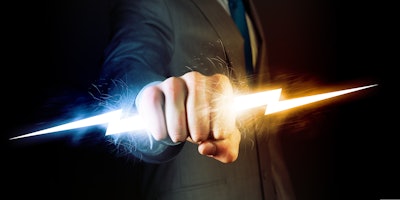
Energy management systems traditionally allow users to monitor their energy consumption, but they don’t make it easy to know what actions to take. With today’s Internet-of-Things-based technology, industrial facilities and warehouses can now take a more tailored and action-oriented approach to reducing energy costs and emissions.
This evolution involves 3 components:
- Real-time energy suggestions
- Equipment-specific and automated actions
- Transparent results
Real-time energy suggestions
Operators can now receive real-time suggestions for reducing energy costs that are customized to their facility. This is a major departure from traditional energy management systems that simply allow users to monitor their usage.
Examples include suggestions for avoiding high electric rates or demand charges. With spot prices now skyrocketing to 100x their normal range during peak periods in many electric markets, these suggestions can pay back system costs extremely quickly.
Managers can also track suggestions across a portfolio of facilities in real time, such as demand response calls from multiple DR aggregators. This enables greater participation in cost-saving programs by simplifying the experience.
Equipment-Specific and automated actions
With real-time suggestions, operators need to be able to respond quickly. Today’s technology helps them do that in two different ways. First, granular data allows for equipment-specific suggestions that indicate exactly what action to take and when, which helps operationalize energy decisions. It’s also now possible to automate these actions to drive even greater participation.
Customized suggestions arise from behind-the-meter data specific to each facility such as IoT meters and sensors, local electric market data, and integrations with warehouse management systems. Recommended actions from this type of system may include curtailing specific equipment or making specific process adjustments. Now operators can meaningfully affect energy costs by adjusting their behavior in real time – for example, by temporarily shutting off certain compressors.
The next step is to automate. With a simple text message approval, qualified personnel can now take recommended actions even if they’re not at the control panel. For example, Automated Demand Response helps take the guesswork and urgency out of DR participation. This is made possible through integrations with control systems.
Transparent Results
Today, companies can both estimate and verify the impacts of their energy decisions. They can also share those results in a much more transparent way, both within and outside the organization.
With location-specific data, it’s possible to calculate the expected savings from each suggestion. That way, operators have enough time and information to evaluate the benefits of each action. This is especially important when considering curtailment so the benefits can be compared to any costs of lost production, where applicable.
The impacts can then be seen in real time, rather than waiting for the utility bill. This helps operators make smarter decisions, and it also helps organizations verify compliance with programs like Coincident Peak and Demand Response. With primary-source data, it’s not uncommon for companies to uncover and rectify utility bill discrepancies.
Digitized data can also be shared with other permissioned users like suppliers, customers, and regulators. This is becoming increasingly important as companies are requesting energy and carbon data from entities up and down their supply chain, driven in part by Scope 3 reporting regulations.
Proactivity is a Major Paradigm Shift for Facility Managers
Industrial and supply chain operations typically involve complex processes and equipment that can’t be ramped up and down easily. They also typically operate around the clock, unlike commercial buildings that have predictable occupancy patterns and can be programmed accordingly. And of course, they must balance the need for uninterrupted production with energy efficiency.
In this type of environment, facility-specific suggestions represent a major shift in energy management practices. Rather than guessing what works, operators can now take the specific actions that make sense for their facility – and even automate those actions. This means energy can be managed proactively, with transparent and verifiable results.
Managers can evaluate these suggestions holistically across a portfolio of facilities spanning multiple utilities, contract types, and even currencies. This makes it much easier to participate in energy and demand management programs. The resulting savings not only improve operating margins, but also reduce impacts on the grid and drive down carbon emissions.
Operating in the Green: Proactive Emissions Management
During peak periods, it’s not just costs that go up. Grid operators also turn on older and less-efficient power plants that normally sit idle, leading to substantially higher carbon emissions. Reducing demand during these periods can be an important way for companies to reduce their emissions.
However, most companies today are not able to track these effects. Carbon accounting traditionally uses annual emissions factors to translate energy use into CO2-equivalent (CO2e). With real-time data, it’s possible to track emissions on an hourly basis, allowing companies to authentically claim credit for reducing demand during peak times.
And as with energy management, recommended actions for reducing carbon emissions can now be automated to drive greater adoption and reduce the burden on operators. This helps facilities drive energy and sustainability improvements while maintaining their focus on production.
Thanks to advances in energy management, facilities now have a new tool in their belt to not only reduce costs, but also drive down greenhouse gas emissions in a credible, transparent way.