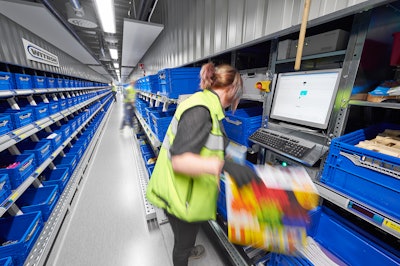
There are myriad warehouse automation solutions on the market today. There are also several levels of automation—from semi-automated to fully automated and everything in between. The important question, then, is what kind of automation system to select based on the goals you are trying to achieve.
“There’s no one size fits all in warehousing; everything has to be thought about in the context of what problem you’re trying to solve. It really depends on how big the facility is, how you want to balance operating expense against capital expense, what your buy-ins are and how big a company you are,” according to Bruce Welty, co-founder of Locus Robotics.
Goods to Person, and Automated Storage and Retrieval Systems
More warehouses and distribution centers (DCs) are seeking goods-to-person (GTP) technologies when considering automation. The GTP concept is simple. Instead of workers traveling to the items to be picked, the items are brought to the worker. According to Nathan Busch, associate consulting engineer at Bastian Solutions Inc., “The throughput rates of GTP systems are typically quite a bit higher than traditional manual operations. This allows companies to reduce their overall operating and order fulfillment costs, while improving throughputs and service levels.”
There are a few different types of GTP systems. Busch elaborates, “At the highest level, automated storage and retrieval systems (ASRS) are examples of GTP technologies because rail-guided cranes traverse storage aisles and levels to store and retrieve materials from pick-up and drop-off points. These pick-up and drop-off points interface with other material-handling equipment that eventually bring the materials to the point of use.”
There are also shuttle-based systems, which are ultra-capacitor or battery powered, in the GTP mix. Shuttles traverse each level of each aisle, and each level has at least one shuttle to handle loads. Busch continues, “Another even more modern shuttle system is one that utilizes lifts at the ends of the storage aisles. The shuttles still traverse the length of the storage aisles, but this type of system allows for the shuttles to travel to other levels within a given aisle. This creates flexibility by allowing access to all inventory within a given aisle, as well as flexibility when determining investment costs for throughput versus the quantity of shuttles required.”
Pick-to-Light Systems
Pick-to-light warehouse automation uses lights above racks or bins to direct pickers where to pick. The user simply scans a barcode on a picking container. Then a light above the rack or bin illuminates with the picking quantity, and the user picks the items for the order, corroborating the pick by pressing the light.
Adam Kline, director of product management at Manhattan Associates, thinks, “Put to light tends to be a nice way to increase overall fulfillment capacity, especially in an e-commerce environment, and when coupled with batch or multi-order picking to be able to meet peak season demand. I think that a lot of the automation trends that we’re seeing are due to that peak and seasonal demand. Ratcheting up your fulfillment capacity to be able to meet six, seven times, and sometimes, all the way up to 20 times average demand during the peak season is crucial.”
Mobile App Picking
When it comes to picking, Kline sees a lot of potential growth in equipping end users with a more modern, mobile experience. Rather than having DC workers wield a large, difficult-to-use RF scanner, he envisions them using a smartphone or tablet equipped with a mobile app for picking. The app elucidates instructions so that it’s easy to walk the user through his or her job functions. The app that Manhattan Associates produces even “offers a view of the item that’s expected to be picked so that temporary workers [who may not be familiar with the inventory] can ensure they’re picking the right item.”
Mobile Autonomous Robots
Locus Robotics offers mobile autonomous robots that can go anywhere in the warehouse. The robots travel to an inventory location. Then a light on the robot illuminates to indicate that a worker patrolling the zone needs to pick an item from the indicated location in a specific quantity. The warehouse worker picks the item, then scans it with the robot’s scanner, and drops the item in the bin. The robot then travels to the next spot for the next pick.
Welty says, “The workers monitor their zones, looking for the robots’ signals and respond to the requests. The collaboration between robot and worker dramatically improves efficiency. The associate completes the pick faster and is thereby able to complete more pick requests. With our robots, workers are able to pick faster and more productively than with traditional manual picking.”
Warehouse Automation Benefits
“Warehouse automation solutions help optimize operations and efficiencies by performing redundant tasks that are typically performed by operators in a manual operation,” Busch says. “Automation helps by removing waste from an operator’s typical work, which may include waiting, travel time and motion. When implemented correctly, automation allows operators to focus on the tasks that require human intervention and leaves the other tasks to the equipment. Typical ASRS and GTP systems have higher throughputs than traditional or manual operations because of the waste that is removed, reducing operating and order fulfillment costs, while increasing throughput capacities.”
When compared to a manual warehouse in which workers operate off of paper instructions, yet must log their productivity in a system to keep track of inventory movement, Kline says, “The leap from a manual process to a warehouse management system in which everything is typically driven based off of barcode scans, real time or voice-enabled flows is massive—especially from a productivity perspective. Because the system is constantly feeding you the next bit of work, you never have to go back to your supervisor to get your next pick list, for example. You’re not wasting that travel time. It’s generally increasing the speed at which you can fulfill orders, which ultimately makes for happier customers.”
Another advantage of implementing warehouse automation is that it reduces a warehouse’s dependency on labor, especially in the face of the ever-increasing talent shortage. Another factor is that many young workers have a disillusioned view of the warehouse as being a generally unattractive place to work. Automation may help reverse this trend because, the more automation a warehouse employs, the more employees are needed to operate and maintain the equipment as opposed to suffering through the repetitive bending and lifting in a traditional manual warehouse. Additionally, Norman Leonhardt, director of business development at Witron, notes that, in some countries, “regulations are very strict, limiting, for instance, the amount of weight that each worker can lift every day. In the end, automation actually seems like an easier solution because regulations are pushing toward automation.”