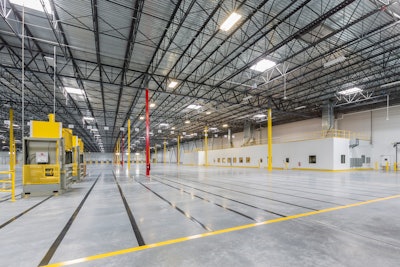
Though we are years past COVID-19 shutdowns, shortages for certain items remain a challenge. With early identification of critical materials—that is, necessary equipment and resources that are at risk of supply chain issues—capital project teams can deploy strategies to ensure those materials are available when needed and projects remain on track.
The process begins with early contractor involvement (ECI), which provides a more complete understanding among all parties of a project’s overall project scope and allows them to come together and examine alternatives and options. It also accommodates early, strategic selection of partnerships. This is in contrast to traditional contractual arrangements, which inherently silo communications among the architecture/engineering team and the general contractors, subcontractors and fabricators.
Once the team has come together, one strategy it may pursue is the use of early release packages to offset materials shortages as well as inflation of prices. Early release packages are part of the preconstruction engagement that identify long lead items and secure commitment dates as well as secure the cost of commitment. Once early design is completed and approved, owners, engineers and contractors can create pre-purchase packages and leverage their established relationships with suppliers and fabricators.
In today’s challenging construction environment, early release packages are sometimes being developed when the design and working drawings are only 30% complete. At that point, the owner and engineer are able to identify critical items. For example, current long-lead items include switch gears and elevators, for which the wait can be two years. By reaching out to the manufacturers of these products while the overall project is still in the design development phase and getting commitments for manufacturing time slots, the long-lead equipment can be fabricated at the same time other sitework is commencing, thereby shortening the overall project schedule.
ECI also ensures that contractors can work with designers and engineers during preconstruction to ensure what is ordered will match the requirements of the completed project design. Running scenarios and choosing supply alternatives may be required to keep a project budget on track. Though it would be impractical to select entirely different critical path materials, experienced contractor partners can compare materials costs to installation methods. The team may opt to design or redesign mechanical systems to use standard shapes and sizes, for example, or switch to on- or off-site assembly. Trusted vendors also can offer alternates by looking at the bigger picture if a challenge in material procurement arises. Though alternates may have a higher upfront cost, they could save money over their lifecycles by being more efficient to the future operator. It’s worth noting that, while the team’s focus may be on the procurement of critical path materials such as steel, joists and decking, lumber, roofing, and piping, it is important to manage the procurement and delivery of all other manufactured materials as well, such as insulation, paint, scaffolding and specialty tooling.
Ensure infrastructure can handle the power load
Lack of available materials and equipment is one type of shortage affecting project teams. Another factor that needs early consideration and planning is the availability of less tangible supplies, such as infrastructure like power and water. Many projects that are common these days, including cold storage facilities, place unprecedented demands on this type of site infrastructure.
Power is a major concern for cold storage facilities. Most facilities are powered by electricity or natural gas and need a reliable source to maintain constant, around-the-clock refrigeration. An unreliable power source can be devastating to a cold storage facility.
In addition to refrigeration requirements, cold storage warehouses have specific and unique temperature control requirements that add even more to the power load. Cold, hot, dry or humid conditions must be maintained. While it may seem counterintuitive, specialty heating equipment must be installed in cold storage facilities. The temperatures required within the facility (which can be -20°F or lower, depending on the items being stored) can freeze the soil beneath the building and cause frost heave, which can be prevented by underfloor heating systems. These systems can be forced air, electric heat or pumped fluid such as glycol.
Capital project teams should assess site utilities and infrastructure to determine their ability to support the high energy demand. Again, early coordination is key. Owners and their general contractors need to reach out to power companies and regional coops early in the site selection and development process, starting with requests for information (RFIs). Today, it is not uncommon for power supply to take 24-36 months.
Most major power companies are responsive to these requests and are more than willing to build relationships with site selectors and economic development organizations (EDOs). Utility representatives will seek to understand a proposed facility’s electrical load, which will include average loads, peak loads, power factors (or the efficiency with which equipment utilizes the power supplied), hours of facility operation, and more. They will then be able to establish how to provide power capacity and what the cost of the power will be. Sometimes a power company will work with the construction team to implement a solution that involves temporary power supplies.
Energy transition considerations, in which renewable energy replaces or supplements fossil-based fuels, may also need to be factored in. Since these alternative types of power delivery are themselves in a state of evolution, this is yet another consideration for the preconstruction team to work through with local utility providers.
Bringing an experienced contractor to the table early, during pre-construction, can help owners plan for challenges in critical equipment and material procurement, as well as meet the high-power demands required by cold storage facilities.