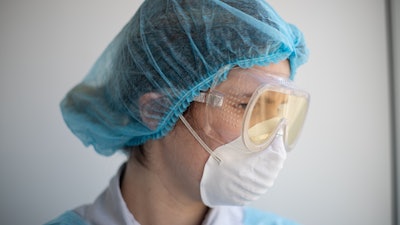
The beginning of the year began with increasing international complexities and shipping capacity concerns for many enterprise-caliber organizations. Then the Coronavirus disease (COVID-19) hit at the end of Q1 and the ensuing global health pandemic quickly overshadowed those initial concerns. Since then, manufacturing, distribution and transportation companies have focused on maintaining business operations while processing a new challenge of ensuring the health and safety of frontline employees.
As organizations attempt to re-open their workspaces, they can best address emerging risks internally and across their supply chains by implementing a contingency and mitigation action plan that uses powerful, easy-to-use digital information tools for employees and leadership. Enterprise-ready, return-to-work platforms should have a central dashboard of workflow procedures to ensure management makes timely decisions and provides employees with the confidence to return safely to work.
To reduce the possibility of costly disruptions and work stoppages across their supply chain, key personnel and health officials need to have full insight into the wellbeing of those working and visiting their facility. This requires enhanced employee health and safety training focused on the virus and its effects and provides leadership with integrated safety solutions that can be swiftly carried out when necessary.
A comprehensive and effective workplace safety platform provides businesses the risk mitigation structure they need to maintain successful operations at all locations. Organizations can leverage the use of technology, smart solutions and health and safety best practices such as:
CDC questionnaires and mobile temperature checks
Although most employees are increasingly aware of the common symptoms associated with COVID-19, it is important employees report potential health concerns to key HR and health personnel. By answering a daily questionnaire that follows CDC guidance, employees can ensure they are meeting the most up-to-date health standards before even entering a facility.
Using a mobile app, employees can fill out a CDC questionnaire about their symptoms and self-report their temperature. If the questionnaire spots an issue, the employee will be instructed to stay home and set up a medical appointment, while an HR administrator is immediately notified.
On-site thermal scanning and automated PPE check
One of the most telling indicators of COVID-19 is fever. Adopting a no contact thermal temperature scanner keeps employees safe and facilities operational. Employees will be issued a QR code to activate a thermal temperature scan to gain access into the facility. These scanners can detect symptoms and ensure employees, vendors and other visitors are complying with mask requirements before being allowed to enter. This process reduces risks and costs associated with assigning an employee to manually perform temperature and personal protective equipment (PPE) checks.
Contact tracing and distance monitoring devices
While managers may rely on security cameras and spot checks to ensure employees are wearing masks and following social distancing guidelines, distance monitoring and contact tracing enables leadership to detect potential and existing risks more effectively and quickly reduces the likelihood of exposing other employees. Distance monitoring not only informs management who may be at risk based on location but identifies the exact location and duration of any exposures. This location alignment assists leadership in contacting those at risk and carrying out proper sanitation measures.
Wearable devices continually track employees’ movements, recording the distance and duration of interactions and alert individuals in real-time when they are at increased risk. If an employee does test positive, having a contact tracing solution in place takes the guesswork out of which areas were contaminated and who the employees may have interacted with. This ensures exposed personnel are contacted in a timely manner and sanitation protocols are properly performed.
On-demand dashboard analytics
While having tech solutions in place to ensure the health and wellbeing of the workforce is key, being able to respond to risks quickly and effectively will ultimately be hindered if the information gathered is siloed amongst teams. Piecemeal solutions and paper tracking systems can result in miscommunications and bulky administrative processes that can impact an organization and its partners’ bottom lines.
Using a dashboard can help leaders seamlessly track pandemic-related activity across the facility, quickly review temperature checks and CDC questionnaire results, all while keeping data private and secure. The system can analyze the data and issue notifications (text and email) based on information gathered, which is crucial for identifying outbreaks and notifying health officials of a potential hotspot. Additionally, organizations can ensure social distancing measures and local occupancy regulations are being followed. With this insight, organizations can address staffing levels and improve their efforts to promote workplace safety by installing physical barriers, creating new pathways, scheduling staggered shifts and breaks and extending work hours (if needed).
Protecting the supply chain and the rest of the workforce needs to begin before an infected employee enters a facility. By creating a comprehensive health and safety strategy, organizations can efficiently mitigate the spread of communicable viruses and reduce costly supply chain disruptions.