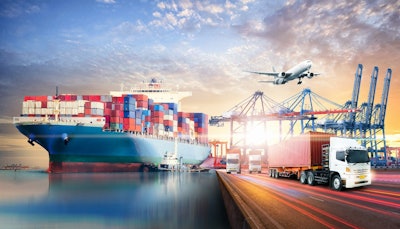
Over the past few years, we’ve seen the strength of the automotive industry’s global supply chains be tested in ways that we could only ever have dreamed of previously. Significant and diverse crises — including the COVID-19 pandemic and the ongoing conflict in Ukraine — have affected supply chains globally. As a result, vehicle sales have been restrained by a lack of inventory, and consumers have been forced to either endure long wait times or settle for purchasing vehicles that lack flagship features.
While the shortage of semiconductors used in onboard vehicle computers has received the most attention, of equal importance to many segments of the automotive industry— including manufacturers, retailers and the replacement market — are the important chemical products and materials like butyl rubber and synthetic base stocks used in oils, lubricants and greases. For example, Butyl rubber products help vehicles maintain consistent tire air retention which contributes to fuel efficiency in internal combustion engines (ICE) and longer battery range in electric vehicles (EVs).
Despite the crises of the past two years, our supply chains has proven resilient and agile enough to meet the automotive industry’s needs. This reliability is not due to luck. Rather, it is the result of strategic, generational investments in analytics, relationships and global capacity.
Using Digital Tools for Improved Logistics Management
When winter storm Uri blasted us living on the Gulf Coast last year with freezing temperatures, the entire chemical value chain worldwide was disrupted. ExxonMobil, for example, overcame that disruption by combining digitalization efforts, and deep institutional understanding of supply chain logistics.
On a macro scale, digitally mapping a value chain — back to our raw material suppliers — can help companies anticipate issues and provide a reliable supply of products to customers. With access to global breadth, doors open to a wide variety of internal and external data sources for market intelligence. This keeps automotive companies one step ahead of potential disruptions and offers the ability to quickly identify potential raw material shortages, and pre-emptively mitigate disruptions for end-user needs.
These digitalization efforts have the ability to pinpoint those areas that lack for multiple sources of the raw materials and lend the ability to pre-emptively find alternative sources of limited raw materials before it affects production. With multiple sources for many of the ingredients used in the production of our products, a value chain becomes more resilient.
Developing Deep Relationships with Suppliers and Customers
Ensuring reliability in the automotive supply chain hangs on the balance of relationships. Creating a “relationship ecosystem” offers a framework to develop strategic partnerships with suppliers — investing in their business to secure supply in the future as a mutual growth connection. These partnerships result in smarter business decisions based on clearer and earlier lines of sight. They have also been particularly important as the auto industry undergoes a profound shift from ICE to EVs.
However, it's not just downstream —it’s important to build deeper relationships with customers to have more transparent discussions about their needs, so we can better forecast demand. Being invested in both suppliers' and customers' long-term success is key to growth and progress. A purchase history with a supplier is not the same as a relationship over the long term. When push comes to shove, and you're in the hardest of times, you can't call on a purchase history — but you can call on a relationship.
Leveraging our Unique Global Footprint and Scale
One of the lessons of the semiconductor shortage is the importance of visibility across the extended supply chain, which digitalization and relationship-building efforts are providing. But, we must also recognize the inherent flaws of just-in-time manufacturing, as it is a methodology that only works with predictable demand and limited supply variability. For example, the ability to quickly react to shifting customer needs during the COVID-19 pandemic helped ExxonMobil ensure capacity, inventory and supply to mitigate risks. As customers encountered supply issues from other butyl rubber vendors, they were able to help them by leveraging their integrated digital value chain and bring supply from other regions.
The size and location of plants are undoubtedly a key component to ensuring a reliable supply chain in the automotive industry so that when one region encounters challenges, other regions can step in and continue to supply products. The many sources of production afforded by a global footprint allow for diversity in maintaining productivity— even in the face of future complications or constraints.
The recent disruptions will only continue into the foreseeable future and will bring both familiar and unfamiliar complications. Future-proofing the supply chain through institutional expertise, advanced analytics, an ecosystem of trusted partners, global inventory, and capacity can bring about long-term resiliency for years to come.