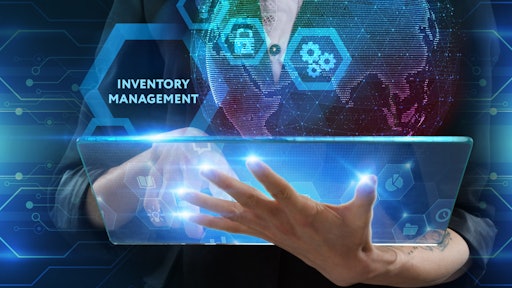
Supply chain disruption in recent years has raised the profile of inventory management, and a lot of firms have made significant investments in this area.
At the same time, great claims are being made for Artificial Intelligence and its ability to optimize various supply chain challenges, including inventory optimization.
But between the hype and the somewhat vague terms used, what is the real state of inventory management and inventory optimization? This is a personal view of the current state of the industry in early 2024.
Let’s start by defining some terms. The phrase inventory management is usually used to describe one or more of three things:
- The physical management of inventory in warehouses or factories and in transit
- The various planning and scheduling processes that define when materials are ordered, manufactured or shipped
- The definition of inventory policies or targets that will influence the two process areas above
There is normally no single business function managing all inventories directly. Rather, the inventory held is the result of a combination of business processes from procurement through to sales, with a significant role being played by various supply chain planning and execution functions.
Warehouse Management
The physical management of inventory is an area that has seen enormous progress over the last two decades. As the third millennium dawned, it was not uncommon for goods shipped from the other side of the world to arrive before the associated paperwork, and annual stocktakes would routinely discover long lost stock. Planners could be working with a drastically inaccurate impression of how much inventory they had available and how much was on the way. The advent of barcodes, RFID, fully automated warehouses and GPS tracking, for those who use them, has made massive improvements to companies’ ability to know how much inventory they have and where it is.
Furthermore, these ID-driven warehouse functionalities also enable significant process improvements, from correct stock booking and rotation to advanced picking and packing optimizations. Once data is homogenous and accurate, you have a solid foundation on which to attempt more complex optimizations.
Supply Chain Management
Things get more complicated when you zoom out a level and look at whole supply chains, even within a single company. Most big multinationals have more than one instance of their preferred ERP system and a variety of legacy systems to boot. Even without this fragmentation, many systems are inflexible and it is still surprisingly hard to generate useful management information from them.
In this area, good progress has been made in the last 5 to 10 years in supply chain visibility solutions. Software that pulls together data from disparate systems and enables useful overviews has transformed organizations’ abilities to manage their inventories at a macro-level, which has proven particularly valuable in times of disruption.
While not everyone is fortunate enough to have the latest technology solutions at their disposal, on average inventory management has seen great advances in the last two decades. What about inventory optimization? Here the picture is less positive.
Inventory Optimization
It is always useful to define inventory optimization as the term can be used more or less precisely. The basic concept is that “optimal” inventory levels minimize the inventory held while meeting target service levels. Inventory optimization could therefore reasonably be defined as the process of managing inventories to be in that sweet spot between excess and shortage. The problem is that this describes almost any inventory planning process. With a few exceptions, no one plans to have too much or too little.
In simplistic terms, inventory planning involves looking at what inventory is held, what is needed, and then making decisions about ordering or manufacturing more. The fact that this definition is simplistic doesn’t mean the process is simple to do well. Visibility of what inventory is held and, on the way, can still be problematic for many, while what is needed is, in most cases, dealing with the future and some kind of forecast. Many discussions assume that if those two variables (current inventories and future demand) are known, then inventories are simple to optimize.
However, a stricter definition of inventory optimization recognizes it as a statistical concept that depends on a much larger range of variables, all of which are in a more or less constant state of flux. Optimal levels depend not just on forecast accuracy, but also on variability (both on the demand and supply sides), intermittence, distribution of demand, lead times, shelf life, minimum order quantities, capacity constraints, and so on.
Inventory optimization requires advanced statistical techniques and therefore can benefit greatly from technology solutions. However, unlike some of the other inventory management technology mentioned above, inventory optimization tools and functionality are not yet delivering on their promise.
There are various reasons for this. One is complexity. The variables involved in optimization calculations are numerous, as are the circumstances, and models which work well in some instances do not work in others. This makes automation risky. A related problem is transparency. Most solutions are poorly documented and poorly understood by end users, which makes them difficult to trust. Another is data quality. Optimization calculations rely on a significant number of data inputs, which are typically of varying or poor accuracy.
This is not to say that inventory optimization solutions are bad. Rather, the current situation is that it requires significant effort to get value from them, certainly more than some of their sales materials would suggest. Enterprise buyers are rightly wary of those offering simple solutions to complex challenges, whether it be AI or some other buzzword. However, as this short overview has sought to demonstrate, progress has already been significant in the inventory management technology space and there is no reason to believe that this shouldn’t continue as optimization solutions continue to improve.
Making Inventory Optimization a Reality
It is also essential to realize that technology alone will not solve the problem. Many organizations still use sub-optimal planning processes, have planners ill-equipped to make the most of advanced analytical solutions and have grossly misaligned incentives across the supply chain. A more holistic approach is required to transform inventory performance.
Macro-indicators show that despite the technological advances made over the last two decades, average inventories across industries have not come down over that period of time. While inventory optimization is not the same as inventory reduction, the high average levels of inventory are a sure lagging indicator that inventory optimization is still much discussed but little realized.
How soon can we make it a reality? Time will tell.