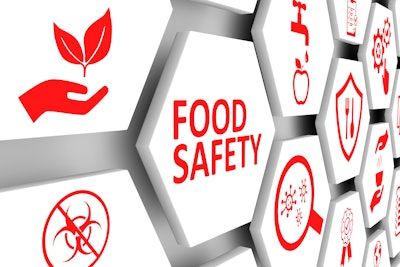
In 2024, a listeria outbreak linked to the Boar’s Head facility in Virginia became a national crisis. At least 10 people died, dozens were hospitalized, and headlines detailed troubling allegations, including 69 regulatory violations, mold on walls, insect infestations, and unsanitary conditions that went unnoticed or unaddressed for far too long. For families impacted, these failures had devastating consequences. For the food industry, it served as a painful reminder that safety gaps, whether caused by human error, maintenance oversights, or inefficient protocols, can have widespread, serious implications. All of which can trigger a chain reaction of tragedy, brand damage, and regulatory action.
While not all warehouse and plant safety risks result in crises of this magnitude, the underlying vulnerabilities are shared across the food manufacturing sector. Unplanned downtime, missed inspections, non-compliance with evolving regulations, and preventable equipment failures all create opportunities for risk. And yet, many manufacturers continue to rely on outdated manual processes or disconnected systems to manage safety and maintenance which leaves too much to chance.
The question today is not whether safety should be prioritized — it’s whether organizations are doing enough to make it proactive, predictable, and data-driven. Increasingly, the answer lies in technology.
Closing the gap between protocol and practice
Food manufacturers operate in one of the most highly regulated industries in the world. From FDA Current Good Manufacturing Practices to the Safe Quality Food Program, regulatory frameworks are designed to minimize risks and protect consumers. But compliance alone does not guarantee real-world safety.
Warehouses and manufacturing sites are dynamic environments where equipment performance, worker behavior, and production pressures constantly intersect. Without centralized oversight, even minor maintenance issues like a miscalibrated temperature gauge, a clogged ventilation system, or a skipped preventive maintenance check can quickly become major hazards.
The Boar’s Head case underscores the dangers of this disconnect. Despite existing regulations and protocols, unsanitary conditions persisted. Technology cannot replace the need for a strong safety culture, but it can ensure that standards are systematically applied, and gaps are swiftly identified.
Technology as the backbone of safer operations
Advanced asset management solutions are no longer “nice to have,” they are essential for reducing warehouse and plant risk. Modern digital platforms bring together maintenance, operations, and compliance data into a single source of truth, enabling a level of visibility and control that manual approaches or outdated technology simply cannot provide.
Here’s how advanced technology is reshaping warehouse safety in food manufacturing:
1. Streamlining maintenance workflows to prevent failures
Preventative maintenance programs are the first line of defense against equipment-related risks. When assets and equipment are well-maintained, they are less likely to break down or operate outside of safe parameters. However, maintenance teams face growing challenges such as labor shortages, complex equipment environments, and reactive service models.
Centralized maintenance management systems alleviate these pressures by automating scheduling and process flows, optimizing labor allocation, and providing technicians with immediate access to the data they need. Instead of chasing down paperwork orders or outdated manuals, teams can focus on executing work efficiently and accurately. Predictive maintenance capabilities take this even further, using data from connected devices and sensors to forecast potential failures before they disrupt operations or pose safety hazards.
2. Ensuring compliance in daily operations
Regulatory compliance is often treated as a separate function and one that is revisited when audits or inspections loom. This reactive approach not only introduces risk but also consumes valuable resources.
Integrated technology solutions automate critical compliance tasks, from documentation and record retention to enforcing safety checklists and generating audit trails. By embedding these requirements into everyday workflows, manufacturers can avoid lapses that lead to fines, recalls, or worse. For example, automated alerts can notify teams when calibration is due or when deviations from temperature or humidity standards are detected in real time.
3. Reducing risk through cross-department collaboration
One of the often-overlooked challenges in warehouse and plant safety is communication. Maintenance, engineering, production, and quality teams must align to prevent issues from slipping through the cracks.
Technology helps to break down these silos. A single, centralized system ensures that all stakeholders have access to the latest safety protocols, equipment data, and work order status updates. This fosters collaboration, speeds issue resolution, and creates accountability across departments which are all critical factors in environments where even minor oversights can have major consequences.
4. Improving response time and mitigating downtime
Even with strong preventive measures, incidents can still occur. In those moments, response speed matters. Systems that provide real-time asset health monitoring and mobile-enabled work order management empower teams to act immediately. Whether it’s shutting down malfunctioning equipment, rerouting production, or addressing environmental risks, digital solutions accelerate response and minimize exposure.
Additionally, by reducing unplanned downtime, these tools protect throughput and product quality. In food manufacturing, where spoilage and contamination risks escalate with every hour of delay, this is both a safety and a financial imperative.
The cost of inaction
It’s tempting to view technology investments in safety through the lens of cost savings and efficiency. However, food safety incidents illustrate that the stakes are far higher. Beyond financial penalties, product recalls, and legal exposure, safety failures erode consumer trust and damage established brand reputations.
On the other hand, proactive technology adoption signals a commitment to continuous improvement and responsibility. It helps manufacturers not only comply with regulations but stay ahead of them, creating safer environments for workers and producing higher quality while having more consistent products for customers.
A safer future starts now
Warehouse and plant safety in food manufacturing will never be “set it and forget it.” It requires constant vigilance, collaboration, and adaptability to new risks and regulations. However, manufacturers are no longer limited to manual processes and reactive thinking.
With centralized asset management, predictive maintenance, automated compliance, and cross-department visibility, technology offers a smarter way forward. As recent incidents have made painfully clear, the cost of preventable failures is too great. By embracing purpose-built digital solutions now, food manufacturers can not only protect their people and products, but they can safeguard the trust and resilience of their entire supply chain.