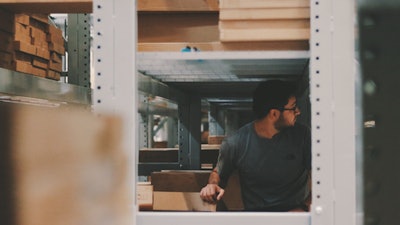
One of the simplest approaches to solving supply chain constraints is through the application of Lean principles. As manufacturers, distributors and retailers look to ramp up production, each of those key nodes within the supply chain should be aggressively looking to utilize all of their assets to ensure commerce continues to flow from their facilities to the retail outlets or via e-commerce channels, such as buy-online, pickup-in store (BOPIS) or drop-shipping.
Three common Lean tools that have proven to provide immediate visibility to process improvement and cost savings opportunities are:
· Cause and effect diagramming
· Spaghetti diagramming
· Value add vs. non-value add analysis
Cause and effect diagramming
Cause and effect diagrams, often referred to as Fishbone or Ishikawa diagrams, can be an effective tool in uncovering root causes of productivity barriers or process constraints. Productivity barriers are anything that prevents the process from being as productive as possible.
There are five steps to constructing and leveraging a cause and effect diagram. The first step is to identify the issue. This becomes the head of the fishbone skeleton.
The second step is to determine the major categories for the causes of each productivity barrier. Categories that are oftentimes used for classification include the 6Ms—manpower (personnel), machines, material, methods, measurements and Mother Nature (environment). These categories should be adapted to fit the desired scenario. The resulting categories become the main bones in the fishbone.
The third step is to brainstorm for potential causes of the productivity barrier. The potential causes become the smaller bones leading into the main bones. When trying to identify the causes, it is important to include resources at all levels of the operations team (directors, managers, supervisors, group leaders, experienced employees, etc.) in a brainstorming session.
Once the causes have been identified and documented, the fourth step is to ask, “Why is this cause occurring?” The answer to this question becomes an even smaller bone leading into the potential causes on the fishbone skeleton. It is highly probable that you may find multiple factors causing the productivity barrier to occur.
The fifth and final step is to eliminate any causes that do not apply, then identify and rank the most critical causes to eliminate in a logical order, such as savings opportunity or duration of time.
Spaghetti diagrams
Spaghetti (or workflow) diagrams depict the physical flow of work or material in a process and to improve the physical layout of a work area or an entire warehouse layout by identifying non-value-added travel.
By analyzing the diagram (see Figure 2) for crisscrossing lines and visits to the same locations or areas multiple times, this is an indicator of backtracking and ultimately non-value-added travel. Minimizing movement paths and the re-slotting items can significantly reduce travel distances as well. Mapping out the flow of work in a spaghetti diagram is a lot easier than trying to visualize that same flow of work and can lead to tremendous cost savings.
Value-add (VA) vs. non-value-add (NVA) process determinations
For something to be value added, three conditions must exist. They are:
· The customer must be willing to pay for the process step.
· The process must be performed correctly the first time.
· The process step must transform the product or service.
If the above three criteria are not met, then the step must be considered wasteful and should be eliminated. One simple way to document and quantify VA vs. NVA is through process mapping and time study analysis.
In process mapping and time study analysis, a table consisting of three columns—the process step, the time to complete and the classification (VA or NVA)—is created. As shown in Figure 3 below, the analysis of the example full pallet picking process results in 25% value-add and 75% non-value-add for this process.
Detailed analysis show that traveling to and from the location comprises 73% of the overall time and 93% of the NVA time. Potential improvement opportunities include re-slotting the pallet to a location closer to the shipping dock or cross docking the pallet at time of receipt.
Companies should always consider ways of employing Lean strategies in order to execute efficiently. By focusing on incremental improvements vs. an all-or-nothing, perfectionist approach, they will drive out inefficiencies with their operations, leading to bottom line cost savings, improved ability to execute, and competitive advantage.