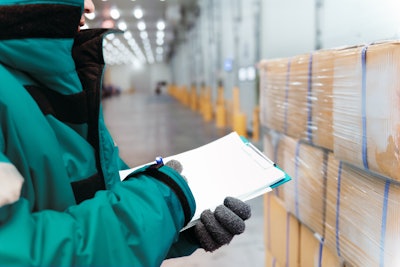
TV dinners are making a comeback. Thanks to the pandemic, there has been a measured surge in the purchase of cold foods stored in the home refrigerator and freezer. In fact, according to a report by the American Frozen Food Institute (AFFI), 70% of consumers have bought more frozen food than usual, and 7% of customers who have purchased frozen foods since the onset of the Coronavirus disease (COVID-19) had claimed they didn’t purchase frozen foods pre-pandemic.
This change in buyer shopping patterns is having a direct impact on grocery stores and their inventory levels, leading to a domino effect of results. First, with the increase in frozen food purchases and the skyrocketing price of fuel, consumers are making fewer trips to grocery stores. Due to the long shelf life of frozen foods, customers are purchasing in bulk when they do make the journey to shop in-person, leading to low stock on store shelves and an increase in inventory in the home. And because customers at home have more food, many are even buying second storage units.
Initial concern over this consumer buying behavior shift has transferred into cautious optimism in these recent months as companies look to automate and digitize operations and processes up and down their supply chains, and a critical piece in those adjustments is the implementation of automated storage solutions. Many operators are shifting from older, less efficient, traditional facilities to meet these new customer demands as well as reduce operating costs associated with older-dated refrigeration technology and building systems.
Just-in-time vs. carrying more inventory
Most corporate leaders have been trained to reduce inventory carrying costs. With supply chains historically showing itself to be more stable, the concept of just-in-time (JIT) delivery of parts or ingredients grew to become the mainstream solution. Incentives for large volume and long-term contracts, coupled with the prospect of stiff contractual penalties, provided reason for sub-contractors to deliver their crucial materials consistently and often. But they were not ready for the world events of the past couple years.
The pandemic and associated supply and demand shocks have not been kind to the JIT philosophy. As geo-political risks increase, companies are contemplating stock levels and reorder points. With respect to automated systems, building a larger capacity system may be a risk mitigation strategy, and one that also makes financial sense. Additional capacity is generally spent on items such as racking, i.e. those elements of a system that do not wear and need to be maintained, or carry higher operating costs. An increase of automation investment may not actually be necessary, which has the effect of reducing the cost of an automated storage retrieval system (AS/RS) from a per pallet or case position standpoint.
Just be smart
With the rise in demand for frozen foods, operators need to accommodate the increase of cold and frozen storage demand. This demand can put a strain on the operations, and managers who deploy automation are using it to their benefit. A few example steps they have taken include:
- Adding rack. Don’t be afraid to invest now. Adding rack to an automated system will reduce the cost per position. While it will require more spending upfront, it will ultimately lead to better value. After all, with more storage rack positions tied to automation, the more value is achieved. Also, static structures require no maintenance and should last 40-plus years.
- Pre-picking orders. Allowing automation to pre-stage orders can pay dividends and improve truck turns. Those activities would normally lead to extra manual touches, but these can often be handled through automation without much or any additional cost.
- Becoming denser and smarter. While this mantra sounds simple enough, building denser largely depends on the number of SKUs and lot codes. Optimum storage depth is determined by analyzing the inventory levels per SKU and other variables, so consult with a proper automation expert first to see if this trend is right for you. If so, it even enables sites (like those situated in more urban areas) to be chosen that may not otherwise be applicable.
The benefits
Ultimately, the goal is to have a system that guarantees reliability and consistency with growth factors included. By implementing automation into a warehouse, the benefits will quickly follow, including:
● Enabling growth. A lot of companies have limited space and need to solve the inventory problem differently. This is especially true with frozen foods where the cost of space is high. By automating and taking the suggested steps above, businesses can improve performance and be prepared to react to a myriad of scenarios. Not only can they increase capacity, but they can also reduce the dependence on difficult-to-find labor.
● Savings in energy consumption. Automating a warehouse is an ideal way of going green. Take a vestibule in a cold storage automated system, for example. Because it is so tight and small, the energy cost associated with refrigeration can be reduced by up to 70%. Every time you open the door, there is no longer a big rush of air that normally leads to significant cooling loss.
● Increased speed. Conventional facilities, when they go large, take up a lot of real estate. Naturally, this leads to lower productivity as the distances erode performance and increase dead-head moves. By properly designing and implementing a denser, higher, automated system, the long travel distances are eliminated, and those manual moves that remain tend to be short and highly productive.
With summer approaching, those refrigerators and freezers will have a steady rotation of steaks, frozen meals and popsicles, so grocery stores must be prepared. As warehouses push forward to deal with those inventory demands, an automated approach to the next expansion project should not be overlooked.