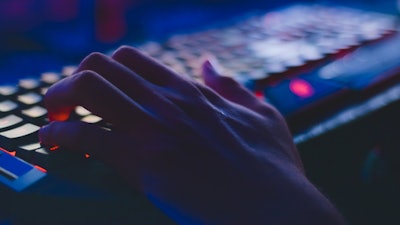
The global supply chain crisis shows no signs of easing with the continued aftermath of the pandemic. Disrupted supply chain operations are having a negative and protracted effect on product and resource availability. From the Suez Canal crisis, cargo ships sitting off the coast of California, the China Power Crunch and more, organizations continue to be affected by everything from production constraints to item availability.
Which all leads to the question, how do we build resilience into the future supply chain? Digital twins technology can be one new weapon. Through artificial intelligence (AI)/machine learning (ML)-powered simulations and parallel, real-time software agents or “watchers,” digital twins can help companies predict issues before they unravel and recommend solutions to address potential problems. By using a digital twin to represent operations, companies can interact with a digital or virtual model of their supply chain, simulating or capturing scenarios that show the best path to faster product delivery, improved efficiencies and minimized costs.
Understanding digital twins
A digital twin is a software-based virtual replica of a real-life entity or system that can take many forms, including representations of devices, people, and processes. Digital twin models capture and analyze data in a way that accurately depicts the physical world and allow organizations to simulate conditions, compare scenarios, explore what-ifs and mirror operations in real time.
In a digital supply chain, companies can deploy digital twins to analyze and understand supply chain behavior, track real-time events, predict potential problems and provide action plans based on data collected by the associated models. This functionality results in many benefits to the supply chain, including:
Cost-friendly production. Taking a product from the ideation stage to the showroom can be costly for businesses. Each product iteration involves several steps with plenty of opportunities for issues or delays in each one. Digital twins can reduce potential defects during these stages by allowing engineers to spot and adjust for flaws in a virtual environment before anything is implemented in the real world. It is much cheaper to "break" a simulated product or process, and engineers can test and run simulations early, allowing for corrections to be made before the physical product is produced and launched into the market. This approach, which can cut costs by 20-50%, allows for the virtual development and testing of complex products and processes, reducing the need to create expensive real-life prototypes.
Reduced time-to-market. The time required to design and manufacture a product before it’s market-ready can take upwards of 12 months to complete. With a digital twin, the entire product lifecycle can be simulated in a virtual environment, allowing companies to test and measure improvements efficiently and quickly, reducing the overall time needed to develop the product by 20%.
Predictive maintenance. Companies can use digital twins to anticipate equipment-related problems and recommend solutions before an issue unravels. The technology can continuously monitor its physical counterparts, gather real-time data through sensors, and analyze this data in real time, allowing human operators to use just-in-time methods for component replacement. By using analytics to predict equipment behavior, component lifetime can be extended, overall costs lowered, and maintenance becomes planned rather than unscheduled.
These capabilities are typically enabled by historical data that is used to train the associated digital twin models. Yes, the outcome of these models will only be as good as the data used to drive them, but the good news is that if done correctly, one can operate with a higher level of confidence as the processes/devices you are tweaking in your physical environment have already been battle-tested in your virtual or digital twin.
Applying digital twins
Digital twins do not just apply to simulations or historical analyses. A digital twin can be used as a real-time, track-and-trace "watcher" of an end-to-end supply chain system, allowing for the proactive identification and response to issues. These watchers are powered by tailored AI/ML models executed against combinations of historical, reference and real-time data sources. This creates an accurate real-time view of the end-to-end supply chain where each key step and process is tracked, and opportunities are identified for supply chain teams to make adjustments based on detected disruptions or events.
Given the bottlenecks, disruptions in production, and inventory delays currently evident in the global supply chain, digital twin “watchers” that operate in real-time are critical to reducing the stresses that these issues place on the system. Teams are armed with the contextual and timely insights needed to adapt to disruptions, meet regulatory requirements, and ensure compliance with third parties. The result? A supply chain that can weather any problem.
Digital twins and weathering the supply chain crisis
The current supply chain crisis has emphasized the need for business agility in the face of unprecedented circumstances. Adaptability is key, and while we can't predict a pandemic, we can build malleable supply chain processes that leverage real-time data, adaptive connectivity, and embedded analytics to reliably forecast future trends and shortages.
Using embedded AI/ML-based simulations, a digital twin model can alleviate complex challenges around efficiency, labor shortages and bottlenecks. When run in parallel to the physical supply chain, real-time digital twins anticipate potential issues by "watching" the slightest change in your data. When alerted to a potential problem, a team can turn to the digital twin to run simulated tests of possible "fixes" in a virtual environment without running the risk of breaking the physical system or process.
As business operations become predominately data-driven digital entities, digital twins simplify complex processes and operational functions with predictive analytics to support or automate decision-making. A next-generation digital supply chain leverages the inherent AI, machine learning and Internet of Things (IoT) capabilities of digital twins to draw insights from and make sense out of vast amounts of data.
In a crisis, companies can create a digital footprint of all assets and inventory, enabling them to analyze and predict possible challenges from implementation to production. Mirroring real-world applications helps organizations create new and improved operational processes cost-effectively through real insight, not just guesswork.
The digital supply chain of the future
A digital supply chain is better equipped to respond to unexpected changes in supply and demand, is agile and can adapt to a customer’s evolving needs in real time.
One kink in the supply chain armor and the whole process falls apart, which is what makes the digital twin option so attractive. Simulating and “watching” devices, processes and even people allows an organization to minimize downtime and enhance the ecosystem's performance with increased resiliency, optimized processes and responsive decision-making.
A digital twin may not predict the end of the global supply chain crisis, but it can help businesses better respond to it.