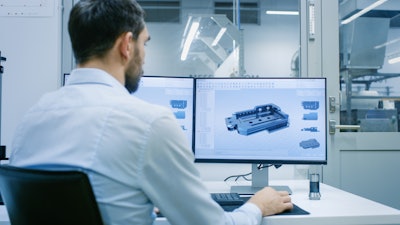
What is the most crucial factor in successful designs?
I know. This is a pretty abstract question. For engineering, this is probably as existential as you can get. However, it is one worth asking. Today’s schedules are getting tighter. Requirements are getting more complex. Budgets are shrinking. To meet the demands of modern product development, engineering needs to truly understand exactly what is on, and off, the critical path to designing great products. This one deserves some mind share.
One viable answer is process. Many companies deem their processes, identifying who does what when, as a core differentiator. And there is likely some truth in that statement. The execution of a process can materially affect the quality of design.
Another valid answer is people. Finding and training the right people for the right job is crucial. Without the correct skills, individuals will be woefully unequipped to design and engineer new products. Most executives recognize this reality and correspondingly invest in their people.
Yet another reasonable answer is information. Engineers need the right information at the right time to make good decisions. Without good accurate information, the wrong decisions result in poor designs that wreak havoc downstream.
One could argue that any one of these three factors are the most important to a successful design. Of these three, however, gaining access to the right information at the right time is likely the most underestimated factor. Let’s take a closer look at that.
The Need for the Right Information
Information is a key part of any decision an engineer makes. It all starts with requirements. They come in a wide variety of forms. There are customer requirements that the overall product must satisfy. Those are frequently broken down into smaller requirements addressed by different aspects of the design. There are formal processes to govern when and how such requirements are created and changed.
While new requirements play a key part in development, not all of them are newly created as part of the development process. There is a burgeoning number of regulatory requirements that vary from country to country. There are also industry standards that apply. All of this information might be locked away in requirements management, product lifecycle management (PLM), or application lifecycle management (ALM) systems. But the existing requirements are just as likely to be documented in PDF files, desktop spreadsheets, online databases and an array of other locations.
A different category of information necessary for good design includes a range of information on past designs. Engineers will often revisit past designs in order to develop new ones. When applicable, they can search documents that have been formally and digitally archived in enterprise systems like product lifecycle management (PLM) systems and enterprise resource planning (ERP). Yet, more information in the company is relevant. That includes results from prototyping and testing that might be a PDF. It covers older engineering artifacts such as scanned drawings and specifications.
Lastly, a critical source of information for good design is completely outside engineering. Modern design requires decisions that take broad considerations into account. Selecting a component might directly depend on if it is sourced by one supplier or more broadly available. It could depend on the current inventory level of a functional equivalent in the warehouse. The decision might be based on material composition. Yet more factors might include manufacturability, serviceability, quoting information and more.
Overall, engineers make some design decisions based on information that is not only accessible, but under their control. However, it is just as likely that key information exists in some form in another part of the company. In many circumstances, the engineer can’t make a decision until they have that information. This reality has spawned a host of approaches to getting the right information to the engineer at the right time.
Accessing the Right Information
One low-tech way of getting the right information to the engineer at the right time is the use of a “gofer.” This term refers to an entry-level role that essentially goes from place to place manually collecting things for someone. They “go for” this or “go for” that. This role originally involved tracking down information physically by talking to different stakeholders in different departments of a company. However, it has evolved into a modern-day version. That role now emails a variety of people in those different departments, collecting the information they need. If that information exists in an enterprise system, they are given credentials to login and retrieve it.
Beyond the manual effort involved, there are a number of flaws associated with this approach. The first problem is that some of the information is likely to change. The second problem is that there is no real-time notification of the change and update to the information. Together, those shortcomings make a deadly combination: decisions made from out-of-date information. Those using this approach try to minimize the amount of time that an engineer could have the wrong data in their hands. So they either increase the frequency at which the “gofer” role goes to get updates or they wait for the rate of change to that information to slow. None of this is an ideal approach.
Emerging technologies offer an alternative approach that addresses many of the shortcomings of the “gofer” approach. Companies such as IHS Markit offer solutions that ‘connect’ sources of information including enterprise systems like PLM, ERP, ALM and more. They index other sources of data like shared drives and desktops for documents, spreadsheets, and PDFs. Furthermore, they connect to online sources of knowledge that are outside of the organization’s firewall such as industry standards, codes, component databases, patent databases, eBooks, periodicals and more. Powerful search functionality allows engineers to stay connected to the live data as it changes in real-time. Ultimately, engineers have access to information, even as it changes, so there is a dramatically reduced chance that decisions are made based on out-of-date data.
Productivity-Based Justifications
So what is the value of providing the right information to engineers at the right time? Traditionally, the focus has been on productivity. A variety of research studies have shown that modern engineers spend a significant amount of time searching for the right information. That represents a productivity loss where the engineer is not adding value to the development process. Many view it as a time sink.
All that is true. However, that argument fails to convince executives to take action or sign purchase requisitions. Engineers are salaried employees that will work for some minimum amount of time per week. If they save some time here or there, the operational costs of the organization do not go down. They stay flat. But furthermore, if projects are behind, engineers don’t just stop working when they hit 40 hours for the week. They will often work nights and weekends to catch up. Justifications based on saving engineers’ time has, and always will, fall short to executives. It is simply too soft.
Yes, new approaches to get the right information to engineers at the right time will increase the organization’s productivity. However, that justification won’t get approval from executives.
Justifications with Hard Benefits
Instead, executives need hard benefits to approve changes. This typically will come in one of three forms: 1) the reduction of operational expenditures, 2) the reduction of capital expenditures or 3) increase in revenue. Each takes on a different form.
Operational expenditures, or OpEx, covers the ongoing expenses related to development and manufacturing products. Development OpEx includes funds for things like prototyping and testing. Interestingly enough, engineering executives are motivated to fully spend their development budgets. If they don’t, higher level executives think engineering can get by with smaller funding. So there is motivation to spend all of their budgets, but not go beyond that. In the context of justification, engineering executives’ ears perk up when they realize they can do more with the same budget. This doesn’t include frivolous extra rounds of prototyping and testing. But it might include more thorough correlation to simulation and analysis.
On the other hand, OpEx related to product costs is a real opportunity to improve profitability. With product prices or contract quotes often fixed well ahead of time, engineers control the ability to hit, or even undercut, cost targets for products. This is a dramatic win for the company as they can hold their original price and remove additional costs from the product.
Capital expenditures, or CapEx, covers the initial costs involved in ramping up the production of products, such as tooling. Reducing this cost directly affects the bottom line, improving the company’s profitability. Engineering executives often have no stake in the game when it comes to CapEx costs. Acting as the source of cost reduction is a win. In fact, costs reduced here can instead be used to acquire new software solutions.
Revenue growth is one of the most appealing means to justify change, but also one of the most difficult to prove. Improving in this area directly affects the profit equation. But it also comes with additional benefits. Engineering can deliver revenue growth by delivering impactful, innovative and high differentiated features. However, validating such a causal relationship is difficult.
Decision-Based Justifications
Productivity infrequently is the basis of a justification. Yet, cost control and revenue growth act as powerful ones. How can getting the right information to engineers at the right time affect costs or revenue?
Decisions.
Obviously, any engineer’s responsibility is to save their employer money and increase their revenues. Their ability to do that, however, is directly related to the accuracy and freshness of the information at hand.
An engineer with real-time access to inventory and procurement categorization might find a functionally equivalent in-stock part for their design that saves the company a significant amount of money.
An engineer with an instant connection to a recently updated standard or federal regulation might catch a new documentation requirement that allows the company to avoid a fine during an audit.
An engineer with real-time access to a research company that publishes their findings online uncovers a newly released plastic, allowing them to avoid the use of a casted component that reduces cost-of-goods by half.
What’s the Value of the Right Information to You?
Getting the right information to engineers at the right time is a critical factor to successful designs. The question most organizations face is this: how do you enable that? Especially when there are so many relevant sources of information.
For years, many employed a “gofer” to manually collect information for engineers. However, that information was often outdated quickly. A new class of technology, included in IHS Markit’s Engineering Workbench and Goldfire, offers a means to connect engineers to a wide variety of information sources in real-time, addressing the shortcomings of the “gofer” approach.
As many companies mull a change to this approach, the question becomes how to realize value from such solutions. Improving engineering productivity is appealing, but lacks the hard benefits most executives need. Decision-based justifications offer the means to reduce costs and improve revenues. This justification has many opportunities, but will often be company specific.