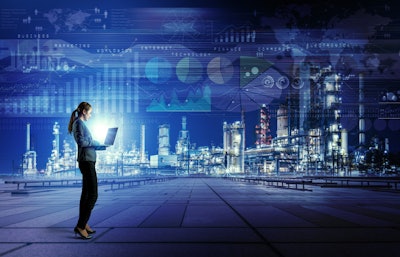
Pre-COVID-19 pandemic, a prevalent misconception within the industry was that companies can reach a “lights out manufacturing” state, whereby they can operate without any people at all.
Yet, the importance of manufacturing workers came to the fore over these past 18 months and now, even with more advanced technology coming onto the production line, it is often enabled by humans. The smart factory, a flexible system that augments human workforces by self-optimizing performance across a broader network, adapting to new conditions quickly, and aiding in running entire production processes, is the concept many manufacturers are now turning to for driving their manufacturing goals forward.
In a 2019 Deloitte and MAPI Smart Factory study, it was revealed that 86% of manufacturers believe smart factories will be the main driver of competition by 2025, and 83% believe smart factories will transform the way products are made. Manufacturers who use smart factories today sit in a market predicted to reach $244 billion by 2024 and are poised to reap the benefits of a fully connected and agile system.
Additionally, smart factories can help shift the long-term misperception of factories as outdated places of monotonous work to encourage the next generation into the workforce. In a recent Parsable study, 52% of recent Gen Z graduates, age 18-24, said they are disinterested or neutral about entering the manufacturing workforce; of those, 30% said they believe it to "be a low-skilled, manual job."
However, many manufacturers are still starting out. The process should really be thought of as a journey instead of a destination. For manufacturers looking to adopt smart factories, it is important to take the following into consideration when getting started on that journey.
1. Know your (realistic) entry points
Many companies are entering the smart factory world through a series of different onramps, so knowing where to start is the first thing to consider. Manufacturers shouldn’t always jump straight to the shiny technology and risk getting stuck in pilot purgatory. With 70% of digital transformation initiatives failing to reach their stated goals, companies should focus on starting small and scaling further down the line.
Leverage technology that's already widely available in the market. For example, turning paper-based work procedures into digital, interactive instructions on a mobile device that everyone already knows how to use can be a great way to get started because it’s a fast, achievable entry point.
Additionally, consider beginning with one asset on one production line, testing it out and seeing how it performs. Having a proven use case will act as a good accelerator for change in an organization because it gives stakeholders a reason to trust in what the smart factory can do for them and the business. According to a recent IFS digital change survey, half of companies cite aversion to change as the biggest barrier to successful digital transformation, so the ability to get teams invested in the smart factory journey is a necessary hurdle to overcome early on.
Manufacturing teams should also have a clear, grounded and agreed-upon definition of a smart factory before getting started, as definitions can vary. What are achievable goals, and how can you lock down and evangelize that vision for your smart factory? Whether that means starting with existing technology and building from there, it is all about finding the right entry point for your company.
2. Tie to environmental, social and governance (ESG) goals
ESG goals are embedded in today’s manufacturing environments, so organizations should look to smart factory technology that can help meet these goals. The convergence of smart manufacturing with the rise of ESG frameworks is supporting industry-wide sustainability efforts to create and protect value for companies and stakeholders, as today’s consumers, vendors and suppliers alike value companies that focus on these programs.
In cases where a smart factory can be developed as a greenfield project, there is an enormous opportunity to set comprehensive, site-specific ESG goals and bring in innovative solutions to achieve them. In other cases, smart factory initiatives can help manufacturers implement, track and measure existing corporate ESG goals. The adoption of typical technologies found in the smart factory environment - connected worker digital tools, artificial intelligence (AI), Internet of Things (IoT) devices and more - can all be used to connect the dots between corporate ESG initiatives and the work being performed on the actual production floor.
3. Use smart factories to bridge the skills gap and change perception
According to a Deloitte study, a U.S. manufacturing skills gap is predicted to leave as many as 2.1 million manufacturing jobs unfilled through 2030. Smart factories could hold some of the answers to this pressing issue. With companies operating on more skeleton crews, particularly as older workers make the decision not to come back following closures from the Coronavirus disease (COVID-19), smart factories can help bridge an immediate gap.
By nature, smart factories are dynamic and modern with their increased visibility, connectivity and adaptability. In today's manufacturing environment, humans and technology must work together to safely optimize performance and leverage the strengths each brings to the table. For example, many smart factories use connected worker and collaboration technologies that help manufacturers react efficiently and effectively to any need that arises on the production line.
Manufacturers choosing to use smart factories and the right digital tools can help the industry pivot and attract desired talent. Utilizing digital tools can improve work productivity, safety and sustainability. It also empowers workers further down in the organization to make decisions based on data and real-time visibility, making jobs at all levels more rewarding.
Changing the perception of manufacturing is necessary because contrary to popular belief, factories can’t run on robots alone. The reality is that humans and technology still work best alongside one another and will continue to do so for decades to come. Solving the skills gap requires people, not just robots. And, agile, next-generation smart factories are a perfect example of the manufacturing workplace that today’s workforce wants.
Conclusion
Smart factories are still an evolving solution with nearly endless possible configurations. It’s an exciting journey to embark on. Companies who make the choice to invest in smart factories, with their increased agility and connectedness, will enable workforces to function more effectively in their environments, help act on and meet their ESG goals and attract the next generation of talent.