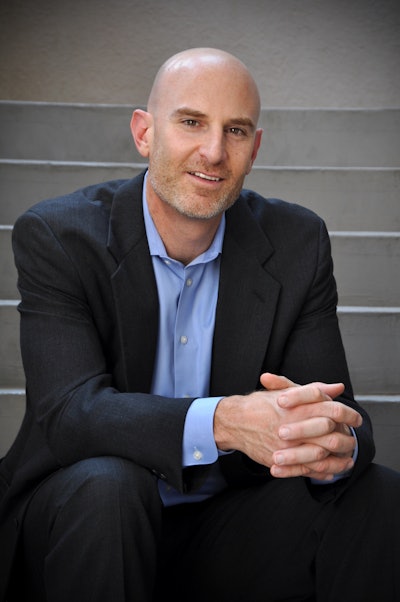
If you're a warehouse manager, you've been in this situation hundreds of times: You know a lot of trucks are going to be arriving at your dock today, but you have no idea when. They could arrive evenly spaced throughout the day or they could all arrive around the same time. This makes it incredibly difficult to effectively plan your labor and equipment needs.
Every warehouse manager wants processes to run smoothly. An efficient operation means lower costs, better morale among staff and happier carriers. But warehouse managers sometimes lack the tools they need to effectively manage the chaos.
As a result, distribution centers are infamous for logistics bottlenecks, where pickups and deliveries are stalled and staffing is a guessing game. According to transportation data gathered by DAT Solutions, some 63 percent of delivery drivers spend three hours or more waiting at a distribution center's dock to be loaded and unloaded. It's no wonder 84 percent of the fleet workers surveyed ranked detention as one of the top five problems carriers face.
But it doesn't have to be like this. The idea of trucks arriving at the loading dock at a predefined time, being efficiently unloaded or loaded, and being sent off in an orderly fashion isn't a pipe dream.
There are plenty of tools that distribution centers can implement to make that concept a reality. You just need to implement the right solutions for distribution's three biggest pain points.
Pain Point 1: Labor Inefficiency
Most carriers and distribution centers do not set specific times for carrier arrivals. That's a guessing game that wreaks havoc on labor scheduling. Are dozens of deliveries going to arrive at once, overwhelming the warehouse and leaving the rest of the shift idle? It's not a sustainable setup for distribution centers or carriers.
The solution lies in better scheduling—and that's a solution that's well within reach. The ability to make, change and cancel appointment times via the Internet is already upon us. You can schedule just about anything online, from haircuts to auto repair, and yes, you can now even do it for freight shipments. Online appointment scheduling software allows truckers to book an appointment for their arrival at the dock. This gives distribution center managers control of the flow of goods in and out of centers, immensely improving the ability to plan resources and maximize labor efficiency.
Plus, scheduling applications can be implemented outside of existing warehouse and transportation management systems. This simplifies the adoption process; users just need to configure the application and start scheduling.
Pain Point 2: Detention Times
For distribution centers, detention didn't stop after high school graduation. Detention in the form of freight waiting times is bad for all parties involved in distribution. Carriers lose money and time as trucks wait in line, and distribution center staff feel the pressure and stress of trying to keep the yard moving. On top of that, having to deal with possible detention fees just compounds the problem for distribution center managers.
One solution that's helping in avoiding disagreements on detention times is the use of electronic logging devices (ELDs). ELDs can track the exact arrival and departure times of trucks entering and exiting a distribution center. This eliminates the he-said-she-said between dock management and carriers, and provides incentives on both sides to schedule deliveries as accurately as possible.
Pain Point 3: Warehouse Chaos
Even the most experienced warehouse manager can't anticipate exact labor needs at all times, so there is going to undoubtedly be a certain amount of chaos on a consistent basis. If trucks are lined up in the yard, it puts a lot of pressure on warehouse staff. The longer truckers have to wait, the more frustrated they become, leaving warehouse employees to load and unload as quickly as they can. And when a paperwork issue or some other hiccup occurs, it can cause the wait to be even longer, increasing the stress and frustration levels for both truckers and warehouse employees.
Tracking arrival times helps in this situation as well, but there's even more distribution centers can do. An additional solution can be found in quality control checklists. When distribution centers require these checklists to be completed in order to receive items, it forces compliance with warehouse protocols and minimizes missteps. These checklists should include directions for how to handle damaged or missing products, or incomplete orders. Solutions are available that keep everyone in the receiving, purchasing and quality control segments updated on every issue being handled.
The process of getting products from manufacturers to retailers and consumers really can be a logistical nightmare. But tools like online scheduling software, ELD systems and quality control checklists can dramatically improve warehouse and transportation efficiency. Even better, many of these tools and systems can be implemented quickly for busy operations that can't absorb a long, costly system integration project.
The good news? Carriers and distribution centers alike share a desire to make shipping logistics more efficient. The tools exist that can allow distribution center managers and carriers to sleep better at night, turning those logistical nightmares into sweet dreams of improved efficiency, lower costs and higher profits.