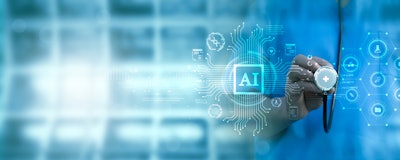
The food and beverage industry is facing significant challenges, particularly labor shortages, which have been exacerbated by various economic and social factors. According to the Food and Drink Federation (FDF), labor shortages have cost the industry an estimated $1.4 billion over the past year. This shortage is not just a financial burden but also impacts service levels in the food supply chain.
The need to reduce waste and optimize throughput
In addition to labor shortages, there is a pressing need to reduce waste of energy and other resources. Efficient resource management is crucial for maintaining profitability. The cost of capital is another critical factor, emphasizing the importance of optimizing the throughput of equipment to ensure maximum return on investment.
Embracing Industry 4.0 in the food and beverage industry
To address these challenges, food processors are increasingly turning to Industry 4.0 applications. This approach leverages advanced technologies to enhance productivity and efficiency. Key principles include:
- Automation. Implementing automated systems to reduce reliance on manual labor and increase precision.
- Interconnectivity. Ensuring seamless communication between machines and systems to streamline operations.
- Data exchange. Facilitating the flow of information across the production chain to improve decision-making.
- Real-time data analytics. Utilizing real-time data to monitor and adjust processes promptly.
- Cyber-physical systems. Integrating physical processes with digital technologies to create a more responsive and adaptive production environment.
The potential of AI in reducing waste
Artificial intelligence (AI) holds significant potential for reducing waste and optimizing production processes. However, AI is data-hungry and requires the right granularity of data to provide meaningful insights. Historically, capturing extensive data was often impractical due to the difficulty in deriving actionable insights in real-time. After the fact information about actual waste versus standard is generally adequate for financial controlling, but process operators need real-time insights to adjust their production runs. AI can provide that because it can manage huge data volumes and more comprehensive sets of data elements rapidly, whereas a human has to simplify the problem. For instance, a cheese-making company previously analyzed yields of the previous week using six data elements like temperature and machine settings. With AI, the company now has immediate insights into 20 factors affecting yield, on a per-batch basis. This helps them to increase yield and achieve a more consistent quality.
Consequently, data collection is becoming increasingly crucial.
Limitations of traditional ERP systems
Traditional enterprise resource planning (ERP) systems are not designed to collect data at millisecond granularity, which is essential for instance to monitor overfill in bottling and packing lines, and a consistent quality in processing.
ERP systems are more suited for managing production orders, cost accounting, and other high-level functions. In the past some food and beverage businesses have added manufacturing execution capabilities to their ERP as modifications. This resulted in technology debt, with outdated systems that are not scalable, for instance managing new factories and growing data volumes. Also, there can be integration and security challenges when wanting to connect to equipment and Industrial Internet of Things (IIoT) sensors.
This is why a growing number of businesses have outlined an application architecture with a prominent role of a manufacturing execution system (MES). The MES sits between ERP and the equipment. The ISA-95 model can help delineate the roles of different systems in the production hierarchy, but in short this should results in a rationalized application landscape in which ERP and MES both do what they are built for.
Seamless integration is essential, with clearly defined integration points and distinctions on which system covers which functions, as well as identifying the system of record for each data object.
Industry suites with vertical specifics in mind
Fortunately, food and beverage processors can adopt a best-practice architecture and deploy an industry specific suite that integrates ERP and MES. This approach accelerates deployment and minimizes associated risks. Requirements differ per sub-segment within food and beverage. For instance, the meat industry has different requirements compared to batch-oriented processing. A tailored approach ensures that each segment can optimize its processes effectively.
In conclusion, addressing labor shortages, reducing waste, and optimizing equipment throughput are critical for the food and beverage industry. Embracing Industry 4.0 and leveraging advanced technologies like AI and MES can drive significant improvements. However, it requires careful planning, investment in the right tools, and a focus on integration and staff development to realize these benefits fully.