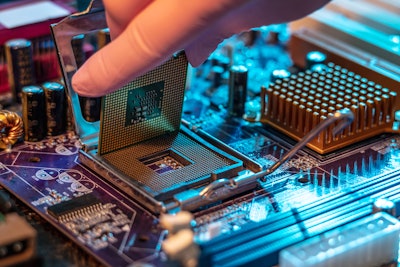
While media coverage of the U.S. semiconductor shortage has been focused primarily on the commercial sector and threats to the nation’s competitiveness and economic health, the country faces equally dangerous risks from shortages that compromise military readiness and national security. Each of these risks must be addressed, but their roots and remedies are entirely different.
Defense and national security
Beginning several decades ago, two things transformed the semiconductor industry and have put the defense and aerospace sectors at risk. First, semiconductor manufacturers by the dozens abandoned these markets to pursue the higher volumes of commercially-driven consumer applications. Then, to more cost-effectively support these higher volumes, they transitioned to subcontracted overseas manufacturing, mainly in Taiwan and China.
The first issue is as concerning as the second. Simultaneous with the U.S. share of global semiconductor manufacturing dropping from 37% in 1990 to 12% today, there has been equally alarming drop in the number of the U.S. companies who design and supply these mission-critical semiconductors.
Industry consolidation accounted for some of the decline. Most of this consolidation has led to a de-emphasis of Department of Defense (DoD), NASA and other government engagements since accretive acquisitions typically result in cuts to these generally peripheral portions of the acquiring company’s business. Microelectronics suppliers were also being lured to more lucrative commercial state-of-the-art (SOTA) opportunities, and today, the number of semiconductor companies with a meaningful defense sector businesses has shrunk dramatically.
This dearth of suppliers is as much of a risk to the U.S. defense and aerospace sector as the offshoring of so much U.S. semiconductor manufacturing to China and Taiwan, which became an even greater concern after he trade war with China began. This was followed by increasing aggression in the South China Sea and Hong Kong, and the actions and statements made by the Chinese Communist Party in the early stages of the pandemic. U.S. policy needs to address both the commercial and DoD sector issues by creating an environment that incentivizes private investment for onshore manufacturing – not just of SOTA components, but also mission-critical semiconductors.
An important first step is the bi-partisan American Foundries Act and its successful addition in July 2020 as an amendment to the Senate’s Fiscal Year 2021 National Defense Authorization Act (NDAA), which also includes provisions of the original bipartisan CHIPS for America Act for semiconductor incentive and R&D programs that was authorized but never funded. Also important is the Endless Frontier Act that was expanded in May 2021 and renamed the U.S. Innovation and Competition Act (USICA). It includes $52 billion in emergency funding to implement the CHIPS Act and allocates $2 billion to “solely focus on legacy chip production to advance economic and national security interests, as these chips are essential to the auto industry, the military and other critical industries.” The price tag on the bill at one point ballooned to over $250 billion which has caused it to slow down for further debate prior to being passed in the Senate.
The next step is to change the NDAA language so that it also includes the mission-critical and integration-level semiconductors required for military and aerospace applications. This addition would better support the fragile global supply chain for Pentagon-military and space qualified semiconductor manufacturing applications and integration. This qualification process is substantially more rigorous than that in the commercial sector. For instance, devices like field programmable gate arrays (FPGAs) used in for onboard satellite payload processing need to be qualified to reliability specifications geared to extremely harsh space environments. The same is true of military and space-qualified discrete semiconductors that are the staples of weapons and space system platforms. In some cases, they are 60 years old but still desperately needed by both prime and sub-prime contractors.
Fewer and fewer companies supply these products or are even capable of meeting their qualification requirements, which creates the potential for looming capacity and capability constraints. In short, the military and aerospace market simply does not have the sales volumes to support the continuing technology investment required to attract suppliers. U.S. policymakers must address the massive resulting gaps that have created today’s shrinking military and aerospace electronics supply chain.
Commercial sector
The commercial sector shortage has continued to worsen and the current order rate is outpacing the capacity that semiconductor companies can bring on board. It is a constraint the industry will likely see through the rest of the year, most likely into 2022.
The issues that created this crisis have been brewing for some time, dating back to late 2018 and early 2019 when tariffs started to create headwinds for many customers. They could not absorb the tariffs and their end consumers could not bear the prices, so demand went down in 2019. And, then as things began to improve and supply chains realigned so that products destined for the United States could be built outside of China, the industry was hit by the Coronavirus disease (COVID-19) pandemic through the first half of 2020. It added to the demand slide especially in the automotive, industrial and consumer sectors. Everyone stopped buying.
As the slowdown happened, companies leaned out inventories and started to idle factories to run less than what they could normally produce. Moving forward through the slowdown, manufacturers could not get a demand signal from their customers that provided enough warning to start up manufacturing again. This is problematic for an industry where it takes six months of cycle time from when there is a “go” signal, as there was in September 2020, to when factories can be ramped up and/or capital investments can be made to expand capacity, and production can begin to return to full force again. The industry has had to catch up from where it was back in late 2019 and early 2020.
Today’s supply issues are exacerbated by manufacturers who compete over the same fab capacity. This can be tracked back to the transition from vertical integration to predominately fabless manufacturing. As fab construction costs skyrocketed, many semiconductor companies moved to a “fab-lite” model, shifting their resources to chip design. They produced some chips in their own fabs while outsourcing some production to foundries. Some went fabless or they exited the business. Then the 2001 recession hastened an industry contraction, which launched a consolidation chapter while also accelerating offshoring. The result has been a much weaker industry ecosystem today, that was far more vulnerable to the whipsaw impact of the recent pandemic.
Policy priorities
The commercial sector will continue to see supply and demand imbalances resulting from normal economic cycles. But, there are also policy initiatives in the medium to long term that will be important to support a stronger U.S. semiconductor infrastructure, including both R&D and manufacturing capability. The biggest issue is the manufacturing side, which will likely take at least three years to address once government initiatives are launched. Meanwhile, it will likely take at least 6-8 quarters to resolve the commercial shortage, not just in automotive but across all end markets.
To ensure availability of microelectronics for U.S. defense, aerospace and homeland security needs, policymakers need to consider the special circumstances of this increasingly fragile, dedicated supply chain. Modifying the NDAA bill to include support specifically for mission-critical and integration-level semiconductor suppliers is a first step toward shoring up a shrinking supplier base so it can continue to provide components that pass the rigorous qualification tests that ensure they can be used in much harsher environments for much longer periods of time than the typical commercial semiconductor.