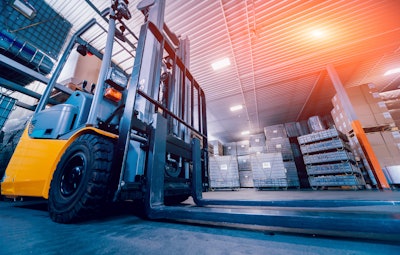
Despite a more than 60% decrease in worker deaths and injuries since the 1970s, according to OSHA, more than 5,000 people still die at work every year and another 3.6 million people suffer a severe work-related injury. Following the COVID pandemic, organizations have become increasingly aware of the critical role they play in ensuring the health and safety of their employees. It’s not only their responsibility to protect workers from illnesses and accidents, but it’s vital to the success of their organization if they want to retain employees and avoid the rising cost of safety failures. This is especially relevant as the demand for warehouse workers is on the rise. According to a recent study, 61% of warehouse operators worldwide are seeking to increase their employee headcount in 2023 and yet 55% say finding and 44% say training workers remain big challenges.
Technology has emerged as one such way to help improve workplace safety and encourage worker retention by changing how employees are trained in hazardous roles, how job sites, systems and tools are monitored, and how overall warehouse health and safety is protected. New inventions including advanced PPE, wearable sensors and other IoT solutions provide valuable data that organizations can use to improve efficiency and safety. Virtual reality, for instance, can offer an alternative to risky on-the-job training, making onboarding and upskilling safer. Artificial intelligence (AI) combined with video can help monitor PPE usage and compliance or risky machinery use. And wearables can alert employees to high-risk postures and detrimental work habits. By harnessing this data output, companies can identify risk areas and proactively address safety failures before they become an issue.
Collectively, these advancements not only improve the effectiveness of safety programs and reduce risk across the industrial industry, but they can also improve employee awareness of how much employers are doing to ensure the safety of them and their teams, a critical part of building a robust safety culture.
Let’s take a closer look at how three specific technology innovations can bring a new level of risk mitigation to the warehouse in 2023.
1.Virtual reality for off-the-job training
Forklifts are one of the most used pieces of equipment in warehouses, but they are also dangerous to both personnel and property if not used correctly. OSHA regulations specify that each individual employee must be trained to operate a forklift before ever turning the key. And yet there are many forklift manufacturers, and the models often vary widely, further complicating the ability to run these machines safely. Effective training to help ensure smooth and safe operations of these powerful machines becomes increasingly critical as businesses seek to fill the labor gap with new hires that are also new to warehouse operations. It’s risky to put these novices behind the wheel who may assume driving a forklift is just like operating the car they arrived in to work (spoiler alert: it’s not!). Virtual reality (VR) can provide the training foundation needed to drive these critical pieces of equipment and do so safely. In addition to traditional classroom training and certification, VR training offers a safe, interactive way to prepare for forklift operations before ever testing it out in the warehouse. By providing an extra layer of training and practice, organizations can mitigate further risks by limiting exposure to potentially hazardous situations.
2.Wearables for individual employee health and safety reporting
The Bureau of Labor Statistics finds that ergonomics injuries comprise more than 30% of workers’ compensation claims, equaling nearly $10 million. For example, warehouse workers commonly suffer strain and sprain injuries. Such injuries can sideline employees for an extended time and potentially impact operations – especially if skilled labor is difficult to come by.
Wearable sensors can alert workers to improper handling techniques and prevent injuries from happening in the first place. For example, sensors the size of a key fob can be placed on the back or a shirt collar of an employee and buzz or beep whenever a move is made that increases the likelihood of a lower back strain. The feedback loop is immediate and new behaviors and postures are established quickly, reducing potential sprain risks.
This technology is already well proven in warehouse environments and can be done cost effectively. Many wearables can be rented and used on a subscription basis ensuring any initial investment is minimal.
3.Coupling cameras with artificial intelligence
You likely have cameras and video capabilities in your warehouse already but turning them into “smart” devices capable of identifying and preventing safety issues is where your organization can truly benefit. By adding AI capabilities into the mix, businesses can help to ensure hazards and safety concerns in the warehouse are being proactively addressed. For instance, without requiring facial recognition technology for privacy concerns, AI-driven programs can monitor PPE compliance, detect spills before a slip occurs and monitor forklift use – including speed. Even if your organization has an injury rate below the national average, there is likely more that can be done to further reduce risks in your warehouse and keep your valued workforce safer. Given AI’s foundation of data, the technology also enables executives to dig deeper and garner insights into current safety practices that may need remediation.
Which technology is right for you
Not every innovation may be right for your warehouse right now. Some of these technologies are better suited to address some issues rather than others; it’s not a one-size-fits-all scenario. Before seeking capital to implement technology, take the time to identify the top hazards in the warehouse. Review the injury log and identify where the majority of issues occur. Perhaps most of the concerns are centered on proper ergonomics; if so, evaluating wearable technology may be prudent. Consider a pilot and establish clear goals that are customized to your specific warehouse’s needs. Also, it’s worth underscoring that technology alone cannot solve your safety problems. Getting workers involved in the process early and feeling like valued partners in the process is critical to developing a culture of safety. By fostering a “find and fix” mentality among employees, companies can elevate hazard awareness and encourage everyone to raise concerns over identified risks. This not only gives the organization an opportunity to swiftly correct an issue, but to track company-specific safety challenges that may be best mitigated with advanced technologies.
According to recent findings by the National Council on Compensation Insurance, the average cost of a workers’ compensation claim was $40,000 plus insurance premiums, lost productivity and more. Implementing a comprehensive health and safety program, underpinned by technology, can help reduce these expenses and deliver safety improvements by often avoiding potential injuries and illnesses altogether. And it's not just the technologies themselves that can move the needle, but rather the ability to capture key safety data and uncover patterns allowing organizations to take immediate corrective action. By leaning on these innovations as way to both demonstrate a commitment to safety and provide practical solutions, organizations can take a proactive approach to warehouse safety to not only benefit their employee’s health and wellbeing, but also the business in 2023 and beyond.