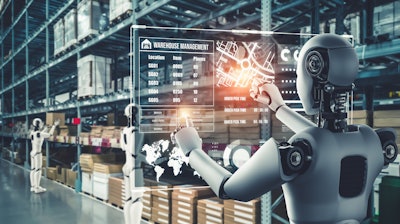
Despite the cozy fireplaces, hot beverages and festive retail displays, the season of perpetual hope may find itself running afoul of the Grinch of Christmas Past (and Present)—the global supply chain.
Though mid-November through the New Year is truly a magical time, the holiday season is not precluded from hardship. Food manufacturers worldwide are still facing unprecedented raw materials shortages. Alongside dwindling supplies, many companies are still grappling with unseasonably high labor shortages. With customer demand and consumer expectations making their holiday ascent, manufacturers may find themselves scrambling for direction in this winter’s wonderland. To get their bearings, however, business leaders need only look to a facility that thrives under tight timelines, welcomes unpredictable demand and undoubtedly pulls off miracles.
Enter the smart factory, an operation that will always achieve near-perfect, on-time and in-full percentages despite any exterior challenges or shortages.
Without the automation of sorts, how can food manufacturers emulate this smart operation? Think smart solutions and the optimizations they enable.
Address raw materials shortages with dynamic workflows
Enter the great peppermint shortage of 2021. While unhappy consumers had to lean into new holiday flavor profiles, the ramifications for the manufacturing industry were far more significant.
Confectioners—their supply of sugars and dyes teaming in preparation for the winter surge—found their goods spoiling as they waited for a key ingredient that would never arrive. Reduced production resulted in reduced order fulfillment, which ultimately, left shelves in stores bare.
Now, an ideal scenario would see companies not be taken by surprise by a material shortage. While foresight into an issue does not abate it entirely, it does give companies the agility they need to adjust production accordingly, thereby maximizing their efforts and staving off as much damage as possible. Fortunately, today’s smart solutions make enabling this level of operational foresight more feasible.
When it comes to enabling operational agility, dynamic process workflows play a crucial role. Built out by production teams and fed by mission-critical assets and infrastructure, dynamic workflows help ensure manufacturers can operate as effectively as possible within their given circumstances. Via integration with warehouse management solutions, these workflows provide real-time insight into raw material levels, which helps guide shopfloor teams toward an optimized production schedule that minimizes waste and spoilage. Taking into account job-by-job quality levels, runtimes and overall performance, dynamic workflows give teams the insight they need to optimize material consumption, reduce scrap and maximize yield. In a scenario where raw materials are scarce, ensuring that as much of a rare item as possible makes it into finished goods as opposed to a wastebasket is a necessity.
Mitigate labor shortages with smart technology
Dynamic workflows have been added to the “nice list.” Now, what if a company is struggling to hire or retain the number of people required to tend to and execute said workflows? With U.S. manufacturing expected to reach 2.1 million unfilled jobs by 2030, businesses grappling with a lack of skilled and general laborers has become a prevalent plight. Fortunately, smart solutions can help mitigate this challenge as well.
When it comes to operating with a less-than-full staff, ensuring every team member is able to work as efficiently and effectively as possible is paramount. Capable of monitoring real-time line-by-line performance, asset performance and runtime, team member performance and availability and more, smart scheduling solutions give departments the power to make the most informed and impactful schedule possible. Beyond that, smart solutions can also help augment employee tasks and workloads and minimize existing skill gaps. With their ability to automate manual tasks, provide seasoned team members the ability to create and implement standard operating procedures (SOP) and provide factory workers with intuitive, data-fed dashboards, smart solutions help manufacturers stave off the worst of the labor shortage impact.
Through adopting efficiency-boosting technology, manufacturers also gain the opportunity to invest in new career pathways and improve employee retention. Companies across industries are consistently finding new ways to incorporate technology into their operations, and digitally integrated generations like Millennials and Zoomers are keen to use job opportunities to gain valuable experience working with state-of-the-art technology. As they continue to embrace digitalization, manufacturers gain the ability to provide their existing and inbound workforce with opportunities for professional growth and development—a sought-after benefit in today's rapidly evolving digital world.
Preempt high consumer expectations with communication
While all of the benefits mentioned above are sure to help food manufacturers, the true benefit of smart solutions lies in their ability to facilitate communication. Communication, not just across facilities and departments, but across the value stream. Communication that empowers raw material providers, sets realistic goals and timelines for production teams and tempers the expectations of customers and consumers alike.
Producing fewer goods will lead to more vacant shelves in stores worldwide, yes. However, if expectations are set, and manufacturers—after communicating clearly with their upstream and downstream partners—know they have done their best, then perhaps the grace that flows so freely during the winter solstice will extend its warm reaches to them.
This season, it is the supply chain. Next year, manufacturers may be staring down an entirely different abominable snowman. No matter how things play out, one thing is certain: for as long as there is manufacturing, there will be challenges that arise and seek to derail it.
It is true—today's manufacturers can't solve their problems with a mystical workshop manned by a prolific workforce. What they can do, however, is embrace the miracle of smart technology, utilizing its array of tools to create a smart operation all its own.