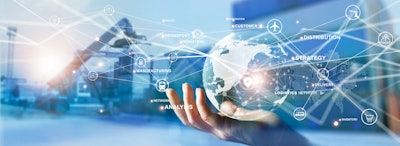
Consumers today expect to get what they want when they want it – whether it’s ordering something online that can be delivered in a few days or going to the grocery store to shop fully stocked shelves. However, the COVID-19 pandemic changed all of that. It exposed the vulnerabilities of the global supply chain and required logistics companies to quickly adapt to continue to move products and goods throughout the world.
Over the last two years, while some businesses have become experts in shipping logistics because of the supply chain crunch, other companies have been pushed outside of their comfort zones to try to find alternate ways to get their products to market. This inconvenience unfortunately created more challenges and issues for businesses such as increased costs, elevated inventory and evolving risks.
Supply chain efficiency is essential in business and delays and bottlenecks are friction points for an already stressed supply chain. While many factors contribute to supply chain issues, the main ones are demand, material supply, bottlenecks and labor shortages.
At the start of the COVID-19 pandemic, as demand for many goods diminished and manufacturing facilities shut down, the supply chain remained idle. However, as countries reopened and people purchased more goods instead of services, demand skyrocketed and manufacturers could not re-open quickly enough to meet this increase. On top of that, a shortage in materials added another layer of complexity to manufacturing and an equipment shortage made the situation more strenuous. This is because companies were trying to operate with existing machinery and tools, while simultaneously investing in and waiting for more advanced or more environmentally friendly technology.
Bottlenecks and shipping delays
Bottlenecks throughout the supply chain can cause extensive delays and port inefficiencies are a major cause of the supply chain bottleneck. If ships get held up at a port or can’t unload cargo quickly, the delay has a rippling effect on the supply chain. Some ports, such as the Port of Long Beach, are investing in newer equipment like environmentally friendly autonomous cranes to help improve efficiency. However, it will take more than a year for these cranes to be built and delivered, which means the ports will continue to face logjams. Although these investments in port infrastructure have been happening, it has not been able to keep pace with the growth in size of container ships and demand during COVID-19.
Shipping and logistics problems
Aside from delays, businesses face unique risks and other problems with shipping such as costs, lost cargo, damaged cargo and goods, world events like political unrest and environmental regulations. It is important to remember that it is not just the product owner that faces these risks. Logistics companies are also exposed to various liability risks.
Typically, companies rely on ocean freight to transport goods. In fact, the majority of global trade goes through ocean vessel because the cost for air freight is exponentially more than shipping by sea. The other big difference between ocean and air freight is speed. Shipping goods on a plane means they will reach their destination faster than traveling by sea. Because of this, using a cargo plane is generally reserved for more expensive goods or perishable products.
However, when supply chains were significantly delayed and disrupted during the height of the pandemic some businesses were unable to rely on air freight because of cost, as well as storage space and weight. A shipping container can be 20- or 40-feet long and can hold a lot of materials. With air cargo, goods are traveling by pallet. The physics of a plane can’t hold the same amount of weight as a shipping container. Unfortunately, it is not possible to just flip a switch and immediately start using air freight.
In the future, some businesses may start relying on air freight because of supply chain dependencies since the only way to solve this problem quickly is with air freight. Companies may also begin to rely on air freight as online orders increase and people choose not to go to a physical store. Though, it is expensive to do this and ties into inflation as the cost for goods for the consumer will not be the same.
Insurance to help protect supply chain
Given the delays and issues in the supply chain, businesses and logistics shipping companies face unique risks. Although some of these risks were present before the pandemic, alternative measures for freight travel can create new exposures. If a company decides to charter their own vessel instead of working with a logistics shipping company, they are entering into a different agreement. It is a channel they would not normally go through, so they must think about the risks involved. It is why businesses need to make sure their insurance coverage is up to date.
In addition, while there are bottlenecks at ports, there are also bottleneck issues on the inventory side. As companies and manufacturers have increased production to get goods to consumers, it has created an increase in inventory that they must store. Companies may be accustomed to having $100 million in inventory, but now may have $300 million in products in their warehouses. This increase in inventory has a direct impact on insurance premiums because there is a significant increase in the number of products the company is holding. Therefore, insurance coverage has to change to protect the inventory. It’s a ripple effect.