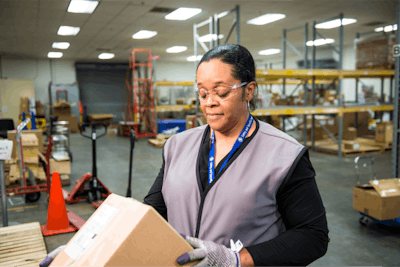
The success of any supply chain begins before any one request or procedure is even put into place. Problems arise in the supply chain when there are weaknesses in forecasting and planning, as well as incomplete or inaccurate information gathered along the way that lead to higher costs, delayed timing and unsatisfied customers down the line. To avoid these setbacks, conducting a comprehensive analysis of operations can help establish a strategic roadmap, and investigate inefficiencies or issues ahead of time.
In February 2015, Savannah River Nuclear Solutions (SRNS) was looking to refine its current supply chain roadmap and implemented a companywide lean management system, known as SRNS FIT or the Focused Improvement Transformation, to aid in continuously improving performance, cost and delivery.
SRNS is a Fluor-led company, whose members are Fluor Federal Services, Newport News Nuclear and Honeywell, and is responsible for the management and operations of the U.S. Department of Energy’s (DOE) 310-square-mile Savannah River Site (SRS), including the Savannah River National Laboratory, located near Aiken, South Carolina. Dedicated to maintaining the highest possible safety and security standards, SRS is a key DOE industrial complex responsible for environmental stewardship, environmental cleanup, waste management and the disposition of nuclear materials.
Lean consultants from Simpler Consulting assisted SRNS supply chain management (SCM) with FIT by addressing specific problem areas with lean philosophies and problem-solving tools. This is accomplished through designing a transformation specific to the needs of a company and then playing an active role toward its implementation, creating a culture of continuous improvement (CI).
A cross-functional team of subject matter experts, customers and a member with an outsider’s perspective conducted the SCM value stream analysis (VSA) to lay out how the process currently works, how it should work and how it could look in the future. The supply chain team recognized that process weakness, combined with complex reviews and approvals, resulted in delays in purchase orders and delivery, as well as increased costs.
The SCM VSA team used the A3 process to develop an implementation plan that included 10 rapid improvement events (RIEs), 11 CI projects and four Just Do Its to address concerns with the overall procurement cycle time, and to improve buyer and user proficiency within the supply chain. Each RIE session took place over the course of one week, and involved a team applying lean tools for identifying waste and making immediate improvements.
SRNS reduced the purchase order cycle time for approved requisitions by 50 percent, reduced the number of significantly aged requisitions by 84 percent and decreased the number of requisitions in process by 65 percent. In addition, the time it takes for an item to go through receiving inspection was reduced from an average of 14 days to three. Twenty-nine percent of employees at SRNS are actively engaged in FIT-related activities and are seeing the benefits as their work processes are improved.
To date, all 10 RIEs for SCM are completed and the total cost savings from FIT activities exceeds $2.4 million annually.
“Transformation and innovation are essential to our company’s success in identifying and executing new missions in a changing environment,” said former SRNS President and CEO Carol Johnson. “The FIT initiative has been a roadmap for improvement, and helped us achieve cost savings and eliminate non-value-added steps, making everyday tasks easier for employees in our SCM organization, while their customers benefit from reduced cycle times and enhanced materials and services.”