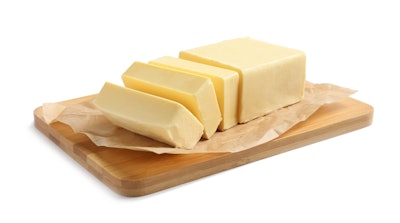
According to the Peace Corps, nearly 1 billion people across the world experience the effects of food insecurity. There are three aspects to food security according to the World Health Organization - food availability, food access, and food utilization. The first area of food availability is dependent on the food supply chain, which has become a punching bag for extreme weather events. Just look at 2023 – natural disasters wreaked havoc from El Niño causing unbridled rice shortages worldwide to Brazil’s droughts stifling coffee bean production. And as long as climate change runs rampant in 2024, the punches will keep coming.
The latest victim: butter.
Extreme weather is predicted for the year ahead, and resulting shortages of food commodities will continue to impact consumers on a global scale. It’s high time business and supply chain leaders move past considering how we got here and take action to minimize, mitigate, and prevent additional shortages.
The perfect storm: climate change meets inflation
Similar to other recent food supply challenges, the ongoing butter shortage was created by a perfect storm of extreme weather patterns and a shifting economic landscape. The record-high heat last summer caused cows to produce less milk, while simultaneously demand increased for dairy-based products. In fact, year-to-date use of dairy products domestically was 8.2% higher, while production and imports only increased about 4%.
On top of that, increased interest rates further strained already limited consumer budgets over the holiday season, meaning shoppers couldn’t afford what little supply was available. To combat these inflationary pressures, shoppers have been forced to make cost-saving switches for their baking needs, looking for alternatives like dairy-free recipes or switching to margarine.
Global warming is expected to continue to have significant impacts on the global supply chain, with 2024 forecasted to be the hottest on record. To navigate these challenges, businesses must pivot their supply chain operations to avoid shortages and minimize costs for consumers.
How to optimize the food supply chain
While better supply chain design and planning certainly can’t fix climate change, it can help successfully manage or prevent disruption through successful inventory planning and optimization. For example, many dairy products like butter or milk have a predetermined shelf life, meaning supply chain planners must be judicious in how many units they have in stock, lest they risk products spoiling before being sold. As a result, stockpiling isn’t an option in the food supply chain.
Instead, supply chain leaders must create a dynamic supply chain system that allows them to engage collaboratively with their suppliers and make quick inventory pivots. Here’s how supply chain leaders can better optimize their food supply chains today:
Manage lack of supply. Supply assurance can be low these days, depending on your industry and the complexity of your supply line. Best practices for a lack of supply include developing alternatives to your primary sourcing plans for key items, proactively revising lead times, and modifying stocking levels to address stockouts, production downtime, and uncertainty in transportation. Regular collaboration with the suppliers with long-term forecasts as well as purchase orders in the short term is also critical to ensure that the supply chain hums along smoothly.
Food and beverage is a classic example of complex supply assurance. By developing new data-driven inventory category strategies for critical ingredients, businesses can better assess their current supply amount. They also set up alternate suppliers to manage risk.
Increase inventory turn rate. A good inventory turn, or the rate at which inventory is moving, is a key indicator of an optimized inventory. To decrease slow-moving or dormant inventory, the best practice is to develop and track an inventory health metric that takes into account the contextual factors that make up the overall inventory performance. Companies must also explore vendor-managed inventory techniques to be more responsive to customer demand.
Digitize operations. One critical component of supply chain preparedness is the use of digital supply chain design technologies, such as a digital twin. This technology offers a digital replica of a physical supply chain that helps recreate a real supply chain in a virtual world so companies can test scenarios and understand how decisions and disruptions will impact their supply chains and business overall.
Such technology allows organizations to cut through the functional silos and build end-to-end visibility into their supply chain. While these tools don’t inherently eliminate risk, they do provide very robust scenario planning with end-to-end considerations, reducing potential delays and constant firefighting.
As the repercussions of climate change continue to impact the global supply chain, businesses must confront these challenges before they reach a critical point. This means expanding beyond their traditional systems, identifying technology partners that provide deeper insights into potential growth areas, and embracing new technology to predict change and work more efficiently with their suppliers.
Ultimately supply chain leaders must engage in collaborative efforts with their suppliers, foster innovative solutions, and commit to digital transformation to create a sustainable supply chain in the face of the climate crisis.