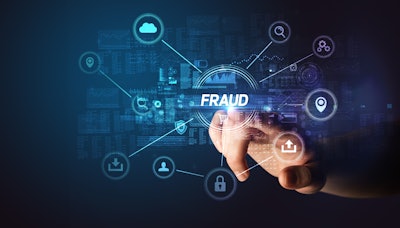
The Coronavirus disease (COVID-19) pandemic has pushed global supply chains to the limit, with tremendous implications for international trade. Businesses that have experienced a sudden surge in demand have been forced to quickly restructure their supply chain network and onboard new third parties into their production process - all remotely. This has opened the door to a flood of new risks, including potential regulatory exposure and severe reputational damage.
Previous crises have highlighted the need for smart and agile logistics operations: the ability to move assets between carriers, modify routes, and change capacity with ease, in order to respond to unexpected events efficiently and effectively. However, the disruption caused by COVID-19 has crippled logistics operations, with suppliers unable to meet soaring demand. Analysis of Factiva, Dow Jones’s global news database, revealed that reports of supply chain disruption in trusted news sources increased by almost 2000% between January and March of this year. Even now, reports are nearly five times higher than the previous year, as the disruptions continue.
The pandemic has also heightened international trade tensions, with new sanctions and regulations creating further complications for risk and compliance professionals. The U.S., for example, recently introduced new laws to combat the export of goods to military end users in certain markets.
To safeguard the integrity of their supply chains during the pandemic and navigate the increasingly complex regulatory landscape, organizations must take the necessary precautions:
Ask the right questions
In order to safeguard against shortages and maintain business continuity, many organizations have been forced to diversify their supply network - onboarding new suppliers at a record rate and volume. In such haste, businesses are more likely to be susceptible to cutting corners, increasing potential risks such as bribery, corruption and modern-day slavery in areas where they would normally have stringent checks in place. Conducting the compliance vetting process remotely introduces new challenges. With restrictions on physical visits and checks, businesses may be solely reliant on the assurances of suppliers to maintain the integrity of their supply chain, leaving them exposed to new risks. The best third-party risk management programs have introduced more robust questioning and checks, such as requesting to see new suppliers’ business continuity and infectious disease management plans, as well as local safety certifications.
Double down on data
As the impact of the Coronavirus continues to be felt, it has never been more important for business leaders to keep up with changing international policies relating to trade restrictions, border controls, and labor laws. And for that you need access to quality, reliable, and accurate data. With significant economic implications set to linger for months to come, we can expect to see ongoing supply constraints, reduced operational capacities as social distancing is enforced, and, in time, new regulations to help ensure businesses are better prepared to respond to disruption during future crises. The organizations that appear to be weathering the COVID-19 storm are those that have committed to enterprise-wide risk visibility, insight and collaboration. This has always, and should remain, a top priority for all risk and compliance professionals.
Scrutinize ownership structure
With the introduction of new export regulations, organizations now have to be hyper-aware of their international transactions. In the United States, the Bureau of Industry and Security has recently amended Export Administration Regulations to expand license requirements for exports of items intended for military end use or military end users in China, Russia and Venezuela. The new rules broaden the definition of “military end use” to cover not only the national armed services but also the national guard, national police, government intelligence and “any person or entity whose actions or functions are intended to support” military end uses. For many companies in the United States and elsewhere, this expansion will require increased due diligence to identify whether customers in these markets are considered military end users, or have other associations with the military, including through many layers of ownership.
While frictions between these countries have been long documented, the Coronavirus appears to have exacerbated tensions. And, as new sanctions and regulations come into play, it has never been more crucial for organizations to keep a close eye on their customers’ ownership structures to ensure they remain compliant.
Prepare and pre-empt
The speed and severity of this pandemic caught many off guard. It has also highlighted a lack of digital literacy in the risk management space. With teams stretched to their limits, and many still working remotely, there is a huge opportunity for compliance teams to transform. Leading supply chain organizations use a range of automated or digitized risk management platforms that incorporate intelligent decision-making frameworks, which can accommodate exceptions and regional nuances in ways that still enable continuous, consistent management of the most common and prominent risk factors.
The Coronavirus is undoubtedly increasing the rate and volume of our work as risk and compliance professionals. And, while working patterns and business landscapes have changed, it is clear regulators haven’t pressed pause. One only needs to witness the record-breaking fine recently levied by U.K. authorities on Standard Chartered for violating Russia sanctions.
Between the pandemic and the new U.S. trade tensions, it is evident just how increasingly complex risk management within the global supply chain can be. Although “Black Swan” events such as the Coronavirus are unpredictable in their very nature, the supply chain of the future must be reconfigured to ensure it can be agile for sudden changes. To mitigate risk in this volatile environment, it has never been more important for businesses to have the data, tools and processes in place to respond appropriately, and proactively.