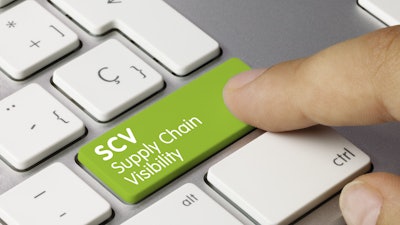
Customers' growing demand for greater transparency and sustainability in the products they consume is transforming food logistics. Customers are increasingly interested in the origin of their ingredients, the business practices across the value chain and the impact their food could have on the environment.
The food industry is becoming extremely competitive to meet the eccentric customer demands. Today, with newer business models and the entry of heavily funded startups, food market leaders are accelerating the introduction of autonomous and self-healing supply chains to address these short and long-term challenges and retain their market leadership.
The autonomous, self-healing food supply chain
The food value chain, often an ambient temperature-controlled or cold chain operation, is the most vulnerable type of supply chain. It has more moving parts than a non-temperature-controlled one, and therefore more potential for breakdowns. In addition, food supply chains face higher pressure than pharma supply chains to optimize for cost while maintaining product quality.
Cold chain management presents several unique challenges that must be addressed to ensure the safe, automated, sustainable and efficient transportation. Some of the most common problems include the following:
● Automating environment condition regulation throughout the supply chain is critical to guarantee product quality and safety. However, temperature control can be challenging due to factors such as weather conditions, equipment failure and transportation delays requiring real-time intervention that’s preferably system driven.
● Managing the right packaging for the correct journey and season to protect sensitive products from temperature fluctuations during transportation. Packaging, especially the reusable type that also improves sustainability, can be expensive and may not be readily available in all areas of the supply chain.
● Automated control tower operations can help resolve complications in multimodal orchestration, long transit times and complex customs and regulatory requirements with minimal overheads. However, today’s control tower operations are often manual and unproductive owing to lack of deep insights in real time within the network.
Automation needs more than visibility; it requires intelligence
The first step to automate is to create an efficient food supply chain operation, or else the inefficiencies get magnified too. Efficient operations can only be created through actionable intelligence built on reliable visibility. A major drawback with existing supply chain analytics tools in the market today is that they rely on manual (inaccurate), untimely and unactionable source data. While this provides a rough picture on location or condition, it is highly unreliable for automating power decisions.
To get reliable visibility and actionable intelligence, companies need a combination of healthy visibility data and artificial intelligence (AI)-powered analytics to gain deep insights into their supply chain operations and make swift informed decisions. Healthy visibility data requires accurate, timely, firsthand sensor-driven signals.
With healthy visibility data and AI-powered analytics, swift informed decisions can be made to optimize their processes and reduce the risk of product spoilage and waste. According to a report by MarketsandMarkets, the global predictive analytics market was valued at $10.5 billion in 2021, and it is projected to reach $28.1 billion over the next five years, driven in part by increasing demand for predictive analytics solutions in the cold chain management industry.
Building intelligence on healthy visibility data
Getting accurate, timely, first-hand visibility powered by sensors is only 25% of the problem solved. To build an autonomous supply chain using AI, it is important to follow these three steps to achieve real-time data:
● Step 1 – Deriving contextual business signals from location and condition visibility to effectively orchestrate a supply chain. Simply knowing that a temperature excursion occurred is meaningless. An example of a contextual business signal is informing stakeholders whether or not the shipment will pass quality control on arrival, days before it reaches its destination, so that corrective measures can be initiated to ensure usable stock on shelves.
● Step 2 – Generating prescriptive and predictive network analytics for rapid optimization of food logistics. With increasing supply chain disruptions combined with eccentric customer demands, planning cycles need to be much shorter. By analyzing historical data on their supply chain operations, companies can use predictive analytics to identify patterns and trends that can help them anticipate potential issues before they occur. For example, a large European chocolate manufacturer improved their cold chain compliance from 59% to 85% in just one season by identifying the Top 20 out of its 93 lanes that caused more than 50% of their cold chain compliance risks.
● Step 3 – Building a self-healing digital twin. With the right type of insights and foresights in the food supply chain operation, a virtual replica of your entire operation can be created with the power of AI and machine learning for specific applications. “What if” scenarios on-time, in-full, in-quality order fulfillment by lane, region, or distributor can be modeled in real time to automate or ease logistics decisions.
Building a data-driven culture enables companies to streamline their food logistics operations and gain end-to-end supply chain visibility that is reliable and actionable. It is essential that businesses empower their teams to improve supply chain visibility with data intelligence to help identify flaws, optimize processes for efficiencies and automate for repeatability and gain competitive advantage.