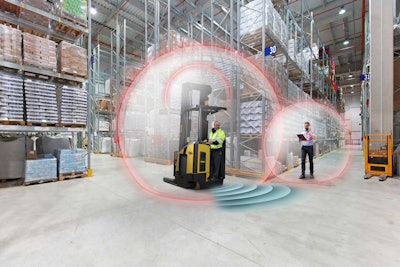
From electricity to smartphones, there is no overstating the impact technology has had on the world. As its name makes clear, some of the most important inventions from the Industrial Revolution – from the steam engine to the spinning jenny – had transformative effects on industry. More recent advances in technology have continued that tradition, redefining not only the consumer goods sector, but also the means of production, including warehouses.
Today’s warehouses are increasingly characterized by their adoption of technology and automation. RFID tags track inventory. Sensors detect anticipated failures in components or systems to proactively alert maintenance teams. Robots navigate independently throughout facilities. It’s clear - this isn’t yesterday’s warehouse. And that’s born out of necessity - the challenges that today’s operations face, from a turnover-prone labor pool to higher order volumes and faster delivery expectations, demand intelligent functionality from all critical equipment, including the lift trucks that keep busy warehouses moving.
To keep pace, facilities can’t settle for the same, tired equipment. They need next-generation solutions, with smart designs and technology integrations engineered to help increase throughput, decrease total cost of operation and empower lift truck operators. Here are five forklift technologies that will enhance performance in the food industry’s warehouses in the year ahead and beyond.
Stability control systems
Where there are humans, there is the risk of human error, including lift truck tip-overs and other incidents that can cause spills, contamination, injuries and damage to equipment or facilities. Some stability control systems can help reduce the likelihood of these incidents by limiting truck performance in certain conditions to help minimize forward and sideways tip-overs. Stability control systems use sensors to continually monitor the truck’s center of gravity automatically implements measures to support stable travel, such as reducing truck leans in turns to help improve lateral stability, producing a smooth deceleration by limiting truck speed around corners based on how tightly the truck is turning, or limiting the truck speed when handling an elevated load raised above a certain height. This additional layer of feedback can be a helpful tool to help reinforce proper lift truck operation already established during operator training.
Operator-assist systems
Other advanced operator-assist technologies have emerged that enable an even greater range of equipment controls to help reinforce lift truck operating best practices and support operator awareness. Whereas a stability system like the one described earlier primarily monitors the center of gravity of the truck, certain advanced operator-assist systems continuously monitor the combined center of gravity of the truck and the load. When the system detects that it needs to reduce truck performance to help support stability, it can dynamically apply a tailored rate of deceleration that considers that combined center of gravity. This kind of technology also goes another step beyond the stability control system described earlier, by monitoring and responding not only to real-time information about the equipment, but also the operating environment. This can include proximity to pedestrians and obstacles, and custom location-specific rules that a business might establish for their warehouse.
So, what exactly does that mean in practice? Warehouses can configure a system like this to automatically adjust truck performance, such as speed or lift, based on truck stability, facility rules and when navigating around obstacles, people and other trucks. For example, the technology can be used to automatically slow trucks as they approach the end of an aisle, intersections, other pieces of equipment and obstacles, or even limit speed to prevent equipment from entering designated areas. It can also limit hydraulic function to help operators lower elevated loads more gently and controlled, to help prevent product damage. These functionalities may be practical for helping to prevent costly injuries, spills, food contamination and damage to products in fast-paced food distribution facilities, depending on the specific application.
Telemetry
Food warehouses are also benefitting from solutions that can take guesswork out of their operations. Under the Food Safety Modernization Act (FSMA), operations are required to take steps to enhance the visibility and traceability of food products. Telemetry systems that provide real-time monitoring of lift truck and operator locations can help optimize visibility. These systems can also provide clear, actionable data that can help operations to prioritize safety and productivity. For instance, telemetry systems can equip supervisors with impact detection, alerts and other data to help inform additional operator training, facility layout adjustments and traffic flow. The systems can also be used to restrict truck access to approved operators only, track operator training updates, digitize pre-shift OSHA checklists and more.
Notably, these technologies are not meant to replace a strong operator training program. Rather, think of them as complements - training teaches operators best practices, stability control systems and operator-assist technologies help reinforce the best practices learned in training, and telemetry empowers managers to continuously audit performance.
Robotics
Around the world, businesses are turning to robotics to help augment their labor pool and reduce operating costs. Robotic lift trucks can help cut those expenses by up to 70%, however, those savings are far from their only benefit. For food warehouses, robotics can automate a number of repetitive tasks, such as moving finished products to storage or shipping areas, accurately racking pallets and moving them away from receiving docks to make room for new arrivals and replenishing manufacturing lines running low on raw goods. Because robots follow programmed site-specific rules of the road such as maximum speed or minimum distance from pedestrians or objects, they can help to reduce the risk of accidents, collisions or other safety incidents when compared to lift trucks with human operators.
Advanced power sources
For years, many food warehouses have relied on lift trucks powered by lead-acid batteries, which can pose the risk of incidental contact between food and potentially dangerous acid, fumes or spills. However, the landscape of motive power options for lift trucks has expanded to include newer electric power sources such as lithium-ion and hydrogen fuel cells. Because they generate zero harmful emissions, these power sources can allow operations to mitigate contamination risks and reduce their environmental footprint. They can also help food operations realize other substantial benefits, such as increased uptime and productivity. The fast charging of lithium-ion batteries, and refueling, in the case of hydrogen fuel cells, can allow for more uptime compared to the more labor and time-intensive process of changing lead-acid batteries, which can take 20 minutes or more each time. Whereas multiple lead-acid batteries may be needed to power a truck over the course of multi-shift operations, the one-to-one power source-to-truck ratio of lithium-ion and hydrogen can also allow facilities to repurpose valuable indoor space that might otherwise be used for lead-acid battery maintenance and storage. Finally, lithium-ion and hydrogen offer consistent power, regardless of whether the charge or fuel level is high or low, whereas there is a noticeable drop-off in power as the charge of a lead-acid battery is depleted.
Adopting technology purposefully
As tempting as it can be to jump at the chance to bring a new technology into your warehouse, it remains important to evaluate whether it’s a good fit for your operation. A trusted partner like a local lift truck dealer can help you understand how to best implement the technology in your facility. They can also help navigate as the characteristic progression of technology introduces the next wave of warehouse solutions.