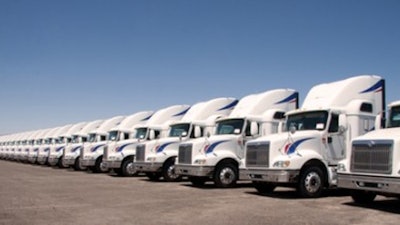
For all the improvements in logistics in recent years, the last-mile delivery problem remains a mystery. The last mile of the supply chain accounts for more than half of total shipping costs, making it the most expensive part of the shipping process. It’s also the most time-consuming. But, with an increase in online shopping, especially during COVID-19, customers expect and demand quick, efficient delivery. If retailers and logistics companies want to succeed during this time, the last mile needs to be a primary focus.
The biggest underlying reason for the last-mile delivery problem is that most of the logistics industry is long accustomed to operating in lag time instead of real time. The industry knows how to follow behind shipments; this works fine on the open road, but inevitably causes delays in the last mile of delivery.
Without real-time information, companies along the supply chain lack visibility, situational awareness, and the ability to collaborate with all parties. For instance, warehouse personnel is often unaware of drivers waiting at a dock to complete a delivery. When a driver reaches a destination, he or she calls the carrier, who then calls the logistics person, who then informs the client. But what if the driver forgets to call or if no one’s on the other end of the line to answer? The driver idles outside until someone realizes the shipment has arrived, and the customer has no clue where the product is or when he or she will receive it.
This lack of interoperability between shippers, receivers, third-party logistics companies and carriers in the last-mile game stems largely from different companies using different technology solutions that make it difficult for two systems to effectively and efficiently relay information. Missing or delayed information is translated to lost time, productivity and money.
What’s more, many logistics companies are still relying on manual processes, paper forms, and traditional communication platforms (e.g., phone calls, text messages and emails) to share information. Employees spend hours checking emails and making calls — playing catch-up instead of acting on real-time data.
If individuals need to add freight to a shipment or go to a different location due to closures, for instance, they might not know for days. But what if they had real-time data at their fingertips and could receive such updates immediately? Technology that enables full visibility and seamless collaboration could change the game.
Collaborative technology is a game-changer for logistics
To make matters even more challenging, there’s a severe driver shortage, which is only expected to worsen. Many carrier companies are scrambling to find the resources to meet growing shipping demands. Even if the pandemic miraculously ended today, online sales would remain robust as the retail industry evolves. And, while widespread unemployment may attract some new truckers, it’ll take time to recruit and train the mass number needed to close the current deficit.
All of these challenges may present hurdles for companies along the supply chain, but they also present a massive opportunity for companies that can solve the last-mile delivery problem now. Logistics companies need a way to make last-mile delivery more efficient and cost-effective, but the pressures of the current pandemic also require solutions that are easy to implement and relatively affordable. Companies should look at collaborative logistics tools capable of connecting stakeholders along the supply chain with actionable, real-time information.
Last-mile delivery technology that connects customers, fleet operators, third-party logistics providers and C-suite executives can go a long way toward solving the associated problems. Empowering these stakeholders to exchange information in real time creates opportunities to improve efficiency, boost productivity and enable innovation.
On the most basic level, connecting a driver or logistics provider and the warehouse where a shipment is headed allows for more efficient and precise scheduling. Perhaps the most exciting opportunity that collaborative technology presents, however, is the ability to glean more data along the supply chain. Stakeholders can use this information to run analytics and identify any areas of improvement. For example, monitoring driver detention times across a fleet is the first step to minimizing that metric.
Adopting a collaborative mindset
As supply chain executives seek out the right collaborative technology and think about how to implement it, the following steps can help form a strategy that will support all stakeholders in last-mile delivery:
1. Don’t be afraid to share information. Many carriers are hesitant to hand over access to their real-time data, but when all involved parties can share information seamlessly, operations will run more smoothly along the entire supply chain.
Provide real-time information and visibility to all concerned parties through a shared portal that consolidates all relevant operational data. Any collaborative technology tools you implement should also enable supply chain collaboration among all parties involved, including shippers, receivers, warehouses, manufacturers, executives and customers.
2. Eliminate fears over job loss. When companies implement new technology, many employees see it as a sign that automation is taking over, and they fear they will lose their jobs to it. But that’s not the case with collaborative technology in the supply chain. It doesn’t replace the work that humans do in the office or on the road. It just makes manual, repeatable tasks easier and allows teams to spend more time doing knowledge-based work that can help grow the business.
3. Start small. You don’t have to adopt all the new tech tools at once. Starting small can actually help you have a more successful implementation. Find a tool that allows you to focus first on one driver, one load, one shipment, etc. Implement the technology first on this small scale, and test it out for any blind spots or failures in the workflow.
Address these on a case-by-case basis. Then, when you’ve worked out the bugs, ramp up deployment to include more drivers and assets. You can uncover untapped capacity and efficiencies that can lead to more opportunities for growth.
Just because the last-mile delivery problem has historically been the thorn in the side of the logistics industry doesn’t mean things must stay that way. Solutions — and savings — exist now for companies willing to embrace new technologies and, most importantly, work together as collaborators.