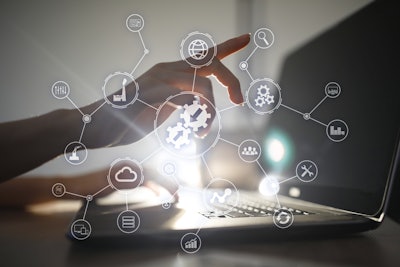
Businesses around the world are facing some gnarly economic headwinds these days, so lots of companies are looking for ways to increase efficiency to bolster the bottom line — and manufacturing companies are always looking to drive costs out of their supply chain.
Time is money. It’s common knowledge, but many businesses operate without bearing this wisdom in mind. And I believe the adage provides beneficial insight for businesses looking to improve their supply chain management operational efficiency.
Now, there are many ways to get a more efficient supply chain, and the right approach depends upon your company’s size. For the purposes of this article, there are ways small to medium-sized businesses can reduce their costs of procurement. If you’re one of those companies, here are three practices to get more bang for your buck out of your supply chain.
Question Sourcing Conventional Wisdom
Conventional wisdom dictates getting at least 3 bids for every component, then picking the lowest price or lowest lead time (depending upon your company’s constraints). It’s time to start questioning whether that strategy is effective in an economic downturn. Getting all of those bids makes cutting costs simpler and more obvious, but there’s an opportunity cost that comes with the traditional approach. Finding 3 (or more) vendors, contacting them, and obtaining quotes from each takes a lot of time, and slows your time to market — and remember, time is money!
What if your focus was just to get quality parts in your engineers’ hands so that they can learn, iterate and get your products to market sooner? Increasing supply chain efficiency isn’t so straightforward as direct cost saving on cheaper quotes or reducing the labor cost of a supply chain manager — you’ve got to consider the opportunity cost of slowing your time-to-market and the revenue delay that comes with it.
And prices aren’t the only thing to consider when it comes to evaluating costs. Are you factoring in the quality and performance of your parts? Because parts delivered cheaply that end up non-conforming get expensive when you have to take extra time and effort to have them remade.
Use Different Supply Chain Management Practices for New Product Development and Production
Too often companies are focused on reducing material spending when they should optimize for organizational costs and time-to-market. For example, let’s say you have 10 engineers making $150k each, who work 250 days a year — you’re spending $6k per day in people costs on this team alone. Now, you can either save $2k on materials they need for NPD or spend the $2k to get parts a week sooner. The second option saves you $30k in people costs by having them work on the project instead of waiting for the cheaper parts — the math is pretty simple, spend the two grand.
One of the most common failure modes seen is when companies apply production supply chain practices to new product development (NPD). To be clear, you shouldn’t have the same supply chain goals for NPD and production.
The problem with the one-size-fits-all approach is that it slows down development cycles and hinders innovation. In NPD, time-to-market is absolutely critical, and validating designs and de-risking products through high-quality component testing are how you build products that last and can scale. But if you’re using production procurement practices, you’re funneling every order through a supply chain team optimizing primarily for cost reduction, not speed or quality.
And does removing 5% of costs in production have the same impact as removing 5% of costs in NPD? Probably not. Spending more on NPD parts to get higher quality is worth it to validate designs faster.
To accelerate NPD you need to streamline your workflow, which means deleting unnecessary steps that move info from one source to another. The traditional method has engineering release CAD designs that supply chain personnel must download and send to suppliers to get quotes. Then suppliers send their quotes and DFM feedback to the supply chain team, who then forward it back to engineering — and if changes to the design are needed, the process repeats itself. It’s arduous and unnecessary.
A more efficient setup is to have engineering go straight to the supplier to order parts and let the supply chain department manage material spend and relationships with vendors.
The Solution
The goal is not to eliminate the role of the supply chain team in your business, it’s to eliminate supply chain’s non-value-added tasks transferring information back and forth — and get supply chain collaborating with engineering efficiently. And, of course the supply chain team needs to know what’s going on with procurement — but there are digital platforms (like Fictiv) that provide the kind of critical visibility they need to manage costs while letting engineers drive procurement for projects.
With the right partner, your engineering and supply chain teams can work in parallel instead of in series. And remember, more efficient use of your teams’ time translates to better financial performance — especially if you’re a pre-revenue startup, where your NPD must optimize for getting to market ASAP.
The bottom line is, regardless of the macroeconomic environment, speed wins in business. So build your NPD supply chain to move fast.