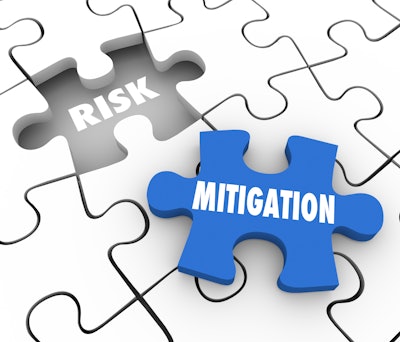
Every day, there are risks to your supply chain–from more visible problems like the continued aftermath of the global pandemic, multiple wars and geopolitical conflicts, the shifting labor market, natural disasters, import/export policies, and local labor challenges. Supply chain risks can come from any direction, up to and including loss of suppliers and diminished carrier capacity.
Recent attacks on ocean cargo ships by rebels in Yemen are causing sizeable commercial shipping vessels to divert from the Red Sea, one of the world's busiest shipping lanes. Ocean shipping lines are diverting vessels away to a much longer journey that goes around Africa's Cape of Good Hope, adding 10 days to the trip. Longer journeys can be detrimental to food shippers concerned with shelf life and product freshness. So, shippers must find ways to get supplies from overseas or use suppliers closer to their processing plants and distribution centers.
Remember during the pandemic when it was hard to buy toilet paper? The food and beverage industry faces various supply chain risks due to seasonality, shelf life and expiration date requirements, consumer demand changes, regulatory changes and compliance, and a focus on food safety. Disruption in the supply of key ingredients or raw materials can impact production and lead to shortages.
Contamination of food products can lead to recalls and shortages. Transportation delays can impact the timely delivery of goods. Properly shipping goods, especially perishables and temperature-sensitive goods, is critical for avoiding spoilage.
Food and beverage businesses must create stringent risk management and mitigation protocols given these risks.
What is risk management?
Supply chain risk management is the systematic process of identifying, assessing, prioritizing, and mitigating risks that may impact the supply chain's efficient and effective flow of goods, information, and finances. Effective supply chain risk management requires a proactive and integrated approach involving collaboration across different functional areas of the organization and close coordination with external partners in the supply chain. By implementing robust risk management practices, organizations can better navigate uncertainties and disruptions, ensuring the resilience and continuity of their supply chain operations.
Within the supply chain, risks need to be identified and assessed. Companies must take a proactive approach to reduce or eliminate the negative impact of risks within their supply chains.
Once risks are identified, organizations need to use supply chain mitigation strategies designed to enhance the supply chain's resilience, ensuring that it can continue to operate smoothly even in the face of unexpected challenges. These strategies include creating contingency plans in case a facility or transportation mode goes away, adding alternative sources of supplies to keep the supply chain operating smoothly and without gaps, optimizing inventory levels, such as adding buffer stock, and using technologies.
Supply chain risk mitigation is an ongoing and dynamic process that requires continuous monitoring, assessment, and adjustment to address the evolving challenges within the supply chain environment effectively.
Technologies in risk management and mitigation
Supply chain network design systems that run and analyze scenarios allow your organization to visualize potential supply chain risks that could transform into significant problems and evaluate options to mitigate the risks. Simulation and modeling tools help in scenario planning and testing of contingency plans. By simulating various risk scenarios, organizations can evaluate the effectiveness of their mitigation strategies and make necessary adjustments. Adding or removing constraints within various supply chain network scenarios helps companies understand the cost, risk, and service outcomes that help guide decision-making.
Advanced analytics tools can analyze large datasets to identify patterns, predict potential risks, and optimize supply chain performance. Predictive analytics can help forecast demand and identify areas of vulnerability.
Artificial intelligence (AI) and machine learning (ML) algorithms can analyze historical data to identify trends and patterns, improving demand forecasting accuracy. These technologies can also be used for risk prediction and scenario modeling to enhance decision-making.
Dedicated supply chain visibility platforms provide end-to-end visibility into the supply chain. These platforms integrate with various systems and provide real-time information on inventory levels, order status, and transportation movements.
By leveraging these technologies, organizations can create a more resilient and adaptive supply chain, better equipped to identify and respond to risks in real time. The integration of these technologies supports a comprehensive and data-driven approach to supply chain risk mitigation.
What is sensitivity analysis?
Sensitivity analysis is an integral part of the supply chain design discipline, allowing users to understand how robust a scenario is when variables such as transportation costs and customer demand change. Designing a supply chain network that incorporates risk management requires running sensitivity scenarios to clearly understand which scenarios will impact your supply chain.
A sensitivity analysis:
● Can create a comprehensive supply chain model that considers all the essential components, suppliers, and production processes involved, as well as associated policies and costs.
● Can identify potential disruptions to your supply chain for each distribution center, looking at several things, such as, disruption recovery time, alternative suppliers' availability, and customer impacts.
● Provides granular detail that accurately shows the complexities and interdependencies of modern supply chains, assessing each disruption's profit impact by considering disruption costs, like lost sales, increased costs, and lost productivity.
● Prioritizes mitigation efforts based on the estimated profit impact of each potential disruption, allowing the organization to focus on the most critical risks first.
In today's volatile market, businesses must ensure that the business can continue to thrive if something happens within their supply chain (loss of supplier, loss of facility, carriers going out of business, merger/acquisition, and more).