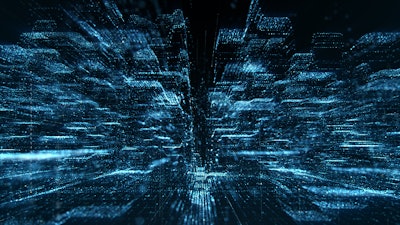
Supply chain leaders are turning to new technology to safeguard themselves from disruptions. Businesses now understand that it is no longer a question of whether to digitize – it is now a question of how much, and how soon.
At the forefront of this new digitally enabled strategy is simulation – a powerful validation, visibility and communication tool for businesses looking to assess automation feasibility, improve network design and optimize distribution centers.
Using simulation, businesses can model hypothetical scenarios without having to physically change the asset. Whether a business problem lies in warehouse layout, inventory management, equipment monitoring, network design or process optimization, simulation is a problem-solving tool transforming global supply chains. With simulation companies can visualize, validate and test designs for DCs, automation and supply chain optimization prior to implementation.
At the core of logistics, is the principle that the longer a product takes from supplier to consumer, the more touchpoints it goes through, resulting in a higher cost. Simulation is helping to understand and navigate this flow, identifying which processes are running sub-optimally and validate improvements.
The applications for simulation are wide reaching, from optimizing routes in the last mile, to automation systems in a DC, to reducing the order cycle time.
Simulation Starts with the Problem, Not the Solution
A clearly defined problem is a problem half solved – this old adage rings true with supply chains. First principles thinking is one of the most effective strategies for breaking down complicated problems and generating original solutions. With an abundance of data in modern operations, it’s important to firstly identify the areas of impact that make a difference, which is why beginning with the problem, not the solution, is crucial to lay the foundation for analysis and simulation.
Simulation isn’t an off the shelf solution and its value is unlocked by the user, who develops the model before interpreting its outputs. Like most advanced technology, subject matter experts who understand the warehouse flow are required to contextualize and interpret the outputs and scenarios to clients.
The reality is, simulation is becoming increasingly popular, but a skills gap hampers its implementation and effectiveness. To create a digital replication of a system, you need to understand how to build a physical system, and the technology experts need to understand the problems associated with the logistics world. For the best results, a cross-functional team of both industry and simulation experts work together to translate the highly complex real-world system into a digital twin.
Validating Complex Decisions
Great companies share the ability to make informed decisions based on the measures that matter. By making strong decisions based on the most relevant data, businesses can be ahead of the curve and create a culture of innovation and accountability. However, the opposite approach can have negative impacts on the supply chain – poorly led companies overanalyze and delay, continually pushing themselves into a tight corner.
Simulation is not only powerful when running “What If?” scenarios, but an excellent communication vessel to ensure alignment from the factory floor to the boardroom. The difference between looking at changes through a 2D, CAD design lens and an industrial simulation can supply the confidence needed to make a significant business decision which transforms a company’s operating efficiency.
Simulation can also prevent companies from overinvesting. Recent reports of major retailers in the UK being forced into mothballing their own distribution centers because of inventory mismanagement demonstrates how simulation could illuminate future scenarios and best inform leaders prior to major investment. By simulating different solutions, companies can better understand their automation feasibility, network design and ways to optimize their distribution center.
For supply chain leaders, it’s important to add another layer to understand, when will it not work? What factors have a large impact on the solution performance and how can we ensure we cater for this? Simulation fits this mentality, helping companies look to the future and prepare themselves for today’s fast-changing business environments.