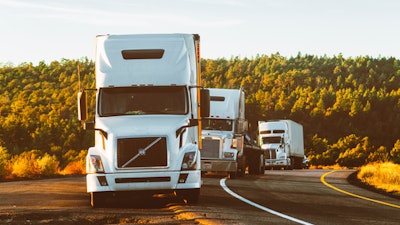
The practice of winterizing any food distribution fleet today has changed drastically from even just five or 10 years ago. Gone are the days of adjusting each truck based on historical perceptions or just going on experience.
Today’s advanced maintenance data analytics and technology have equipped progressive distributors with the tools and resources to make more informed decisions, eliminating the need for guesswork. Furthermore, while many fleets must begin to make adjustments in October and November, winterizing today is actually an annual process built around seasonal preparation.
This is especially critical during the holiday season when grocers need on-time deliveries for the increase in seasonal shopping, and even in January and February for large gatherings.
Everything begins with a comprehensive plan
All that being said, food distributor fleets and their maintenance/technician departments must have a plan – not just for the winter, but for the entire year. Everything starts with preventative maintenance (PM) and the ability to calendarize the PM plan. Maintenance prepared for and performed in the spring and summer will have a different focus than that of winter, and distributor fleets must be able to identify the trends and areas that colder climates may affect more so than in warmer climates.
For example, a fuel filter that has some water in it in April and May won’t offer any problems. However, that same filter in November and December will be a completely different story if you’re operating north of I-70. This can result in a breakdown on the side of the road, which affects everything from driver morale, safety, routing and other costs such as on-call maintenance.
Setting the appropriate annual plan will be vital to establishing the proper PM checklist at different times of the year.
Pay close attention to fuel systems
Another critical area to focus on is your fuel system. Many maintenance professionals and technicians still look at it as a filter, but today it’s a complete system. In the winter months, trucks move into higher idle applications. For many of today’s trucks we talk about a five-minute idle set. Still, the reality is that the truck allows a five-minute idle after it reaches normal operating temperature. Therefore, that increased idle during the winter months is going to cause additional soot to enter the diesel particulate filter (DPF) and can impact the entire system.
More specifically, you have the seventh injector, which inserts additional fuel for the engine burn. There is also the filter, which includes the crossover pump, as well as the fuel blend which has great consideration. Food distributors can see as much as two- to three-tenths MPG reduction during the winter months, not only from the change in fuel and different blends, but also cold tires, cold transmission, cooler fluids, etc. Therefore, a truck that typically reaches 7.3 MPG drops to 7 even if you’re doing everything correctly.
Changing tires can’t just be based on muscle memory
In addition to fuel, tires are a major expense for food distribution organizations, and preparing your winter plan can be significant here. As winter approaches, many distributors may consider running their rear tires back to 4-32 treads. There is this perception that since there will be snow and ice on the road, technicians must hurry up and change the tires. The reality is the traction between 4-32 and 8-32 is very minimal. However, each tire change can bring additional expenses, and distribution fleet managers must be cognizant of this. It’s essential to leverage sophisticated PM and tire data and analytics and solid KPI metrics from the OEM and dealer to ensure tires are only changed under the right circumstances and seasonal timing instead of just going on perception or a hunch.
In addition to accurate data, distributors and their maintenance departments must have the appropriate technology to properly and continually make assessments in accordance with their annual PM plans. Years ago, the first thing a technician would do when inspecting a truck was to change the oil. However, today’s technicians are plugging a laptop into the diagnostic portal. By doing so, you can check critical areas of the truck that may show certain areas in the fuel system or tires to identify areas that could have a problem and perform more preventative work – even before a check engine light appears.
Properly communicating cost breakdowns to the C-level
All of these decisions can potentially cost the companies several thousands of dollars each year. And when you multiply this by 40-60 trucks, you’re talking a significant amount of money eroding the organization’s bottom line. Fleet managers and maintenance crews must have an open line of communication with the executive suite so that planning and expenses can be discussed together.
A solid plan and detailed line-item visibility can make all the difference in the world in front of the executive team. Distributors and their fleet personnel should be able to address leadership and say, here's what we foresee happening; this is why maintenance costs have seasonality; this is why our tire cost is rising in the fall; this is why our fuel cost is rising; and here's what we plan to do about it. What’s more, today’s analytics and data technology can help demonstrate these cost changes.
When food distributors combine a comprehensive annual plan with today’s sophisticated data analytics and maintenance technology, they can keep their trucks on the road more and drivers safe during the winter months while helping the executive suite preserve the bottom line.