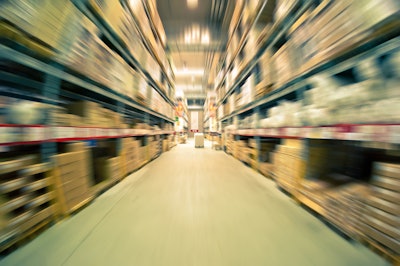
Our 2022 Top Supply Projects award’s mission is to celebrate projects the most transformative and successful cases from the past year. And, this is certainly true for the project featured in this interview.
The editors of Supply and Demand Chain Executive sit down with executives from Raymond to hear how to optimize a warehouse for maximum efficiency, and how it was able to help food insecurity reduction with Crossroads Community Services. The project was selected as one of SDCE's Top Supply Chain Projects of 2022.
Supply and Demand Chain Executive: Please describe the project.
Raymond: In 2019, Crossroads Community Services turned to Malin, a Raymond Solutions and Support Center, to learn best practices of receiving/shipping; to maximize efficient use of the additional warehouse space and inventory control. Crossroads Community Services had recently moved its operation, which aims to alleviate pockets of food insecurity in the southern sector of Dallas County as well as in Ellis and Navarro counties in Texas, from about 10,000 square feet to 72,000 square feet and needed help from Malin to ensure it was safely and fully utilizing all the benefits of such a fantastic new distribution facility.
Supply and Demand Chain Executive: What was the inspiration for this project?
Raymond: Fourteen months after Crossroads Community Services opened its new warehouse facility, the economic effects of the COVID-19 pandemic hit the Dallas area in March 2020. Just as Crossroads Community Services was starting to get comfortable in the new space, it faced a new challenge: unprecedented demand. In April 2020, the food pantry saw the number of daily visits double overnight. The food pantry, which was projected to distribute 900,000 pounds of food, was challenged with demand exceeding its expectations.
Supply and Demand Chain Executive: How did it make a difference for the company?
Raymond: Crossroads Community Services turned Malin to learn best practices of receiving/shipping; to maximize efficient use of the additional warehouse space and inventory control; and to safely and fully utilize all the benefits of such a fantastic new distribution facility. Raymond Lean Management (RLM) allowed Crossroads Community Services to identify and implement small enhancements and tweaks in its processes, which significantly impacted its production and efficiency. RLM added value to Crossroads Community Services by empowering employees to make improvements and take ownership of the tasks they accomplished daily. By teaching workers to spot inefficiencies or potential errors in their work, lean management provided them with practical tools to share their ideas and develop impactful, long-term solutions.
Supply and Demand Chain Executive: How does this project provide innovation during the supply chain crisis and disruptions seen this past year?
Raymond: When demand increased due to COVID-19, Crossroads Community Services used RLM teachings to continue identifying waste inside its warehouse. Through this process, the organization realized it was underutilizing its space. Malin helped Crossroads Community Services audit its current warehouse setup and identified areas for improvement. Then Malin was able to develop a new warehouse layout based on the turning radius of the warehouse fleet that included more areas for smart storage and increased racking inside its warehouse and cold-storage operations.
These continuous improvements extended beyond the warehouse floor for Crossroads Community Services. It helped identify waste and implement technology upgrades in other departments, including shipping/receiving, and in the pantry shopping experience.
Using RLM strategies and techniques to process, store and distribute nutritious food, the pantry distributed over 2,750,000 pounds, and the Crossroads Community Services network collectively distributed 11,800,000 pounds of food in 2020.
Supply and Demand Chain Executive: What makes this project different than others in the industry?
Raymond: The goal of Raymond Lean Management is different in that it doesn’t just help operators solve problems but also teaches them how to solve them on their own going forward. RLM is designed to instill a culture of continuous improvement throughout the organization to boost productivity and efficiency through visualization, standardized work, target-based key performance indicators (KPIs) and continuous improvement activities to provide the best possible solutions.
Supply and Demand Chain Executive: How did/does this project fit into the overall operations of the company?
Raymond: The RLM training course helped Crossroads Community Services identify areas of improvement to maximize its new warehouse space and enhance customers’ overall shopping experience.
The food pantry also optimized the client experience by using RLM principles to implement a one-way shopping lane, significantly improving the shopping experience. Clients in the pantry intake area work with volunteers to build customized shopping lists based on their families’ nutritional and caloric needs. When out on the pantry floor, the lists help organize the shopping experience and tell the shoppers exactly where their items are in the pantry, by aisle and shelf, so there is no need to backtrack or search for items.
Supply and Demand Chain Executive: What do you think the future holds for this project?
Raymond: Raymond and Malin are honored to have helped Crossroads Community Services improve its operation and ensure it could continue its mission to alleviate pockets of food insecurity in the southern sector of Dallas County as well as in Ellis and Navarro counties in Texas. Although Raymond and Malin’s involvement with the organization ended after they helped it optimize its new facility, Crossroads Community Services continues to improve its operations through a culture of continuous improvement using the RLM techniques and other optimizations Malin helped implement. Raymond and Malin are excited to see the success Crossroads Community Services has had in its new facility and hope their involvement helps the organization better serve the community.