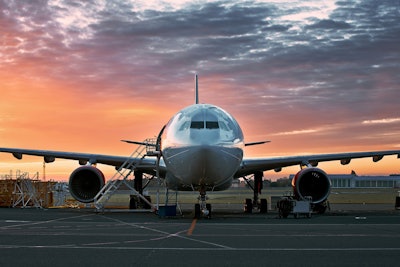
Boeing 737 Max mishaps have been dominating the news the past several months. Back in January, an Alaska Airlines door plug blew out mid flight due to loose bolts, forcing Boeing to pay the airline company $160 million in losses. In March, the windshield of another Alaska Airlines Boeing 737 jet cracked. The FAA is also currently investigating claims made by a whistleblower raising concerns over the manufacturing quality of the 777 and 787 aircrafts.
These incidents suggest major manufacturing quality issues on the shop floor, which serves as a ‘last-mile’ blind spot where significant vulnerability carries through to end-user scenarios that keep bubbling up, plaguing the industry and threatening safety. To resolve this issue, influential players like Boeing should address this directly by adopting modern solutions on the shopfloor and creating higher standards for quality and safety.
Data From The Factory To The Runway and Beyond
Aviation and aerospace manufacturing leaders need real-time visibility to critical granular and contextualized data across the supply chain, from the shop floor to the airport runway, to ensure optimal operability, predict machine downtime, and avoid jet recalls. One small deviance or abnormality in the manufacturing process could mean the difference between life or death. As such, aerospace and defense (A&D) manufacturers need to digitize their entire operations from the factory to the runway to collect data in real-time and contextualize it to find blind spots. They must adopt modern solutions that help improve quality control, predictive maintenance, and perhaps most importantly, personnel safety, before another airline mishap occurs.
To do this, manufacturers can harness big data to provide better operational and business insights and minimize habitual errors. Big data plays a critical role in the manufacturing shop floor and is used to track all production processes and improve equipment productivity. But according to industry analysts, only 25% of the aerospace manufacturing shop floor is digitally connected, severely limiting the amount of data a manufacturer can use. The remaining 70-80% of the factory is dependent on legacy analog equipment and manual processes that require human-enabled data reporting, or worse yet, ill-informed assumptions of what is being done in those areas.
By capturing environmental and equipment condition data, such as vibration, temperature, humidity and battery usage throughout flights and while idle, A&D manufacturers will gain critical information to help make decisions about maintenance issues, minimize cargo damage, and improve overall aircraft health. While an individual aviation manufacturer can control everything inside their aircraft, they will have to communicate with multiple airports and suppliers to capture data across the supply chain as multiple vendors are usually required. However, there are still areas in a manufacturer’s control that can have a dramatic impact on data availability.
A&D Asset Tracking and Digital Twins
To start, A&D manufacturers should precisely monitor equipment locations and maintenance schedules with advanced IIoT asset tracking solutions. By enabling real-time tracking of technical operations assets, aviation companies can optimize tool and equipment availability, reduce misplacement, and enhance operational efficiency. Using IIoT sensors and beacons attached to specific assets such as vehicles, assembly parts, and safety devices will allow manufacturers to digitally report on location as well as location history, which will improve timing of availability and operation use. This will provide useful data of trends over time so manufacturers can make better informed decisions and improve productivity and safety across the factory and the airport.
Lastly, by creating a digital twin of their entire operations, A&D manufacturing leaders can fill data blind spots on previously undocumented machinery and processes to improve accuracy of business intelligence analysis. With the help of IIoT sensors attached to physical equipment, manufacturers can capture everything from vibration, motion, temperature, voltage, and more. This will help ensure machine health, longevity, and safety for inside the aircraft and across the airport. Connecting the digital twin to the cloud will vastly enhance visibility throughout the supply chain and improve decision-making.
Ready for Take Off
To transform aviation asset management and digital twin technology inside the aircraft and across the airport, manufacturers must first understand the challenges and potential for improvement. IIoT solutions such as asset tracking and digital twin can unlock previously hidden data blind spots. The more complete, timely, granular, and contextualized the data set, the more power will transfer to manufacturing operations executives looking to make real-time decisions. If successful, this will translate into operation, safety, and profit improvements. By following these steps, aviation companies can revolutionize asset management and digital twinning, optimize resource allocation, fill data blind spots, enhance transparency and accountability, reduce costs, and ensure FAA compliance. Hopefully, this will result in improved manufacturing processes and a safer future for the flying public.