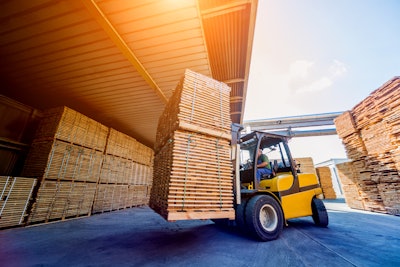
This year the price of homes and new builds skyrocketed, as a lumber shortage made its way throughout the United States. It is yet another impact from the Coronavirus (COVID-19) pandemic, one of many examples throughout that shows just how much impact the supply chain has throughout all facets of business.
But how has a virus caused the housing market to skyrocket while lumber and building materials run dry? Like so many disruptions in the supply chain this past year, it is a multitude of factors coming together.
One of the most discernable reasons is lack of personnel to physically source, mill and transport lumber and other building materials due to social distancing requirements as well as COVID-19 outbreaks themselves.
“Increased demand and lower supply,” says Rita Ferris, president of the Northeastern Retail Lumber Association. “The lower supply is due to manufacturing challenges. The manufacturers are having difficulty obtaining product and manufacturing products due to reduced staff. Issues impacting staffing are lower numbers of staff working to prevent COVID illnesses and reduced staff when COVID illnesses occur. There are also occasions when manufacturers are closed down (depending on where they are located in the world).”
At the time that lumber plants had difficulty with staff, consumers stuck at home increased their interest in projects, and in turn purchasing more building materials.
“The sudden need/desire for residential homeowners to take on home improvement projects was a contributing factor in lumber shortages,” says Bob Mewis, principal engineer at Gordian.
More than COVID-19
These same factors plague other material sectors such as steel and aluminum as well.
But for the lumber industry, it is not just the pandemic that brought a decrease in materials. Many reports throughout the past year say that climate change is a contributing factor, especially regarding a spruce beetle which has flourished in North America due to warming climates. In a conversation with Bloomberg, David Elstone, owner of Vancouver-based Spar Tree Group, says that the issue reduces the British Columbia Interior’s lumber product output by 40%. According to the World Integrated Trade Solution, Canada is one of the lumber exporters to the United States.
With all this adding up to a perfect storm to cause a serious lumber shortage, the lumber supply chain now has the extremely difficult task of managing pricing.
“The retail building material supply industry is quite concerned with the volatility of prices,” adds Ferris. “There are times where the price of lumber increases each day so it’s challenging to provide accurate quotes to customers far in advance. In some cases, the quotes are good for a few weeks now instead of 30 days. Just think about quoting a job today, but you’ll be filling the order in 30 days and you have no idea what the real price of the commodity will be.
“Retailers do their very best to hold price quotes, but it’s difficult. They don’t want to quote too high and turn away business, but they also don’t want to quote too low and end up losing money. The extreme volatility is not good for retailers and consumers.”
Mewis explains that the lumber shortage will likely be around until COVID-19 is completely under control.
As this problem remains, its impact is far reaching, says Ferris.
“Everyone is connected in the industry,” she says. “Manufacturing challenges impact distributors, retailers, contractors and consumers. The increased price of lumber is driving up the price of housing. It also puts contractors in a difficult position when they can’t get their products in a timely, cost effective manner. It has never been more important to communicate expectations throughout the supply chain.”
The building material shortage and the dramatic growth of housing prices is only one very public example of how disruptions in the supply chain disrupts daily life and business. Since last year’s toilet paper catastrophe, we will likely continue to see similar outages until the pandemic subsides.
Click here to hear more about the supply chain for the trades and construction: