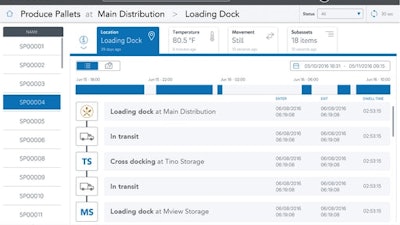
The Coronavirus disease (COVID-19) has had a major impact on the efficiency and effectiveness of supply chains across the world. Even before the arrival of COVID-19 pandemic, supply chain organizations struggled to manage the large workflow of interlinked processes that make up their end-to-end supply chain. In fact, 21% of supply chain professionals name visibility as their biggest challenge. The global, interlinked nature of supply chains makes them more vulnerable to many potential points of failure. This issue becomes critical when disastrous events such as COVID-19 cause a dramatic shift in demand and production requirements.
COVID-19 has exposed glaring blind spots within our supply chains, but 63% of supply chain organizations have yet to deploy visibility technology to help monitor its supply chain performance. Now, organizations are feeling more pressure than ever to adopt new technologies that provide the necessary visibility into their supply chain so that that they can properly navigate adversity and disruption.
Both hard and soft attributes must be tracked
Unfortunately, many organizations think they only need to track hard attributes within their supply chain; these are traditional attributes such as location, temperature, vibration, humidity, etc. True end-to-end visibility accounts for these hard attributes, but more importantly, it accounts for soft attributes as well. There are two types of context for soft attributes: (1) business process context such as purchase orders, payment terms and (2) environmental context, such as weather and traffic conditions.
Hard and soft attributes are directly tied to values and consequences, making them relevant in the context of business. While the link of hard attributes to values and consequences is clear, the same is true for soft attributes, as they can affect the successful shipment of a product. Changes in both hard and soft attributes can impact different aspects of the supply chain. For example, if a contract payment term has changed (a soft attribute) so that a product in a warehouse has not changed ownership, then the liability risk of the potential owner could be affected, not to mention their balance sheet.
It is important to understand that both hard and soft attributes are tied directly to both values and consequences, which make them extremely relevant in the overall business context. By tracking these changes in hard and soft attributes, companies can make more accurate predictions, plan better, make decisions faster, lower risk and increase revenue. If both hard and soft attributes are tracked, blind spots can be eliminated in the supply chain and the progress in value can be clearly observed.
Enabling visibility and tracking
Once organizations are able to track both hard and soft attributes in real time, they can gather all of the relevant data and superimpose it on to a digital model of the various supply chain components, creating what’s known as a digital twin of the supply chain, which allows them to perform real-time analysis. This analytic data can then be used to take timely action, mitigate risk and improve operations and planning.
Soft and hard handoffs
Inefficiencies can occur in two main areas: (1) The transition from one step to another within a function and (2) transition between functions. The first type of transition is termed a “soft handoff” while the second type of transition is referred to as a “hard handoff.” If a delay in the soft handoff is detected, they can be handled with escalations within the organization. Hard handoffs are different, as they occur across organizations. Because of this, they require different intervention methods rather than an escalation within the organizational boundary.
Within an organization, soft handoffs can be handled by soft attribute-based tracking. Every handoff has a “from” state and a “to” state as the workflow is executed. When a “from” state is reached, a notification can be sent to the stakeholder of the “to” state proactively, reducing system inefficiency. For example, if a purchase order is approved in the supplier process, a notification can be immediately sent to shipping so that shipping is triggered without delay. If shipping is not triggered within a specified time, then an additional alert can be sent, or escalated up the organizational structure. If this soft handoff occurs within an organization, an enterprise-wide messaging system can be triggered. Organizations need to pay close attention when a soft handoff occurs across companies, as this is when blind spots occur if they are not tracking these soft attributes.
Hard attribute-based tracking can tell when hard handoffs happen, but when the expected handoff does not occur, it can’t identify the reason as to why. For example, if raw material is loaded onto a delivery truck, sensor-based tracking can detect it. However, if the loading does not occur, hard-attribute based tracking can’t determine why it did not happen and therefore, can’t take appropriate action to move the process ahead. Since soft attribute-based tracking is more granular, it would know exactly at what step the workflow got stuck. By sending a message to the right stakeholder in the workflow, the process can proceed.
It helps to think of the entire supply can as a large workflow of interlinked processes. By tracking both hard and soft attributes, organizations can remove blinds spots, which leads to improved performance management and more accurate predictions.