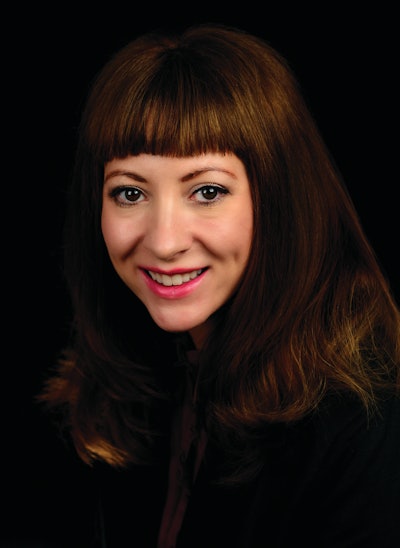
In the past few years, the amount of data that companies must assimilate, transmit, analyze, and archive has grown to such a critical mass that the process requires intelligent, effective management tools and processes to stay competitive. And that trend isn’t reversing anytime soon. According to a report published by analyst firm IDC in 2010, by the year 2020 the amount of digital data will be 44 times the amount in 2009.
Yet this preoccupation with quantity has created the recent hype surrounding big data and technologies designed to process astronomical volumes of information. All the attention paid to data volume has often obscured the critical business concern wrought by the phenomenon. That is, the business need is not just about how to process quantity, but specifically about intelligent solutions for accomplishing the increasingly difficult task of sifting out the relevant data amidst so much “noise.” Then companies need strategic management processes in order to turn the raw data or “information” into actionable business intelligence for effective, measurable performance improvements and predictive analytics.
Although it has commonly been used by tier-one companies for historical trend analysis, Business Intelligence (BI) is increasingly transitioning into a powerful tool for real-time decision making on the most critical supply chain functions. Previous business intelligence solutions were too expensive and too complex to implement and manage for the budget, data volumes, and capabilities of mid-market supply chain organizations. However, the recent influx of mid-market, packaged BI offerings provides powerful solutions for a variety of supply network users without the expense or complexity typically required at larger companies.
Options for Mid-Market Business Intelligence
The mid-market’s tendency toward nimbleness—due to more centralized management and less bureaucracy than larger firms—provides the ability to quickly implement business decisions based on analytic data. This nimbleness bolsters a company’s resiliency in the face of disruption, and a properly selected BI tool enhances speed and agility even further. Mid-market businesses should consider the following qualifications when choosing their BI tool:
Ease of Use
BI tools that make it easy for any user or decision-maker to quickly sort and interpret data will provide the most value for mid-market supply chain organizations. Some SCM applications, such as OneSCM, already contain embedded BI tools for analyzing data from connected systems, providing even further value through the combination of automation, collaboration, and analytics.
Look for solutions that additionally contain these advanced analytic functions in an intuitive, dynamic display:
- Data Sorting—The ability to choose each criteria to display, as well as to arrange the order and combination. For example, a user could select which suppliers, and what details such as company name, address, contact, PO number, and shipment dates, to display and in what order.
- Drilling Down—The ability to sort data according to hierarchies in order to make comparisons at a glance. For example, a user could first view the invoice totals for a fiscal year, then for a certain quarter, and then could drill down to view the invoice totals from each supplier in that quarter.
- Filtering—A filter allows users to sort criteria using advanced logic, such as values between, greater than, less than, equal to, or not equal to a set of criteria.
- Interactive Reporting – Dynamic reports allow users to click on displayed results for more information, or to modify criteria in the report with the click of a button.
- Supply Chain Access—Web-based self-service access to suppliers and other partners in the network build relationships, improve overall supply chain productivity, and ultimately increase end customer satisfaction.
Efficient Reporting
In the past, BI tools were only used by IT professionals and other technical specialists. Today, due to the advance of user-friendly interfaces, these tools are accessible to most business users of SCM applications. To best leverage the capabilities of BI tools for accurate, timely reporting, the following steps are recommended:
- Identify which supply chain software users need to generate reports and analyze data.
- Determine the types of standard reports to create so that users can generate them on-demand (e.g., standard supplier performance reports, invoice history, purchase order history, etc.).
- Ensure that your BI tool is configurable and flexible so users can create custom reports, define data points, and display resulting data in a variety of formats, such as bar graphs, maps, charts, or tables.
- Once a solution is implemented, provide training to target users.
Dashboard Functionality
Companies of all sizes are grappling with the question of how best to use and display data in order to easily meet the needs of their business, industry, and users. Dashboards are an increasingly popular choice due to visual data representation and a host of options in the market that provide dynamic display capabilities.
The enthusiasm for visual analytics in the form of dashboards is due to the recognized role they play in quickly providing more data and trend insights than traditional text-based formats to a variety of business users. Text-based reports and spreadsheets tend to obscure key issues and trends with an overload of tabs, columns, numbers, and text. Dashboards, in contrast, provide an “at-a-glance” image that delivers easily comprehensible trend and issue information. Over time, it gets easier to see where the trends are headed, so decision-makers can spot critical issues and problem areas – and respond to them – far sooner than if they were waiting for weekly, monthly, or quarterly reports and crunching the numbers after the fact.
Data Integration
When BI solutions use integrated data to provide a single version of the truth, users across the manufacturing enterprise gain access to accurate information at the right time, enabling consistent and efficient operations and fulfillment. Companies increasingly face the need to integrate supply chain data from various systems such as multiple ERPs or division/ department databases (due to M&As or company growth). The best integration method for each company will vary based on specific requirements, but a data integration layer that accurately maps fields for supply chain operations is a critical prerequisite for harnessing the best value from a business intelligence application.
Data Security
Data security is the biggest concern to most organizations when determining how to share information across the enterprise and with external vendors and suppliers, often analyzing information using web-based tools and applications for better performance. This is especially true with cloud and mobile deployments. Unfortunately, this concern can lead companies to resist implementing BI tools or maximizing their use of data sharing.
Cloud-based application security continues to improve, however, and recent research suggests that data security in the cloud can often exceed security provided by individual companies hosting their own data. Cloud data storage vendors are dedicated to continuous monitoring, security assessments, and robust staffing for instant response to install patches or address any other problems that arise.
The global, networked economy operates non-stop, every day of the year. Combined with the accelerated pace of doing business, the exponential increase in data quantities and types, and consumer expectations of rapid fulfillment, selecting and implementing a BI solution is a mission-critical imperative for supply chain organizations who want to stay competitive. Many growing, mid-market supply chain companies share the goal of being able to quickly and easily access and interpret data for better strategic decision-making and competitive advantage. The strategies outlined above should help mid-market organizations feel more confident when they begin shopping for their BI solutions.
Virginia Morgan serves as a product, research, and industry content expert for TAKE Supply Chain Solutions supply chain collaboration and data collection product offerings. She is focused on delivering easy-to-understand user manuals that help customers get the maximum utility from TAKE’s products, and thoroughly studying the supply chain solution marketplace to help our product team develop competitive next generation solutions.