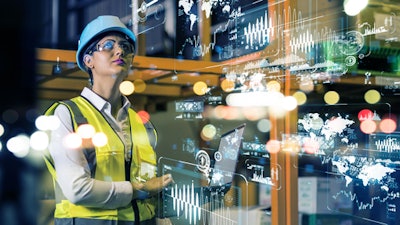
For decades, supply chains were engineered to be the equivalent of Swiss watches, where inventory and capacity were optimized for ideal conditions. Bonuses and accolades were bestowed upon executives who could create the leanest operation. Perfection was planned in every supply chain and low-cost labor and logistics were linchpins. Organizations trusted that supply chains would work and discounted significant risks as they blindly focused on the lowest price. The automotive industry may be the finest example of focused lean manufacturing adoption. And now, according to Seraph calculations based on multiple data sources, it is facing a combined revenue loss of $850 billion due to semiconductor shortages alone.
It started in 2020. Low-cost countries fell into disarray as the pandemic took hold and many still have yet to recover. With the stops and starts across regions, it has become increasingly challenging to refill supply pipelines. Shipping containers from China now cost more than $20,000 and delays are rampant as ship, port and trucking constraints impact the supply chain. Automobiles, paper towels and even children’s toys are in short supply. Shelves are often out of stock, highlighting the stark realities of the broken supply chain strategies companies have been using. As fall and winter settle in, look for an increased prevalence of more production stops and supply shortages.
We all should have known better. No room for error existed even as “black swan” events became common and expected. Supply chains need to be re-engineered across all industries to make them more resilient and enable companies to survive.
Even with the heroic effort being made by many companies, supply chain disruptions will continue throughout 2023 and likely far beyond. There are actions that companies can take now to re-gain control of their supply chains and mitigate the impact in the future. Reimagining and then re-engineering the entire supply chain will take massive capital investment, political will and a sense of urgency.
Here are five immediate actions that supply chain teams should take to enable their organizations to survive:
- Engage the management team and board of directors. Supply chains have never been a board-level issue, but the Coronavirus disease (COVID-19) has the potential to make supply chain failures business killers. As supply chain professionals, it is your obligation to make sure that the risk associated with supply disruptions is understood by your board and management team. All companies that have real products need to have a board sub-committee focused on supply chain to engage the government, look at the capital investment that may be required and remove roadblocks to take rapid action outside of normal budget cycles.
- Conduct an immediate, honest and quantified “tactical” risk assessment of your supply chain with board oversight. In the past, sourcing was done to find the lowest cost or the lowest landed cost. Risks have rarely been considered in sourcing models; there was simply an assumption that material would always arrive in the quantity and quality that was required. Suppliers were expected to manage their Tier “N,” but organizations were not structured to do this and that has put most companies into a reactionary mode when product is not going to arrive. Those who have been most successful have found supply chain monitoring tools that enable transparency and serve as an early warning system.
- Understand how your systems handle backlog through EDI, remove the noise from the system and communicate directly with suppliers. Enterprise resource planning (ERP) systems are designed to work in a perfect world. Occasional exceptions can be highlighted and managed by a small team, but the backlog is extreme and supply chain professionals are unavailable to intervene. These ERP systems that enabled “lean operations” are beginning to kill manufacturing operations. There is an immediate need for all companies to go through their ERP system, purge the massive backlogs that likely exist and prioritize electronic data interchange (EDI) releases, so that the parts needed for immediate production are clear and suppliers can forecast true demand out to their supply base. Beyond the system work, supply chain teams must staff up as calling and talking to suppliers is essential. Those teams that build good relationships will have the best performance from their supply chain moving forward.
- Make plans to regionalize all components that can be moved. Lowest cost has proven to be highest risk and organizations need to accept that inflation is here. Moving component supply back into the region where production takes place or product is consumed is becoming a strategic imperative. Models show that we will be dealing with significant supply chain disruption through the end of 2023 and likely far beyond. Engaging the board with quantifiable data, including risk adjustments, will enable a competitive advantage when supply chains are regionalized. This is not a fast or inexpensive step, but is one that all organizations have an obligation to study and act on where feasible.
- Secure space to hold inventory and develop a risk driven inventory model. Allocating capital and holding inventory is no longer a bad thing; it is now essential. Making a calculation to continue supply of critical materials needs to be done immediately. Warehousing material, minimizing engineering changes and understanding supply chain fragility will be important to keep the shop floor running. Warehouse space is already in short supply, so finding and securing unconventional space such as abandoned retail stores will be essential in many areas. Moving quickly here with clear risk-driven inventory levels will cushion the stops and starts that will continue to cascade through regions over time. Simply because a region is open now does not mean it will be in three months’ time. Understanding the shipping and production impacts of COVID-19 on the regions where your suppliers exist should support your inventory planning and warehouse-based requirements. Inventory is no longer a four-letter word; it is one of the key factors that will enable your organization to survive the COVID-19 business cycle.
There are many other strategic actions that can be taken to protect your supply chain. Getting these basics in place and engaging the broader organization should be top priority in the coming weeks and months. The current stop/start cycle of COVID-19 is going to last far longer than most want to admit. Plan on this being the catalyst to drive a complete reengineering of your supply chain, but start with some basic tactical actions to enable your company to survive in the interim.
Click here to hear more about resiliency in the supply chain: