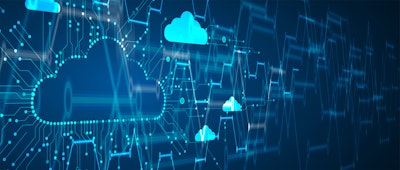
There’s a lot of information out there on the level of demand volatility and the fragile nature of the supply chain. Now ask yourself “why,” given the level of investment that has occurred to improve supply chain operational performance.
Establishing a data-driven supply chain
The challenges frequently accompanying today’s supply chains – such as disruption, risk and lack of communication – require evolved solutions. However, to date, most Manufacturing 4.0 efforts have been focused on the internal supply chain. By leveraging digital tools, manufacturers can better see and control their operations, build more agile and resilient processes and create a scalable business model.
However, digital solutions cannot stop in-house – especially given most supply chain data originates from outside an organization's enterprise systems. This means that more focus needs to be put on creating an agile way to integrate external partner data. A lack of operational data visibility and multi-enterprise collaboration capabilities in the external manufacturing and packaging supplier supply chain network can cause major inefficiencies.
It’s important to keep in mind that when brands attempt to manage variability and risk with their partners, a seamless integration between all partners is critical to drive true agility in the supply network and robust resilience to recover quickly from disruptions. Luckily, there are tools and technologies to help improve visibility and enable seamless partner collaboration and communication. As it has been proven over the last several months, unfortunately not enough companies have truly connected these partners to deliver these critical operational capabilities.
Multi-enterprise supply chain capabilities can provide network wide real-time visibility of critical information such as capacity, inventory, order status, quality and performance metrics. This makes it easier for brands and their network of manufacturing and packaging suppliers to quickly plan, analyze, execute and collaborate to quickly respond to changes and disruptions.
Leveraging external supply chains
The quest for the holy grail is end-to-end visibility, however achieving real-time visibility and collaboration is more difficult than ever. When leveraging external partners, brands need assurance around product quality, sustainability and on-time and in-full performance to minimize risk for outsourced orders.
There are repeated examples across industries of the need to bring partner operational data focused on production plans, schedule conditions, capacity and current available or committable inventory into client planning and scenario analysis to drive better operational and financial decision making. For example, in the fast-moving consumer goods (FMCG) industry, a company should be looking to work with partners that have the technology in place to quickly track and trace products in the event of a recall. If not, the risk profile of what will need to be included in the recall and the number of affected partners goes up exponentially.
With the volume and speed at which FMCGs are produced, recalls can be catastrophic if they are not caught in time or if there is insufficient data from the production process, both of which make recall more extensive and expensive. A digitized production floor can capture real-time information, including component lot data, line and machine data, date and time data, etc. and can share accurate recall data quickly and efficiently, cutting down on the time it takes from identifying a recall to remediating it – all while also reducing unnecessary product waste.
Building a more sustainable supply chain
With environmental, social and governance (ESG) investing expected to surge in the wake of the pandemic, sustainability is top of mind for many organizations. However, lack of material and capacity visibility into external supply chains, as a result of manual or legacy systems, can lead to higher waste and less “green” operations.
Blind spots within the supply chain can obscure information related to waste, costs and inventory, which not only contributes to inefficient work, but also drastically reduces a partner’s sustainability. A multi-enterprise platform drives cross-company process collaboration and data visibility, shining a light on opportunities for improved sustainability across the ecosystem. For example, visibility into raw materials and finished goods available across all the partner operations can improve the movement and usage of the right materials at the right time, reducing potential shortages and avoiding waste from unnecessarily duplicate safety stocks and/or replenishment orders that do not need to be triggered. Lean, agile, data-driven supply chains run more efficiently, freeing up time to sustainably innovate and deliver products more responsibly to consumers.
The quest to manage variability and risk while maintaining quality requires seamless external partner programs built on data visibility and collaborative process management. Multi-enterprise platforms can help brands achieve visibility and collaboration, maintain trusted partner networks, ensure sustainability and reduce the likelihood and impact of recalls.