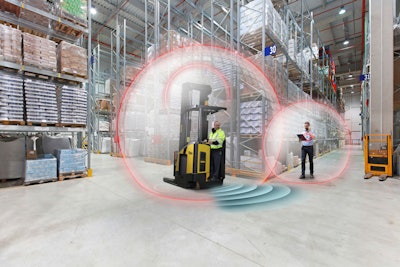
Lift truck operator assist systems (OAS) are often misunderstood. Just another telemetry tool? A magic wand that makes equipment capable of operating itself? Or a cumbersome tool that gets in the way of productivity? High employee turnover and labor shortages continue to strain food distribution and cold storage operations, exacerbating the risk of safety incidents and making it even more imperative for businesses to understand and consider technology tools engineered to enhance operator awareness and adherence to best practices.
Myth #1: OAS is just another name for the telemetry systems that lift truck manufacturers already have on the market.
Reality: The truth is that OAS is an umbrella term that encompasses a variety of products and technologies designed to do exactly what the name suggests – assist operators. It includes telemetry and aids like pedestrian awareness lights and alarms, automatic slow-down, lift lockout and so much more to help operators adhere to best practices that support safety and efficiency.
To further distinguish, telemetry captures and reports lift truck status and usage, providing the data to inform a more reactive approach to managing operator behavior. Features that enable truck monitoring and operator access control can make telemetry an especially useful tool for food distribution operations that need to take steps to enhance visibility and traceability of food products under the Food Safety Modernization Act. Digitization and enforcement of OSHA pre-shift checklist completion can also help isolate potential problems. Other OAS features, however, can take a more active role, providing operators with real-time alerts and automatic performance limitations based on the real-world operating environment, equipment status and load, making it easier to adhere to best practices. Further capabilities of certain OAS tools include line of sight support, location-based fork height restriction, speed controls and more. And while these systems typically implement performance reductions automatically, the operator retains ultimate control of the lift truck.
Myth #2: Having an OAS installed on your truck can risk reduced productivity and decreased throughput.
Reality: OAS is capable of supporting site-specific initiatives AND maintaining productivity, as opposed to prioritizing one at the expense of the other. In fact, fast-paced e-commerce warehouses are well-represented among early adopters of OAS.
In fact, some solutions thrive in warehouses with high throughput expectations. For example, some systems feature in-aisle muting. While lift trucks could be subject to performance reduction if they are in close proximity in main thoroughfares, the narrow nature of tight warehouse aisles means equipment cannot maintain the same distance. In practice, the in-aisle muting capability can allow two trucks to work in the same aisle without slowing each other down.
Myth #3: OAS is typically limited to ultrasonic technology for object and pedestrian detection, so it cannot register all potential hazards in the environment.
Reality: Many companies and OEMs use different technologies to detect objects, pedestrians or both. Technologies such as lidar, ultrawideband (UWB) and ultrasonic are all popular for these applications. Some OAS solutions are unique because they can use either single or multiple means of detection, depending on the goals and needs of the specific warehouse application.
Myth #4: Object and pedestrian detection only work in the path of travel and if the object or pedestrian is standing straight up or vertically.
Reality: While vision technologies like lidar and ultrasonic sensing can detect obstacles in the direction of their orientation, trucks equipped with certain OAS can be configured with multiple sensors to enable detection in the appropriate direction depending on truck and obstacle location. But what about unseen obstacles, such as a truck hidden inside of racking?
Some systems offer line of sight support that uses UWB technology to account for and react to objects equipped with a powered badge within a certain radius, a valuable feature for busy operations like those in food distribution – you don’t want to miss a pedestrian about to step out of the end of an aisle as a truck approaches. Lift truck speed can be slowed to a crawl based on location-specific rules as a way to discourage operators from entering certain areas, such as designated pedestrian zones, aisles, doorways and tunnels.
Myth #5: OAS reduces truck performance only to avoid obstacles.
Reality: Sure, it’s common for an OAS to enable features that help operators avoid hitting obstacles, such as reducing speed if an obstruction is detected or in response to location-based rules at intersections or high traffic areas. However, another hazard is operators traveling quickly around corners, risking a tip over. While some OAS offerings may reduce speed when making turns, certain systems offer true lateral stability when cornering, decelerating equipment based on the combined center of gravity of both the truck and load.
Myth #6: OAS provides only audible and visible alerts.
Reality: Most OAS solutions deploy beeping sounds and flashing lights for various situations, but those can get lost in a loud and busy warehouse environment. What if alerts went a step further, enabling operators to “feel” what’s happening?
An advanced OAS adjusts the truck’s performance in real-time, alerting operators through the feeling of performance reduction, such as limited speed or an inability to raise forks. For example, when entering a zone designated as having heavy pedestrian traffic, the system proactively reduces travel speed to help alert the operator and improve situational awareness.
Myth #7: An OAS can expand load capacity, allowing trucks to go beyond their maximum load capacities.
Reality: OAS does not enable extra load capacity. Instead, these systems help lift truck operators avoid lifting loads that exceed the lift truck’s capacity limit.
Some OAS offer a feature that automatically stops lifting if load weight exceeds the truck’s threshold. Rather than simply telling operators they are lifting a load that is too heavy, such a system actually prevents them from doing so.
Myth #8: OAS only applies performance controls based on other trucks, objects and pedestrians that are connected to the same technology.
Reality: While an OAS can use a network of ultra-wideband tags to sense equipment, personnel and infrastructure, a technology like lidar can offer an extra layer of detection to sense obstacles in the path of travel even if they are not connected to the same network of tags.
Certain systems leverage both lidar and ultra-wideband tags for detection. Some can also offer a real-time location sensing option using the same proximity tags together with beacons to enable location-based rules like equipment exclusion zones and end-of-aisle slowdown.
Is it right for you?
OAS technology helps warehouses boost efficiency and adherence to lift truck operating best practices. But as with any new technology, figuring out what makes sense for your food distribution operation requires digging into details. A conversation with your lift truck dealer or manufacturer can help you to get a better understanding of how the technology may be a fit for your particular facility and goals.