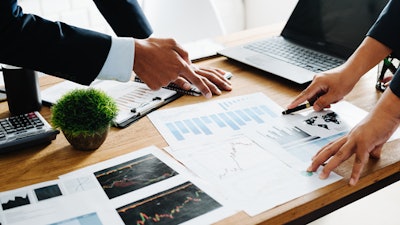
Today, every global manufacturers’ CEO, CFO and COO are leading virtual “war rooms” to respond to supply disruptions, demand spikes, supplier risk and ensuring their employees’ well-being.
At the exact time when multinationals’ supply chain leaders need to be front and center identifying and resolving supply chain disruptions, most are relegated to advisor roles, focusing on building resilience on the fly and identifying ways to cut costs. Why? Because they don’t have the data-driven insights to systematically predict and mitigate risk.
Despite investing millions over the last several years, supply chain leaders are being hampered by their technology platforms. Multinationals, with complex, multi-step, multi-geography supply chains, have been unable to capture the critical data from suppliers and sub-suppliers two or three tiers down in the chain. And, instead of leaning on the best of the digital technology toolkit, supply chain leaders are relying on antiquated spreadsheets, historical data and news reports about continuing disruptions in key production and logistical hubs.
So, how do supply chain leaders flip the script, and quickly.
When the Coronavirus disease (COVID-19) lockdowns first began impacting manufacturing hubs in China and South East Asia, companies began manually mapping out their our entire just-in-time supply chain network to identify potential disruptions that could impact customer service, fulfillment, manufacturing and transportation, using unstructured data.
That’s why having an automated, AI-driven visual dashboard that overlays the number of COVID-19 cases, deaths and hospitals by country, state and city with internal data helps improve customer demand, orders, inventory and logistics to better predict disruptions in real-time.
Disruption to multinationals’ supply chains will continue well beyond this pandemic. To build resilience, evaluate supplier risk and adapt quickly to swings in demand, supply chain leaders must do three things:
1. Integrate external real-time data feeds to deliver a 360-degree view of risks and opportunities.
While every company invests in market intelligence, nearly all of it is entirely static -- PDF reports based on backward-looking data and assumptions renders the information effectively useless today.
Instead, chief supply chain officers must partner with their IT teams to deploy a single portal with independent data verified by third parties who are commercially on the hook for the quality of that data. The external data feeds ¾ all readily available today ¾ should include public health information such as John Hopkins University’s COVID-19 map, commodities pricing, weather forecasts, port and factory closures, along with financial information about key suppliers. Since the biggest direct suppliers are usually publicly traded and must report material financial data, it’s straightforward to integrate feeds to continually assess their financial health. By integrating external intelligence feeds with its internal data, including orders, inventory, shipments and supplier information to scan for predictive patterns, companies can identify potential issues and provide realistic alternates.
2. Use AI/ML to deliver visualized insights for data-driven decision making.
The bigger challenge is not integrating external data feeds, but rather, improving the quality of their internal data. Most global manufactures have been unable to capture and maintain the extensive volume of data required to fully map their end-to-end supply chain. Frontline employees like requisitoners and warehouse staff do not find the technology intuitive, adoption falls short, and the data is generally dated and inaccurate. As a result, the data not only doesn’t support decision making, it actively erodes supply chain leaders’ creditability.
Instead, companies can apply this same AI/ML analytics to predicate customer demand to the supply chain. By making assumptions to fill any gaps in supplier data, integrating 2 years of direct and indirect spend financial information and 2 weeks of external COVID-19 data can accurately forecast disruptions and conduct scenario planning.
3. Iterate rapidly and deliver quick wins
No organization has 9 months nor millions of dollars to spend on implementing new solutions. The key to success is to accelerate development and use out-of-box business intelligence tools. Building a prototype while simultaneously engaging business leaders to solicit feedback, drives adoption and validates the quality of internal data.
The pandemic has shocked world trade, forcing companies to rethink their strategic approach and diversify suppliers. But, globalization is not going to slow down. It is becoming far more complex. Trade tensions, tariffs, the increasing intensity and frequency of natural disasters will multiply the risk to companies’ global supply chains. By providing a visual, real-time reporting portal that combines external data with the company’s internal demand, inventory and supplier risk assessment, supply chain leaders will deliver actionable insights to navigate uncertainty. Plus, it elevates the chief supply chain officer to strategic leader within the c-suite. It’s not only entirely possible with minimal investment, it’s an imperative.