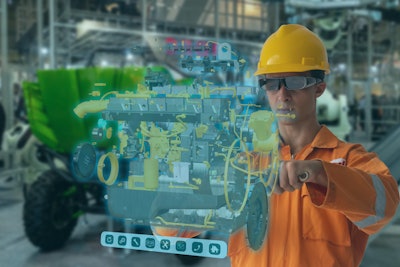
The use of digital twins—a virtual representation of a physical object, machine, or system—is exploding. Barbara Humpton, President and CEO of Siemens, aptly said digital twins may “lack the name recognition of technologies like artificial intelligence, virtual reality, or 3D printing, yet it surely ranks among the most remarkable industrial technologies to emerge.”
Digital twins are interactive simulations that leverage real-time information flows. The technology has the potential to broadly impact how businesses operate in an increasingly digital world, helping with everything from city planning and urban decarbonization to retail. But even as leaders across industries begin embracing this technology, the widespread application of digital twins to optimize supply chain operations could have the greatest impact of all.
Supply chain managers can start to unlock the power of digital twin technology by being specific and selective in its deployment. Don’t try to boil the ocean; building a digital twin for your entire supply chain is a good goal, but a momentous task. Data is only valuable if insights and action can be derived from it. By initially deploying digital twins for purposes more targeted than wholesale supply chain improvement, procurement professionals will see more immediate returns on their investment.
Here are a few goals to consider targeting first.
Optimize product design for supply chain constraints
Amid continuing global disruption, supply chain constraints are causing part delays and shortages without an end in sight. Running model comparisons in digital twin environments can help manufacturers identify alternate parts and optimum product configurations so they can get to market faster than otherwise possible.
Fortunately, manufacturers don’t have to wait for problems to arise before deploying digital twins. The benefits of this technology are applicable to the entire product lifecycle, but manufacturers too often make the mistake of waiting to think about optimizing their processes until after it's already been built.
Starting in the virtual world first during the design phase affords logistics and supply chain managers far more flexibility. It’s much simpler and more cost effective to test how two different parts work together in a digital environment—like Piston 1 versus Piston 2 in an engine—than it is to manufacture two different engines with two different sets of pistons.
If the parts work essentially the same in the digital twin, manufacturers can opt to choose the one that is best to procure—whether that’s defined by the part’s availability, cost, environmental footprint, or any other metric—before moving on to the manufacturing stage.
Digital twin technology provides incredible value at the front end, enabling optimization for design and procurement before manufacturing even begins. Unfortunately, manufacturers often miss these opportunities by deploying digital twins too late in the product lifecycle.
Reduce Scope 3 emissions
Sustainability is an imperative consideration for manufacturers, and Scope 3 emission reduction is often the greatest challenge faced by supply chain and procurement professionals on this front. The EPA describes Scope 3 emissions as “the result of activities from assets not owned or controlled by the reporting organization, but that the organization indirectly impacts in its value chain.” For many companies, these emissions represent the majority of their carbon footprint—oftentimes as much as 65% to 95%. This means that to meaningfully affect the overall sustainability of their organization, supply chain leaders need to reduce emissions resulting from things beyond their direct control.
Digital twins can help manufacturers source more sustainable parts and products based on a variety of criteria. By running comparisons to assess the functional equivalency of two potential alternate parts—like in the earlier example comparing Piston 1 and Piston 2—manufacturers can determine where they have the flexibility to optimize sourcing and supply chains based on a variety of environmental factors.
If the simulated engines perform the same regardless of piston choice, manufacturers can pick the piston made from a more sustainable material or built by a supplier that has a carbon offset program. They could also avoid ocean or air freight emissions altogether by sourcing instead from a domestic manufacturer. It’s even possible that leveraging industrial-grade 3D printing technology to manufacture the piston onsite might ultimately be the most sustainable option.
Digital twins make it simple and cost-effective for manufacturers to assess the viability of alternative parts with varying environmental impacts, giving you the knowledge and power you need to meaningfully reduce Scope 3 emissions for your organization.
“What if?” bottlenecks
The COVID-19 pandemic and supply chain disruptions that followed reminded suppliers, consumers, and everyone in between about the importance of anticipating potential problems before they become global crises. Supply chain professionals can use digital twins to both navigate current disruptions and predict where they may face problems in the future—enabling manufacturers to stress-test and enhance the resiliency of their supply chains.
By tracking metrics like packaging performance and distribution routes, digital twins can help streamline supply chains to minimize the likelihood of bottlenecks before they occur. Furthermore, it is far more expedient and cost-effective for manufacturers to analyze the impact of potential changes to their distribution routes in a digital environment based on historical data than it is to experimentally alter their routes in the real world.
As COVID-19 has demonstrated, there will always be unpredictable events. But with the right data and infrastructure in place, manufacturers can proactively plan for many of the most common and destructive disruptions.
How to stay ahead of the pack
Like other emerging and impactful technologies, manufacturers that don’t deploy digital twins to improve their supply chain and logistics operations will be left in the wake of those that do. Before getting started, however, supply chain leaders must be clear about the basics of what’s needed for success
- Start with defining goals: Examine your logistics operation to identify inefficiencies and pain points that can be addressed with digital twins, including the people, procedures, information, and assets related to those components. Then, align your goals with the data needed from the digital twin.
- Understand hardware necessities: Digital twins for supply chains and logistics operations can benefit from integrating IoT devices to collect real-time information from physical machinery or worker movements. Your sensor deployment should be planned in advance to align with your goal—whether that is collecting data about an asset itself, its environment, or both.
- Don’t underestimate software requirements: Software providers play an outsize role in the success of digital twin initiatives. Make sure your solution is capable of capturing all the pertinent data from your real-world environment. In parallel, build or otherwise deploy a data lake to aggregate the wealth of data from all your databases and systems related to the digital twin.
It’s not too late—starting with a targeted approach will enable your digital twins to provide actionable value and net immediate benefits for your organization. The great thing about digital twins is that once you have them, it’s quite easy to grow their utilization throughout additional departments. Eventually, you’ll be able to represent the entirety of your supply chain and procurement operations in a digital environment, reaping rewards that will put you ahead of the competition.