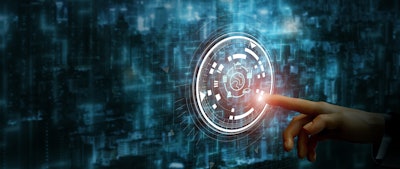
There are many challenging disruptors that must be addressed when analyzing and improving supply chain operations, including labor shortages, a rise in shipping costs and geopolitical issues. The global supply chain upheaval is being felt strongly in the United States, where 43% of U.S. workers are in supply chain industries, employed either at lead firms or their direct suppliers. Softening demand in the B2B space and the potential slowdown in consumer spending means that companies must examine and improve all aspects of how they manage their supply chains to maintain service and protect profitability.
Reengineering business processes enabled through examining current technology solutions is critical to increase supply chain agility and improve efficiency of supply chain execution. Based on years of experience and more than 150 client engagements focused on digitally enabled supply chain transformation, consider the following proven strategies:
1.Strengthen collaboration with suppliers and customers
When it comes to supply chain management, predicting and planning, especially given recent volatility, is beyond challenging. External forces are driving unpredictable volatility and without powerful analytics tools in place, companies are at the mercy of factors beyond their control. Building technology infrastructure that hyper-connects the value chain and drives insights, while reducing or eradicating the crippling of data latency, is foundational.
It is imperative to have systems in place that connect data, including beyond just the four walls of your company, in order to secure visibility and enable timely orchestration across your supply chain. Take for example a Fortune 500 consumer packaged goods (CPG) company who lacked connectivity to co-manufacturer/co-pack partners. This greatly impacted manufacturing and delivery schedules and consequently prevented timely and accurate decision making with retail-driven promotion programs. As a result, the company faced millions in retailer fines, lost revenue and margin erosion through opaque opportunity costs missed in the allocation decision making process. After making improvements to their technology and governance infrastructure, the company raised visibility and predictability to inbound material delays/shortages to more than 85% and improved fill rates to their customers by 11%, while saving over $20 million in fines.
2. Focus on planning and execution
Even the best plans can be rendered obsolete when supply chain disruptions occur. If you don’t have the materials you need, or your suppliers’ delivery schedules are unreliable, the entire value chain is exposed, putting credibility in customer commitments at risk. When your delivery-of-materials schedule changes, new operational models are needed to bring logistics and manufacturing teams together. This also includes extending capacity and feasibility planning models on behalf of critical and most disruptive partners.
To adapt to a new operating model that prioritizes agility and resiliency, companies must redefine metrics, shift tasks and decision-making authority and ensure these adjustments are reinforced by cross-functional senior leaders. Even simple steps, such as installing business data process stewards to monitor and analyze the impact of planning parameters and critical data elements, is often overlooked and undervalued.
The reality is that, in a hyper-volatile business environment, flexibility is quintessential, and efficient enterprise decision-making must be woven into the process and KPI governance. Building in supply network redundancy is very important, especially since disruptions add costs and complexity to manufacturing and delivering products. This is where a streamlined operating model, that successfully leverages the enablement of technology and concepts such as concurrent planning, play a critical role in improving operations.
When you have technology platforms in place to analyze data in real-time and the proper operating model with empowered users and clear decision logic, you’re in the position to adjust quickly. Conversely, if you rely on manual efforts to review reams of data, it can take days to make necessary adjustments, which reduces options, generates waste and erodes margin.
For example, consider a CPG company. When the COVID-19 pandemic hit, consumer buying behavior changed and the demand for sanitizing products skyrocketed. Having a system in place that allowed a sanitizing products company to collaborate in real-time with suppliers alleviated potentially massive disruptions and protected the company’s margins while maintaining their commitment of social justice in the allocation process. The results were unprecedented, accommodating between 3,000-7,000% increase in demand with only a handful of empowered allocation control center network planners efficiently executing the process, compared to the prior manual operation that took weeks and over 80 employees.
3. Concentrate on parameter input quality using AI/ML rather than reliance on static values
One challenge that we see is when companies focus their planning on static data. While it’s true that changing transaction systems of record is difficult for the IT team, the reality is that these systems contain the foundation of planning decisions and timely reflection of reality is critical to planning decision and feasibility of execution. When there are changes and high degrees of volatility to your supply chain critical data, it’s necessary to leverage artificial intelligence (AI)/machine learning (ML) technologies.
Consider a furniture manufacturer that has a complex enterprise resource planning (ERP) system. The manufacturer had historically received a consistent volume of foam material to use in couch cushions and bedding products and that amount was delivered every 21 days. These historical realities were embodied in the ERP system and never changed. But during recent supply chain disruptions, the supplier can’t deliver the same amount of foam material every 21 days. The manufacturer needs to adjust the delivery from every 21 days to every 50 days, and the amount delivered is now cut by 30%. Do you look for another supplier? Do you stay with the operations in place and re-configure planning, ERP and customer ATP systems to reflect the new reality? Do you start leveraging pricing strategies to shape demand to avoid poor customer sentiment?
When there are changes in market conditions, companies should leverage AI/ML technology to change the key parameter inputs such as lead time, capacity, yield curves and others to improve quality of promise dates to customers in both B2B and B2C transactions. If your systems aren’t set up to adapt to these changes, you’ll continually run into the same problems based on ever-changing planning variables.
Increase agility to beat your competition
These strategies are designed to increase agility within your company’s complicated and ideally integrated ERP, transaction systems and supply chain tools landscape. Increasing collaboration with suppliers will be tremendously helpful as your company navigates the complexity surrounding supply chain delays. By examining and updating planning and execution models and leveraging AI/ML to enhance traditional static values, you’ll be able to identify and evaluate your options more thoroughly across a balanced scorecard that reflects business objectives in managing the inevitable changes to your supply chain network.