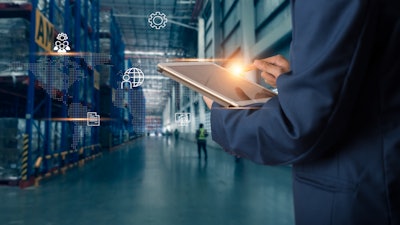
Peak season has historically been the benchmark to measure against in the process of improving warehouse logistics management. The stresses of increased customer orders and meeting short delivery windows provide warehouse managers with critical information on how to handle the workload under even the most challenging circumstances.
While peak season can still provide these insights and numerous worldwide challenges have added to the immense hurdles a logistics workforce must face. The ripple effects of COVID-19, numerous geopolitical shifts, supply chain stagnation and mass labor shortages added atop the steady increase in ecommerce shopping have made logistics challenges an ongoing issue, essentially creating a never-ending peak season.
As a recent Gallup poll revealed 57% of consumers have experienced significant delays in receiving purchases. Warehouses staying flexible and incorporating efficient fulfillment processes to help offset any delays that may happen on the carrier side is essential. Adapting with the labor they have and finding new ways to increase productivity to accommodate the ever-shifting demand is crucial to support omnichannel fulfillment into 2023 and beyond.
Evolving supply chain challenges
The transition of retail stores shrinking to make way for ecommerce has created additional challenges for warehouses. Customers preferring the online option equates to fulfillment centers needing more labor to meet the demand, only to find a shrinking labor pool. A 2022 Instawork survey revealed 73% of businesses have had problems attracting employees, a statistic that has nearly tripled from the year before.
Many warehouses are still prone to working through the logistics process manually and now with less talent. Working in this traditional manner is slow and inefficient and it increases the probability of human error. Worse, labor morale is affected by long shifts and the heightened physical danger of using heavy push carts to perform associate duties.
While major ecommerce players have invested heavily in warehouse technology to capably handle increased demand and meet tight shipping windows, small to mid-size businesses and third-party logistics (3PL) providers need to find ways to adapt to survive. Although it feels like an uphill battle, finding effective ways to keep up and meet customer expectations is possible when adjustments are made in the warehouse.
Incorporating automation
Adding a flexible autonomous element to an existing fulfillment infrastructure can provide immediate relief without disrupting the warehouse as a whole.
One type of automation experiencing rapid growth over the course of the last five years is autonomous mobile robots (AMRs). Customizable robots guide the picking process, in turn reducing the stress and exertion felt by warehouse workers. For instance, overall employee productivity can be improved by 25% and walking time is cut in half on average. The human-first solution allows labor to excel, from a morale boosting perspective which in turn attracts and retains talent, while mitigating risks of incorrect picks or manual equipment failure.
As the number of SKUs increases year over year, the ability to safely and accurately pick orders optimizes overall warehouse performance. Order picking accuracy with AMRs can reach 99%, which results in far fewer quality issues and cost savings overall. AMRs are one piece of automating the wall-to-wall fulfillment process and reassessing warehouse components further is valuable in staying flexible.
Reevaluate infrastructures
Another way to combat the increasing fatigue felt by fulfillment operations is to reevaluate the warehouse infrastructure as a whole. Identifying blind spots in the warehouse can illuminate problem areas for rehabilitation. As the peak season now comes in waves, there is added value in having the ability to learn and change as you go.
Automating capacity management by leveraging technology is a data-driven solution. Ongoing warehouse analysis is necessary to keep tabs on slow-moving inventory and overall space utilization. Incorporating capacity management tech ensures systems are performing accordingly while flagging problem areas – saving the time and energy of manually identifying extraneous issues.
Additionally, leveraging open-source technology and cloud-based services lets a warehouse share data through APIs. This allows seamless data collection from warehouse information systems for full infrastructure comprehension. Having an overall awareness of the warehouse and its place in the supply chain greatly benefits all parties involved, especially when changes are happening on the fly.
Modernizing the warehouse
A technologically progressive warehouse is able to sustain peak season and any unknown challenges around the bend. Reaching out and finding a helping hand with a fulfillment platform can handle all aspects of logistics operations from port to porch, enabling stronger communication across all elements of the supply chain and ensuring better overall accountability. Delegating through fulfillment allows a warehouse to realign focus, letting someone else do the heavy lifting. Additional benefits like lowering shipping costs, increasing shipping speeds, streamlining data and operations and more take off a substantial burden from a warehouse.
Additional tools worth leveraging are smart mobile devices and tablets, giving labor the tools and resources needed for an optimal working environment. Smart devices can be used to scan barcodes, find shipment locations, view important receiving data, generate reports and more all in real-time. Ensuring all parties in the same network have access to the same data keeps everyone on track and minimizes unwanted surprises on the warehouse floor.
Embracing AI or machine learning
Artificial intelligence (AI) can be a great asset to a logistics warehouse. A McKinsey report noted the successful implementation of AI helps businesses improve logistics costs by 15%, inventory levels by 35% and service levels by 65%. When identifying key business drivers, machine learning can evaluate the best ways to improve. Analyzing aggregated data points within the warehouse can automate important decision-making processes to highlight and streamline, be it safety and productivity or fulfillment time and accuracy.
Machine learning provides results in user-friendly data visualizations and other formats that allow actionable insights. What once took an entire devoted team to analyze and manage can be done instantly with AI, freeing up time and energy to best support the everyday tasks of the warehouse.
Prepping for the future
Having faced so many hurdles in the last several years, warehouse operators can only imagine what unknown challenges lurk around the corner. Today’s climate calls for flexibility to respond to whatever may lay ahead. As technology becomes more widely accessible for implementation, the time is now to incorporate it for everyday use to combat any problems that may come in 2023 and beyond. Ecommerce has no plans of slowing down, so mitigating a crisis by staying flexible will only help warehouse efficiency and brand longevity in the future.