optimizing operations, improving supply chain lead times, reducing costs, and improving sustainability and regulatory compliance. The core elements of a sound integrated supply chain approach include leveraging digitalization incorporating AI and other technologies, accessing experienced digital-first supply chain service providers with global networks, and deploying best practices.
Digital Supply Chain Platforms
On the digital technology front, there are advanced supply chain platforms incorporating AI, Machine Learning, Operations Research and proprietary algorithms that deliver end-to-end supply chain visibility, real-time notifications regarding critical supply chain events and milestones, streamline processes, provide actionable insights, foster seamless information exchange between stakeholders and remove inefficiencies with various ERP environments. They support informed decision-making and collaboration, as well as order management and supplier. management. Collectively, all of these capabilities advance the connected, integrated supply chain enabling manufacturers to access critical data pertaining to their shipments’ status and inventory levels, among other need to know information.
The Right Service Providers
As important as applying digital technology is for achieving an integrated supply chain, having the right resources is also necessary. The right provider will be able to offer fully integrated and cost-effective supply logistics, freight forwarding and supply chain services. They will be able to offer customized services tailored to the customer’s needs. Additionally, they will have developed a global network with strategic global locations in close proximity to their customers and major ports and terminals. In addition, they will have in-house specialists with hands-on experience and knowledge of the intricacies in all supply chain areas, from manufacturing, importing, and exporting to suppliers, cargo airlines, sea freight companies, rail companies, and trucking enterprises. Their broad expertise helps to effectively address market challenges and disruptions such as identifying alternative shipping ports, routes and infrastructure (i.e., airports, seaways, railways and roads).
Best Practices
When asked in a Statista survey what best practices they were adopting to support their supply chain integration, 15.9% of respondents said adoption of operation technology — 14.5% said shift more digital/direct sales, 13.5% said increasing transportation partners, 11.5% said dual/multi-shoring, 10.9% said integration of other/advanced technology, 6.4% said near-shoring, 6.3% said increased volume of inventory, 6.3% said no changes, 5.6% said shrink operations/geographic footprint of inventory, 5.1% said reduce inventory holdings, and 4% said re-shoring production in headquarters country.
While, these practices may make sense for many manufacturers, the key to supply chain integration is a data-driven mindset. Real-time, actionable data and related analytics is foremost to establishing effective supply chain practices. Establishing a culture of collaboration backed by strong communications and data exchange among supply chain partners is also vital to achieving an integrated supply chain approach.
Benefits Derived
Perhaps the greatest gain manufacturers receive from an integrated supply chain approach and the more accurate and reduced lead time and deliveries it facilitates is increased customer satisfaction. The streamlined operations achieved through this approach also result in lower operational costs, increased productivity and worker fulfillment and retention. The insights manufacturers gain from the data analytics delivered via digital platforms also contributes to their ability to optimize inventory management and capitalize on economies of scale and more favorable pricing from suppliers.
The ability to react quickly to market changes and disruptions, optimize their resources and better comply with government regulations and industry standards are all advantages gained from an integrated supply chain approach and an opportunity for manufacturers to gain agility and resiliency in an increasingly more complex market.