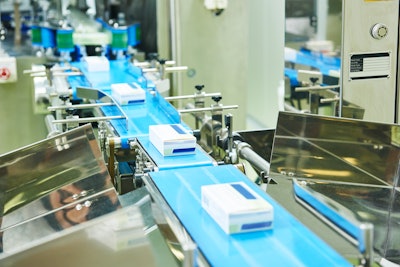
It's been a decade of data deployment for the pharmaceutical sector, thanks to the Drug Supply Chain Security Act (DSCSA). The final interoperability stipulations signed into law in November 2013 are due in a matter of months and must be up and running by November 27, 2023. While the DSCSA has already brought numerous positive changes to the supply chain, even a minor hiccup could throw the entire system off-kilter.
Manufacturers have already implemented serialized product identifiers, readable by both machines and humans. However, potential glitches lurk. Accurately linking products with their respective data throughout the chain, from manufacturers’ origin points to the dispensers’ endpoints, is subject to misalignment exceptions.
The industry has successfully designed and rolled out measures aligning with DSCSA mandates, but an essential next phase is crucial to prevent misalignment. Carrying out tests before the November deadline will greatly reduce future DSCSA-related issues. Besides testing, a holistic strategy that includes heightened drug tracing, adherence to serialization mandates, verification of saleable returns, assurance of electronic systems' reliability and security, and development and implementation of policies and procedures meeting all new regulations will ensure compliance before November.
The Discrepancy Boomerang
Exception handling has the potential to lead to an industry-wide crisis. And exceptions are inevitable. A single misaligned component in the product or data chain can have drastic consequences. If the physical product and its data are inconsistent, the product will be isolated until the discrepancy is rectified, or it will boomerang back to the manufacturer for a reset. Considering the vast volume of prescription drugs traversing the U.S. supply chain, a mere one percent of quarantined products could paralyze the entire industry and result in shortages. These shortages directly endanger patients, who may experience delays in obtaining vital medications.
Testing can pre-empt exceptions before they materialize. The next few months are the ideal time for ensuring data readiness. Consider it a trial run. Ironing out system issues before November will prevent exceptions from arising. According to a 2022 survey by the Healthcare Distribution Alliance, 75% of manufacturers intend to transmit all their DSCSA-required serialized data with shipped products by the November deadline. While there is still much to accomplish, this represents significant progress compared to a 2021 survey, which revealed that only 45% of manufacturers were transmitting serialized data to wholesale manufacturers.
Industry Collaborators: Serialization & Aggregation
Assigning a unique code or identifier to each saleable drug product unit, AKA serialization, provides compulsory verification of serialized products to their respective digital record in advanced shipping notices. Additionally, end-to-end product tracking and tracing throughout the supply chain, from production to dispensing, safeguard authenticity and integrity.
While the DSCSA regulations do not explicitly mandate aggregation, wholesalers are already insisting on it. If a safety issue or defect emerges, manufacturers can leverage aggregation data to promptly identify the cases or pallets containing the affected products and initiate a recall of only those units instead of the entire consignment.
Avert Exceptions Before They Occur
The effectiveness of serialization and aggregation is entirely dependent on the systems in which they're implemented. Audits at every stage uncover potential problem areas. Testing for readability and other functional prerequisites is now commonplace, but comprehensive data audits remain irregular for most.
Even with the industry's best efforts, errors are unavoidable. For instance, a buyer may receive a shipment but not the accompanying serial numbers. Or a seller may send data, but the buyer does not receive the physical shipment. Alternatively, the package serial numbers may not match exactly what's in the pallet. Data corruption is another issue. Each of these instances creates exceptions, and preparing for all possibilities will significantly mitigate the repercussions.
Reduce misalignment exceptions by carrying out tests at every stage, down to the individual serialized unit. By scrutinizing every step, you will not only identify what triggers an exception, but you can also use the test results to establish clear, forward-looking procedures and processes.
A comprehensive strategy integrating risk assessment, clear procedures, technology, documentation, regular audits, communication, education, and contingency planning, will assist in ensuring DSCSA compliance and maintaining a robust and reliable supply chain. You might consider the following steps:
- Verify product authenticity using barcode scanning, RFID, or other authentication techniques at each point in the supply chain.
- Maintain thorough documentation related to the supply chain, including product information, transaction history, and deviations from standard procedures.
- Regularly audit all parties in the supply chain to ensure DSCSA compliance and promptly address any issues.
- Ensure that suppliers and partners understand DSCSA regulations and are prepared to adhere to all procedures.
- Educate employees about DSCSA regulations and offer regular training so they understand the vital part they play in the supply chain.
- Stay updated with any changes to DSCSA regulations and adjust procedures as necessary.
- Create a contingency plan for supply chain disruptions or emergencies, such as a product recall or natural disaster, to minimize the impact on your business and customers.
Boost Exception Rework Capabilities
Manufacturers need to have a comprehensive protocol to identify and rectify exceptions. In the past, packaging operations could repair a damaged physical case or pallet. But now, the issue is both physical and digital. Misalignment exceptions necessitate both physical and digital solutions – as the receiver of medicines will now be reconciling that the physical products match the electronic transaction information sent. Your organization should be ready to understand that an entire pallet could be rejected due to data issues.
Websites, emails and call centers will facilitate communication between trading partners and ensure quick resolution of exceptions. Quick access to issues in the field smooths the product track. Preventing misalignments in the first place is the obvious choice.
Address Misalignments Now
The future holds all the uncertainties. Until November, we can only speculate about where issues will emerge and their true impact. We also don't know how the FDA will respond to exceptions. But one thing is certain: testing is the key to preparation, and addressing issues in the field prevents products from reverting to the manufacturer for the dreaded reset and redo.
- Ensure the effectiveness and reliability of the exception handling process.
- Examine the performance of automated tools.
- Evaluate the precision of exception detection.
- Measure the speed of resolving exceptions.
- Perform checks for consistency between data and products at all levels.
- Carry out audits and tests with wholesalers to confirm simultaneous arrival of data and products.
- Establish who is accountable when discrepancies occur.
- Detect and rectify data handling shortcomings promptly.