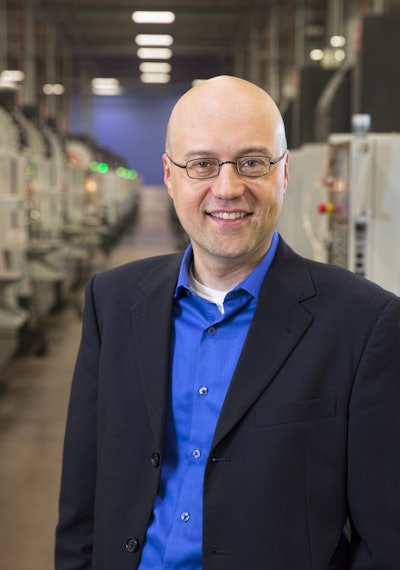
The Industry 4.0 revolution has been gaining momentum, given the increased understanding that technology systems and devices that make up the backbone of industrial processes can be digitally interconnected. This creates an industrial internet of things (IIoT) where smart devices and machines communicate and interact to make improvements to supply chains, operations and decision-making.
PwC estimates that about one-third of industrial companies have already digitalized their supply chains in support of Industry 4.0, and nearly three-quarters expect to go digital by 2020. Experts predict that digitalizing the supply chain can have staggering results. Changes such as predictive maintenance could eliminate up to 70 percent of manufacturing failures, and data-driven insights could increase productivity by up to 30 percent. This greatly reduces total cost of ownership (TCO) of production capital equipment.
More companies began evaluating their supply-chain performance in terms of TCO as the economy tightened and, more recently, as finance has gained greater influence over purchasing decisions and product development costs.
TCO also comes into play as companies decide how and where to source manufactured parts. Today, on-demand manufacturing is becoming the preferred way to source prototypes and low volumes of production parts.
On-demand manufacturing
On-demand manufacturing brings together the principles of just-in-time and lean manufacturing to streamline processes and reduce waste.
It creates the advantage of continuing to use the same supplier as product moves from prototyping into low-volume production. By consolidating suppliers, it reduces the cost and complexity of working with multiple vendors. An on-demand manufacturer with the scale and advanced automation needed to ramp up production quickly to meet delivery dates consistently will improve on-time performance.
On-demand manufacturing powered by digital manufacturing enables companies to purchase the exact quantity of parts when they need them. This means reduced inventory costs, and the ability to get parts quickly to avoid the risk of lost sales.
While the purchase price of a part from an on-demand supplier may look more expensive upfront, it’s important to consider the complete picture. Digital manufacturer mold costs are significantly lower than traditional injection molding service providers, making it a better value for production volumes up to 25,000 parts a year.
Even if you don’t have a digital supply-chain strategy in place, partnering with an on-demand manufacturing supplier can streamline production and simplify partner relationships by creating a digital thread from design through production. This thread enables the digital transfer of data through the process to speed up each step of the supply chain. It also allows companies to leverage a single supplier source as a part or product moves from prototyping into low-volume production. Companies with digital supply-chain capabilities – such as using digital 3D design tools – can achieve even greater benefits and lead to reduced TCO.
Industry outlook
According to the U.S. Commerce Department’s Manufacturing Extension Partnership, companies often underestimate costs by 20 percent. By using TCO as the baseline metric, companies get a more complete picture of costs, and a better measure of value or ROI.
Many industries – including medical, automotive and aerospace – are already taking advantage of on-demand manufacturing to reduce TCO. However, it’s important we continue to educate on its benefits, and the risks of failing to embrace it.