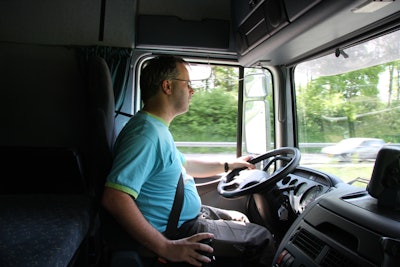
Editor’s Note: The following article is brought to you by Echo Global Logistics in partnership with the Supply Chain Network.
When the Department of Transportation mandated that the trucking industry install electronic logging devices (ELDs) in 2015, there was legitimate concern that tracking driver hours would raise prices and exacerbate supply problems, but no one thought the resulting data could also be beneficial. For Echo Global Logistics, ELDs have become a powerful and largely untapped source of big data.
For Echo client Newell Brands, a global consumer products company whose portfolio includes well-known brands such as Rubbermaid, Coleman, Sunbeam and many others, ELD data revealed processes that had elevated shipping prices. Thanks to a partnership with Echo, who analyzed the data and made recommendations for improvement, Newell has contracted lower prices, improved relationships with carriers and become a shipper of choice.
Newell’s story illustrates how big data has matured from a trendy buzzword to a force for transformation in the logistics business. In this article, I’ll discuss the problems Newell faced, how Echo investigated and the impact of the ELD study.
The Pricing Dilemma
According to The Washington Post, the U.S. has a shortage of at least 51,000 truck drivers. The squeeze has raised prices and increased volatility for shippers like Newell. Steven Judge, manager of Corporate Transportation at Newell Brands, contacted Echo for help. How could Newell get more predictable pricing?
In a tight market, you must strive to be a “shipper of choice,” the one carriers want to work with. ELDs have made truck drivers even more selective. A driver who sits at the yard for four hours eats up more than a third of the daily 11-hour driving limit. In general, drivers are only paid when they’re moving a load. Thus, shippers who stick drivers into holding patterns eventually can’t find drivers or end up paying a premium based on anticipated delays. In a recent survey across Echo’s carrier base, Echo found that almost 25 percent of carriers had terminated business with a shipper due to loading and unloading delays.
Big Data to the Rescue
Newell suspected its yards were turning around drivers too slowly and tried to analyze its turnaround times, but faced a roadblock. Its recent acquisition of Jarden introduced six new transportation management systems and six additional enterprise resource planning platforms, making analysis complex.
Judge analyzed changes in Newell’s detention charges but ran into a blind spot. Detention charges only kick in if a driver spends two hours or more in the yard. A driver held for one hour and 50 minutes would not be compensated for the time and would likely be very frustrated by the outcome.
At Echo, we hatched an idea: why not mine data from ELDs to evaluate Newell’s yards?
Our analysts used geofencing parameters based on the latitude and longitude of warehouses. We managed to pinpoint shipments that originated from or delivered to Newell warehouses. Within a month of starting the conversation with Judge, our study was completed.
Applying the Data
On average, drivers spent 102 minutes in 37 surveyed shipping yards. The team studied problematic yards to identify processes causing long turnaround times. The analysis also pointed to yards that were performing well above average, allowing Judge to discuss best practices that could be scaled across the organization.
One facility not performing as well didn’t begin to pick loads until the drivers arrived. The yard supervisors were afraid that drivers would miss their appointments and jam up the warehouse.
Judge introduced these supervisors to their peers at a warehouse that preloads shipments. The supervisors from the above facility learned how to stage shipments and print bill of ladings before drivers arrived. After updating their process, the supervisors communicated to drivers that if they arrived on time, they’d get out of the yard much faster.
The Results
Turnaround times dropped about 30 percent to an average of 72 minutes. At the yard that introduced preloading, average loading time dropped by 50 minutes and detention charges were eliminated altogether in Q3.
Even as Newell increased truckload and intermodal shipments by 16 percent during the peak season, the company kept detention spending flat. Indeed, 70 percent of its facilities lowered detention spending within three months of the study.
Newell tracks detention spending relative to overall truckload spending each quarter. After this metric hit between 10 percent and 15 percent during Q1 and Q2, it dropped to less than 5 percent in Q3. For Q4, Newell is on track to lower the ratio even more.
“It was a mentality shift,” said Judge. “We didn’t know this data was out there and usable. We no longer feel vulnerable for not knowing, and there’s so much data we still haven’t tapped.”
The Echo-Newell study illustrates how practical big data can be. Armed with insight, logistics professionals can detect and fix broken processes rapidly. Big data is no longer a technology of the future—it’s a necessity for succeeding in the present.
For more information on how Echo Global Logistics can help you uncover and implement efficiencies in your supply chain, email [email protected].