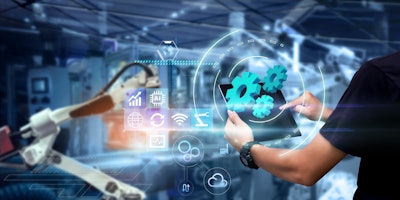
Warehouse automation and robotics solve for several pressing industry challenges. From staffing shortages and a booming rise in e-commerce to the gradual shift to Industry 4.0, AGV and AMR technologies will continue to play a pivotal role in warehouse operations for years to come. In fact, one estimate shows 4 million warehouse robots are expected to be installed in over 50,000 warehouses by 2025.
This rise in adoption and investment is significant because it will bring great shifts in efficiency across the supply chain. To put that in perspective, it’s currently estimated that 50% of the time consumed in order picking is spent traveling within the warehouse or distribution center. If a warehouse employee spends half of their working day walking to locate the item to be picked, that’s time that could have been spent more productively or strategically. AGVs and AMRs come into play by automating these simple, repetitive tasks, freeing up workers for other tasks while maintaining output.
The proliferation of AGV and AMR technologies in the space is encouraging, but a critical component isn’t discussed enough: charging strategies. Rather than an after-thought consideration, your AGV and AMR charging strategy should be intentionally planned and thought out in order to keep your technology investments running smoothly and delivering a maximum return.
Here’s where to start in optimizing your approach.
1. Identify Your Specific Charging Needs
The first step to optimize your warehouse robot charging strategy is considering your goals with the robots. What actions will they take, and what does the typical workflow look like? Consider the size of your AMRs and AGVs and take inventory of the space and environment where the robots will operate. Do they need to follow a tight path, or does the warehouse allow more room to roam? Finally, determine their travel needs and if you will require a configurable footprint. Addressing these questions will help you assess the best charging options for your needs.
2. Consider Your Charging Options
One of the most important elements of your charging strategy and ensuring your robots work effectively is choosing the best charging infrastructure. There are many different options, including conductive or inductive solutions and charging contacts or wireless charging. Here’s what you need to know about each to make the best decision for your operations.
Conductive charging uses contacts instead of wires. This conductive power transfer replaces the conductive wires between the charger and the charged device with conductive contacts. These contacts maximize operational time by taking advantage of opportunity charging for batteries any time equipment is stationary. Charging contacts eliminate the need for manual or automated battery swaps and manual plug-in charging – optimizing profitability and productivity.
The latest inductive chargers are optimized for Lithium batteries and have a constant interaction between the onboard battery management system and the inductive power supply. As opposed to conventional charging methods, conductive charging contacts and “plugged” inductive systems and wireless inductive battery chargers don’t use any plugs or paddles and are intervention free.
3. Be Strategic with Charging Stations
The next way to optimize your AGV and AMR charging strategy is to be intentional with your charging station locations. For warehouses and facilities using robots, it’s ideal to have charging stations set up along their set paths to support continued movement and automation. You want to ensure the charging stations are out of the walking and working path of employees. To ensure the safety of your employees and technology, ensure your charging stations aren’t in high-traffic areas or in places where they could potentially be damaged.
4. Enable Opportunity Charging
Opportunity charging is the practice of charging an AMR or AGV’s battery for short periods during the day rather than fully charging it all at once. Ideal for lithium-ion batteries, this typically looks like charging in shorter spurts whenever the opportunity arises hence “opportunity” charging. The opportunity to charge can occur at staging areas, workstations, loading/unloading stations and turnarounds.
This process is increasingly becoming the standard in the industry for energy supply, as it’s more efficient, ensures robots are readily available when needed, and prevents unproductive downtimes and long charging breaks. Opportunity charging also allows AMR OEMs to have smaller batteries, which decreases the cost and weight of the mobile robot and can improve ROI. If your warehouse AGVs or mobile robots need to be operational around the clock, opportunity charging will be a critical component of your business.
5. Plan for Proactive Maintenance
Lastly, as with any major technology or infrastructure investment, you want to ensure you’re taking care of your equipment. Both the robot itself and the charging components need to be taken care of. There are many experts in the space that can provide best practices and help plan for proactive maintenance. Be sure to select a partner that has a consultative approach and can create a tailored plan for your specific equipment and configuration.
‘Charging’ Ahead
Businesses across the supply chain are finding new ways to increase output, boost efficiency and support revenue operations. Many have turned to mobile robots as new automation in the warehouse environment. Businesses that haven’t already adopted AGVs or AMRs are likely to in the future, as the market is expected to reach $10.6B by 2030. As you approach AGV or AMR adoption, keep charging at the forefront of your strategy.